Squeezing Cost While Raising Quality
September 27, 2012
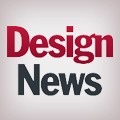
I was working on a new connector design for 50 ohm impedance-matched coax connectors for Automotive Digital Satellite Radio receiving at 2.33 GHz. This application was very sensitive to electrical performance, with low insertion losses (i.e. a low impedance discontinuity, low dissipation factor, and low reflections from impedance mismatches), but was also very cost sensitive. The target electrical performance was compared with SMA connectors costing $25 each, but our target terminated cost was $1 each!
The SMA had screw machine components with PTFE Teflon insulators with dielectric constants around 2.1; gold-plated contacts and cable using foamed or expanded PTFE Teflon dielectric; a silver-plated center conductor, and dense outer braid and FEP Teflon jacket. Just the Teflon insulator was over my entire target cost! The less expensive engineering plastics usually had 3.4 to 4.5 dielectric constants which would increase my insertion loss and grow the size of the connector unacceptably to match the impedance.
My marketing was able to back off on the high-heat thermal capability requirements, to where we could use cable with the same center conductor, foamed polyethylene dielectric, cigarette wrap foil and loose braid, and polyethylene jacket. These material and construction changes provided better electrical performance at about 1/20th the cost per foot.
The connector optimization was more difficult. I created tables for a range of dielectric constant choices. This table created a sub-table at each dielectric value with a range center terminal outside diameters and outer conductor inside diameters. I then changed the color of all the corresponding characteristic impedance values in the table within +/- 2 ohms of nominal as green and +/- 5 ohms as orange printing. I could then visualize the sizes of my components for each dielectric choice down to around 1.0 for the dielectric constant of air.
This last observation kept striking me as so great electrically, and free. I came across articles in trade magazines of using ceramic discs as air/vacuum gap insulators in coax cables in space. Then it struck me (my aha moment) -- I could use cheaper nylon or polyester insulators, molded to hold the center terminals on ribs, and the effective dielectric constant was approximated as interpolated based upon volume of air at close to 1.0 and Nylon at 4.5 dielectric constant.
This further saved material volume, allowed use of much cheaper materials that could be injection molded instead of machined, and provided even better electrical performance than full density Teflon! If I targeted a slightly lower characteristic impedance, I could even tune and tweak the exact result by reducing the mold core sizes, effectively taking away air and increasing the dielectric constant. This worked like a charm. I also used deep-drawn brass outer shells at a much lower cost than diecast outer shells with an intermediate contact spring assembled.
We met our cost target, and we outperformed our competitor's connector that we estimated to have a much higher manufactured cost.
One other benefit of the "ribbed" insulator design was that it lent itself to injection molding, rather than machining. The core pin tooling in the molds became more robust than a skinny little pin. The mold builders were much happier with the tooling on the mold with this revised concept, the mold processing was much easier (larger process windows without damaging the core pins), and mold maintenance was much less frequent (cheaper).
—This entry was submitted by David T. Humphrey and edited by Rob Spiegel.
David Humphrey has a BS in mechanical engineering from the University of Delaware. He started working in the electronic connector industry right out of college, and has worked for various connector manufacturers over the past 22 years. This has included roles of manufacturing engineering, product engineering, application engineering, and design development engineering. Over the last 10 years, he has worked for Dentsply, an OEM dental equipment and supplies manufacturer, in various operations manufacturing engineering roles.
Tell us your experience in solving a knotty engineering problem. Send stories to Rob Spiegel for Sherlock Ohms.
Related posts:
About the Author(s)
You May Also Like