Selecting Vibratory Feeders and Conveyors for Food Applications
How to properly select vibratory equipment to effectively handle bakery and other food items
August 13, 2021
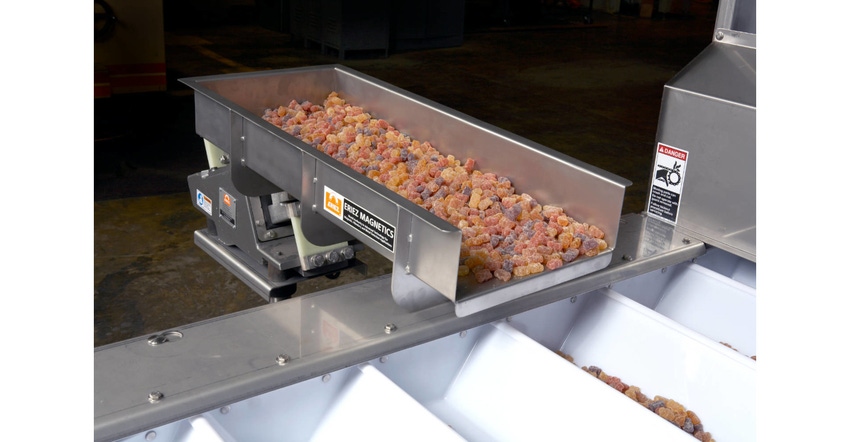
Linda Mioduszewski, senior technical sales representative, Eriez
Vibratory feeding and conveying equipment have been used in bakery and other food industry applications for several decades. This article will assist plant managers and equipment operators in properly selecting vibratory equipment to effectively handle bakery and other food items.
Overview
Vibratory feeding and conveying equipment can efficiently handle a broad range of bakery and other food products, such as fine powders, tacky materials, granular materials, and bulk products. This equipment is utilized to assist in adding ingredients to mixers and blenders, metering to downstream process equipment, screening oversized or fine debris from final products, sprinkling salt, sugar, or various seasonings, and on-demand supply to the packaging process.
Prior to a conveyor moving the product along each step of the processing facility, a feeder meters the amount of material that is placed on the conveyor to ensure the flow is not disrupted. On a vibratory feeder, the feeder’s amplitude moves the material up and forward, allowing it to drop to the surface at a point further down the tray. Multiple vibratory feeder or conveyor designs are available, each with a different amplitude, frequency, and angle of deflection to suit the process requirements.
Manufacturers continue to advance the design of vibratory feeders and conveyors to evolve and meet the food industry’s safety needs and regulatory challenges, such as following guidelines for Safe Quality Foods (SQF), Good Manufacturing Practices (GMP), and sanitation requirements. Government policies and industry standards also require bakery and other food industry facilities to install equipment that meet construction specifications as outlined in programs like a company implemented Hazard Analysis Critical Control Points (HACCP) program, the Food Safety Modernization Act (FSMA), and the Global Food Safety Initiative (GFSI).
Compact feeders can convey raw or moist product like cheese during a food processing operation.
Areas where vibratory equipment can assist the food and bakery industry include:
* Baking or freezing
Vibratory feeder and conveyor models are available for high-temperature installations with ambient temperatures approaching 300°F and cold temperatures approaching frozen at 20-32°F.
* Screening for fine debris and oversized material removal
Vibratory equipment adapts easily to the addition of a screening function during the conveying process. Common applications include “scalping” or removing oversized material from the product and “de-dusting” or removing fines from the product.
* Metering material at a controlled rate
In a processing plant, vibratory feeders are commonly used to meter material into downstream processing equipment. The vibratory feeder is the bulk metering device to provide material at a controllable, easily adjusted rate.
* Automation
Variable voltage controls allow integration of vibratory feeders or conveyors into automated processing or packaging applications. Remote on/off, and signal following/voltage regulation capability through a PLC with 4-20 Ma DC signal or 0-10 VDC are available.
* Cleanliness and sanitation
One of the primary benefits of vibratory feeding and conveying is the clean nature of the construction of a conveyor or feeder tray. With no complex geometric barriers, the conveyor and feeder tray can be easily and quickly wiped down or washed out for product changeover or sanitation procedures. If screens or tray covers are required, these components can be designed as quick removal items utilizing fasteners that do not require tools for removal.
Product contact and product zone weld and surface finish upgrade options are available to comply with USDA, FDA, and other industry standards.
Choosing the Right Feeder
High-speed feeders are an excellent choice for applications where fast travel speeds and requirement for the feeder to start and stop frequently per process demands are necessary. These units are ideally suited for packaging applications.
High-amplitude/low-frequency feeders and conveyors are the typical choice for handling light and bulky, fine powdery and flexible products, including cereal, flaky and powder spices, potato chips, raisins, gummy candy, and more. These units are the preferred choice for adding a screening function to the conveying process.
High-stroke mechanical conveyors are well-suited for high-capacity applications that require longer conveying lengths and/or intermediate discharge gates.
Optimizing Efficiency and Product Consistency
Consistency and quality of a finished product is integral in the food industry. Electromagnetic and electromechanical feeders and conveyors offer food processors several opportunities to improve their facility’s efficiency:
* Electromagnetic feeders under a hopper allow for ingredients to be supplied to blenders and mixers with ease.
* Electromagnetic scarf plate feeders can sprinkle finely granular material like salt, sugar, and seasoning onto snack food or baked goods traveling on a belt conveyor, ensuring consistent coating on product.
* Electromagnetic vibratory conveyors can be used as a transfer device to move product from the processing area to the storage or packaging area.
* An electromagnetic bin vibrator on a hopper or bin wall can aid in the vertical flow of products.
* Adding a screen deck to an electromagnetic vibratory feeder or conveyor can remove oversized material or fine debris from the finished material.
* Adding a hopper above an electromagnetic feeder (a.k.a. volumatic feeder machine), can be used in conjunction with weigh scales, batch operations, and operations where additive feeding is performed either continuously or intermittently.
Electromagnetic Feeders Versus Mechanical Feeders
Electromagnetic feeders and conveyors can be utilized in continuous process operation, constant on/off process operation, and to convey traditionally difficult-to-feed products.
Electromagnetic feeders and conveyors can also adjust to changing process requirements with voltage input adjustment to the feeder through use of a variable voltage control or automated signal following control.
Electromechanical feeders and conveyors continue to be a popular choice for a variety of feeding and conveying applications where continuous operation is the process requirement. Mechanical drives utilize traditional motors with eccentric weights or motor vibrators to create the vibratory force required to excite the feeder or conveyor tray. Electromechanical feeders and conveyors typically operate at a low frequency and high amplitude. While mechanical feeders do not offer the same level of feed rate control as an electromagnetic design, they are effective for handling higher capacities and longer tray lengths. Mechanical conveyors can be a cost-effective means to move material over distances longer than 10 ft.
Endlessly Customizable Tray Designs
The shape, length, and width of modern feeder and conveyor trays are practically limitless. Customers can order trays with custom features to satisfy their unique process requirements. Every configuration of flat, curved, v-channel, and tubular designs are available. Trays are typically fabricated from stainless steel for food applications.
Trays that include features such as a tray cover or screen deck incorporate quick-release fasteners that enable removal of these components without tools. Once fasteners are loosened, the component simply lifts and disconnects from the tray for easier cleaning.
Instrumentation for Feeder or Conveyor Monitoring
There are various equipment options that intelligently track the operation of feeders and conveyors and provide verification the equipment is responding appropriately. They prevent equipment damage in upset situations. An over-deflection monitor is one such piece of equipment. The monitor detects changes in tray deflection due to conditions such as material sticking on the tray surface. As material accumulates on the tray surface, it adds weight to the tray, affecting performance and possibly damaging the feeder. The monitor alerts, warns, or shuts down the feeder so the tray can be cleaned. This improves performance and reduces costly downtime.
Additionally, electromagnetic feeder controls can operate in a “closed-loop” mode that make automatic feeder adjustments to maintain tray vibration under various conditions. For example, if material builds up on the feeder tray surface, the tray deflection is typically affected. If a closed-loop control is utilized, the vibration level is constantly monitored and the control automatically adjusts the power to the feeder, ensuring the tray vibration level does not change.
Conclusion
Technology advances make vibratory feeding and conveying solutions more applicable than ever for food and bakery industry environments. Sanitary construction, ease of cleaning, low maintenance, and latest design features make these units an ideal choice for facilities where greater product purity, energy costs savings, decreased equipment maintenance expense, and streamlined manufacturing operations are desired.
Linda Mioduszewski is senior technical sales representative, Eriez. For more information, call 814-835-6000 or visit www.eriez.com
You May Also Like