Stopping the Gulf of Mexico Oil Flow
June 29, 2010
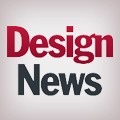
By David Greenfield, Design News Editorial Director
Engineers voice their ideas on how to remedy the BP oil disaster on Design News’ System & Product Design Engineering social media site.
One of the most active discussions currently on Design News’ System & Product Design Engineering social media site is a post originated by Contributing Technical Editor Jon Titus that asks: How would you stop the Gulf of Mexico oil flow? (You can access this site and this ongoing discussion directly by visiting http://bitly.com/designnewsLI.)
Considering the disastrous nature of the oil spill, it seemed more than appropriate to spotlight some of our readers’ opinions on how to address this issue in our Calamities column.
One of the first suggestions posted to the site following the failure of the top-kill attempt came from Roderick Whitfield, design engineer at R. Whitfield Assoc. He isn’t sure the top-kill approach itself was a failure, but rather that BP erred in its selection of materials with which to carry out the top kill. “They just pumped in the wrong materials with the drilling fluids (metal and rubber),” Whitfield wrote. “If we are getting sand-based asphaltic nodules washing ashore, the same types materials such as an asphaltic-compatible material could be pumped into the drilling fluid after a controlled drilled relief well is drilled.” He adds that this step would best be taken after first completing a study of the subsurface geology and the hydrology to determine “where to best relieve the pressure to slow the flow so that it can be capped and controlled also.”
A hydraulic solution was suggested by Howard Hurley, owner of Alacarte Engineering. “I would fashion a hydraulically actuated, three-jawed carbide-tipped apparatus that, when actuated, would push against the walls of the pipe, digging in to lock it into place,” he wrote. “This could be hydrodynamically designed to make it possible to shoot it into the well to a thousand foot depth or so. Once the jaws were tight against the sides of the pipe, the hydraulics could be used to start blocking the flow. Once the flow was blocked significantly and a pressure head was built up, a flow of sealant could be introduced to block the well at a reasonable depth.”
Based on past experience with heat shrinkable materials while working at Raychem (now part of Tyco), Lee Dudley, president of Diamondback Technology Inc., suggests the use of Nitinol which was formed into a coupling to stop a North Sea oil line break. According to Dudley, “The metal is fabricated into the required shape, (in this case) a coupling, and expanded and cryogenically frozen. When it warms to a temperature above freezing, it recovers (actually a crystalline transformation from Martinsite to Austinite). The volumetric change results in a strain of about 6 to 8 percent which would provide a clamping force of 60,000 to 100,000 psi.” This is plenty of force to “weld” the open valve in place, Dudley contends.
“If you look at the video (of the exposed pipe gushing oil into the Gulf), you will clearly see that the cut in the riser pipe was about 8-10 inches from the bolted flange,” wrote David Hoenig with DH Technical Consulting. Based on the video image, Hoenig suggests strapping a two-halves clamp collar below the flange as the holding device for any caps. The flange would take all the possible load for which it is designed to handle. The outflow pressures could also be addressed with a “monstrous” ball valve (that would be kept open) until after strapping (on the collar).
While it’s clear there are no easy answers to this situation, design engineers certainly possess the knowledge to approach the problem from a perspective that considers all the material and environmental issues that must be addressed to develop an effective solution. We all hope that an answer will soon be found and effectively deployed. Until then, this discussion will remain up on the System & Product Design Engineering group. Your contributions to the conversations ongoing on this site are always welcome and appreciated.
About the Author(s)
You May Also Like