The Adventure of the Persnickety Peltier
December 10, 2009
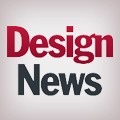
Engineers are perplexed when an analytical instrument passes all earlier stages of design validation, but flunks the final testing stages
By K. Ghosh, Contributing Writer
As a senior engineer, I am occasionally called upon to review designs done by our junior designers. We design and manufacture analytical instruments and pretty often land into peculiar situations which need careful review of the design right from scratch.
One such situation involved the design of an instrument which had a small copper chamber to be maintained at 27°C, 30°C or 36°C for different situations. The chamber was maintained at the required temperature by a Peltier, which cooled or heated the chamber as needed. The requirement was the temperature accuracy needed to be +/-0.5°C and should be reached within 5 minutes.
The instrument was in its final testing stages, having passed all the earlier stages of design validation, when two problems were observed. One, it behaved fairly within specifications in the air-conditioned design lab where the ambient temperature was roughly 27°C. When taken out of the room at ambient temperatures of 30-35°C, the instrument was unable to reach 27°C at all. Second, if the top cover of the instrument was in place, the lower temperature of 27°C was unreachable even within the design lab. Since these problems had not been seen in the earlier stages of the design, I was called in to provide some solution.
The copper chamber was cooled by the Peltier and in turn the extracted heat combined with the heat from the Peltier was removed by a heat sink (a block of Aluminium with fins). The first suspect was the interface between the copper chamber, the Peltier and the heat-sink. I had to know if the interfaces were transferring the heat efficiently. For this, I decided to decouple the assembly from the rest of the system, both hardware and software. I hooked up the Peltier to an external source of power and connected it to cool the copper chamber. I gradually increased the power through the Peltier and observed the temperature of the water in the copper chamber. I was easily able to go down to a steady 18°C within about four minutes, with the ambient at 32°C.
Knowing the power input to the Peltier, and the Peltier and heat sink thermal characteristics, I was able to calculate the temperature difference across the interfaces and they matched the theoretical calculations done earlier. So, the interfaces were not the culprit.
Next suspect was the thermistor, giving the temperature feedback. Was it showing the right temperature, was it calibrated? This area had a lot to be checked. The output of the thermistor itself. The analog output of the thermistor was converted to digital with an ADC (Analog to Digital Converter). Was the ADC doing its job? After conversion, how were the readings interpreted by the software?
The thermistor was operated under a constant current source. This checked out fine. So, I logged the voltage from the thermistor circuit for different temperatures and this too matched my calculations. The converted digital values from the ADC were also logged and checked out as expected.
So, I turned my scanner to the software which generated the PWM for the Peltier. If steady DC power could cool the copper chamber so effectively, was enough power not reaching the Peltier in PWM mode? Or, was the interpretation of the feedback of the temperature the culprit?
The software controlled the time period for which the power to the Peltier was applied. Depending on the temperature feedback from the thermistor, the software decided the on-time period and the direction of the power through the Peltier. Two LEDs (Light Emitting Diodes) distinguished the duration and direction of power flow, red for heating and green for cooling.
I observed the LEDs under different conditions of the instrument operation. If the ambient was 27°C, and with the top cover of the instrument removed, the copper chamber reached its set point of 27°C within 4 minutes and the LEDs would alternately glow, with the green remaining on for a tad longer than the red. So, the software was doing its job.
As the ambient increased, the red LED grew fainter while the green grew brighter. This meant, the software was directing increasing power to the Peltier and in the cooling direction. So, the copper chamber’s temperature must be increasing. Measurement confirmed the observation. If increased power was passing through the Peltier and in the right direction, why was it not cooling further?The same was observed with the top cover of the instrument in place. The copper chamber was able to coolat first but could not keep the temperature down. The temperature would drift up and the green LED would glow furiously. Removing the top cover would allow the copper chamber to slowly come down to its desired27°C. So, what was the link with the top cover?
I had had a chance to see the instrument in its design infancy, but had moved onto other projects later. I noticed now the top cover looked different to what my memory recalled. The curvature was different and the exhaust fan was definitely smaller now. Inquiries revealed the truth. The top cover had initially been designed for a certain internal volume, but later was passed onto the Industrial designers, who gave a curved look to the instrument, in the process reducing the internal volume of the instrument. Because of the curvature, the exhaust fan on the side of the instrument needed also to be scaled down in diameter, resulting in reduction of the amount of air flow through the instrument.
While heating to above the ambient was no problem, it was when trying to cool, that troubles started. As per thermodynamics, to cool an object, heat must be removed from it. But then, heat can only flow from a hotter body to a colder one, and not vice-versa. In this case, the Peltier was operated in such a way, that, while cooling, it presented a cold surface to the copper chamber, thus drawing heat away from the chamber into itself. On the other side, the heat from the hot side of the Peltier was transferred to the heat sink, which in turn dissipated the heat to the air surrounding it.
Now, when the top cover was not in place, the heat sink had no difficulty in dissipating the heat to the surrounding air, which then moved up due to convection currents, allowing cooler air to replace it. Therefore, the Peltier was able to transfer heat away from the chamber and thus cool it properly.
When the instrument had its top cover on, the air surrounding the heat sink was restricted in mobility, and soon attained the temperature of the heat sink, impeding further heat flow. The exhaust fan did not help, since it had been downgraded. Within the confines of the design lab, it worked because the ambient temperature was lower and it took more time for the air inside the instrument to get heated up to the point where it impeded heat flow. That was the reason, the temperature of the chamber would drift up from 27°C even within the design lab, if the instrument was given enough time to operate. And indeed, it did take about a half-hour or so for the temperature to slowly start climbing up.
Increasing the power flow through the Peltier did not help because, like any other electrical device, a Peltier also has its own internal resistance, and normally, the heat generated inside the Peltier has also to be removed by the heat sink, to allow the Peltier to cool. Heat generated in the Peltier is mainly governed by the current flow through it and for a certain level of current, the heat generated internally by the Peltier can become equal to, or more than, the heat removed by the heat sink. From this point on, instead of cooling, the Peltier would start heating !
Okay, so the root cause has been established, but what to do for the solution ? Obviously, the air inside the instrument needed to have better circulation around the heat sink and also the heated air had to be replaced by fresh cold air from outside the instrument. Changing the exhaust fan was out of the question, since it would change the overall look of the instrument and marketing pamphlets had already been circulated.
Finally, I had to place a small fan at the bottom of the heat sink to assist the convection air-currents, so hot air near the heat sink was forcibly moved up and colder air could take its place. Also, the exhaust fan had to be replaced by one with the same diameter, but with a different blade design, so it moved more volume of air at a lower rotating speed (RPM). This was important, to restrict the amount of audible noise generated now by the two fans. Finally, some more ventilation holes on the bottom of the instrument were added.
About the Author(s)
You May Also Like