The Case of the Low-Efficiency Beacon
August 31, 2011
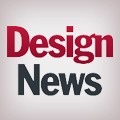
Nearly 20 years ago, when I was working for a rail signaling company, we were manufacturing mini-beacons. These were transponders that were bolted to railway sleepers. They transmitted brief data to the onboard train-protection system as the train passed over. They were powered from the 27mhz train transmitter and responded with data modulated 4.5mhz. We received beacons periodically from the customer that required testing and sometimes repair. They were in a harsh environment: vandals, tamping machines, vibration, coal dust, lightning, etc.
The electronics of the beacon were potted in gel and silicone. Then it was sealed with epoxy. If we needed to gain access to the components, we could run the router over the whole cover or just the section that was deemed to be at fault.
We noticed a trend of low efficiency in the standard test with numerous returned units. They were about five years old. The efficiency of the transponder was its ability to generate specific power supply volts and RF output under the test condition.
After some testing, dissection, and PC board substitution, we determined the electronics were OK. We checked the manufacturer's test data, and it showed the units were no different from any others in the same batch.
So the remaining contributor to the problem could be either the antenna or the housing. The antenna was constructed from mil spec PTFE (polytetrafluoroethylene) dielectric coax cable that was molded in the polyester resin and glass fiber housing. It was not likely to give the time-related faults that were noticeable. So we focused our attention on the housing. We dissected one into various parts with a saw and a carbide Dremel bit.
Once it was exposed, we could see the polyester had differing density areas by color and hardness. We performed some low- and high-voltage resistance tests on the suspect areas, and we found the problem was most prominent where the fiberglass was embedded in the polyester. We baked the housing pieces to remove moisture, and conductance returned.
We determined the conducting substance was the cause of the low efficiency. It was compounded by moisture and pollution absorption. The molded housing was a mixture of polyester resin, fiberglass, and mineral powder. This problem could have been caused by less-than-adequate mixing of the molding ingredients. Tests on the mineral powder showed no conductive result in its new dry state. Although there was no fix for the sick beacons, at least we knew the cause of the failed units.
This entry was submitted by Toni Graham and edited by Rob Spiegel.
Tell us your experience in solving a knotty engineering problem. Send your story to Rob Spiegel for Sherlock Ohms.
About the Author(s)
You May Also Like