Pressure Sensing Integration in Portable Devices
February 15, 2011
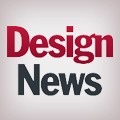
A growing number ofOEMs are opting to incorporate MEMS-based pressure sensing components intoportable device and equipment designs. As a device designer, it's important torecognize that the choice of pressure sensing type within these applicationstends to be highly specific to the intended operating characteristics of boththe sensor and device itself.
For example, a handheld,battery-operated spirometry device must be able to be turned on and off quicklywhile continuously recording data over a 20-second period with optimized use ofavailable power. Based on these requirements, it requires a low-voltagepressure sensor which is able to use power only as needed. In another instance, pressure sensors for handheld HVACmonitors, due to their portability and manner of use, cannot be overlysusceptible to vibration or position changes, which could ultimately affectmeasurement integrity.
Pressure Sensing Integration in Portable Devices _A |
Among the varioustypes of sensing technologies available for these types of applications, low-voltagedie-based MEMS pressure sensors offer some of the greatest advantages withinportable devices, including high-reliability performance and extended usefulservice life. This is particularly important for environments characterized bya wide dynamic temperature range, or where external shock and vibration ispresent. In addition, these sensors can be isolated from internal deviceelectronics, offering added protection from signal degradation as a result ofthermal transfer.
Low-voltage MEMSpressure sensor components are comparatively lower in cost and offerhigh-quality mass customization and production capabilities. When integratedinto assembled portable devices and equipment, they can help achieveexceptional measurement linearity and repeatability, with minimized powerconsumption and extended service life.
Performance Characteristics
When selecting anappropriate pressure sensor for integration into a portable device, you shouldunderstand a sensor's own unique performance characteristics as they relate todevice operation requirements, as well as the unique operating conditions ofthe intended device usage environment and collective potential effects ondevice performance. Following is an overview of these considerations from adevice design perspective:
Sensor Die Design - A typical MEMS pressuresensor is constructed of a body, or "die," and a thin silicon diaphragm withfour surface piezoresisA-tors, whose resistance changes in response to mechanicalstress. They are generally arranged in a bridge configuration and are preciselylocated on the diaphragm surface to maximize deflection response. In doing so, pressuredifferential response is maximized across the diaphragm. MEMS pressure sensor quality and performance within an applicationenvironment is most directly tied to sensor die quality.
Pressure Sensing Integration in Portable Devices_B |
PackageSize - By definition,a portable device is characterized by its ability to be easily transportableand with on-demand functionality. This typically calls for compact pressure sensordesigns which offer performance stability, low voltage requirements, and which canreliably operate in a lightweight, easily transported package. Thus, whenincorporating pressure sensing technologies into portable device designs,compactness is a near-absolute requirement. The space constraints within thedevices themselves impose certain limitations on sensing technology optionswithin these types of applications. Sensors must not only operate within asmall package, they must also be isolated from the internal device electronics toavoid signal degradation.
While traditional low-pressureceramics products are still in use to satisfy these requirements within somesmaller device applications, they are design prohibitive for portable devices,as size and weight remain major considerations. Equally important is for thesensor to be compact enough that it will not cause stress on the sensor packagewithin the assembled device, as this affects overall output signal accuracy,ultimately effecting overall device performance.
Temperature Variation - Operating temperature variations can also have a direct affecton MEMS pressure sensor offset voltage and output span, and can ultimatelyaffect overall measurement stability. Portable device applications typically requireuse of a pressure sensor that can reliably operate in moderate temperature excursionsof 0 to 50C, though certain operating conditions can require more extensiveranges. Portable oxygen concentrators are an example of a device featuringintegrated pressure sensors that are used in relatively moderate temperatures,though some models may require a sensor with wider, industrial-leveltemperature ranges of -20 to 85C. To meet these varying range requirements,manufacturers frequently look for a pressure sensing technology with eitheruser-adjustable or integral temperature compensation options.
MEMS-based pressure sensing componenttechnologies are commonly offered with customer-applied temperature compensationcapability, which allows manufacturers to tailor temperature performance totheir own device performance requirements.
Sensor Output and DeviceStability - Sensor output sensitivity isanother parameter that will impact signal strength at a particular operatingvoltage. Higher sensitivity devices can typically be operated at lower voltageswith less signal degradation. The higher output level of the pressure sensing dieused offsets the lower operating voltage, thus maintaining comparable signal-to-noiseratios to those found in previous generation devices.
Power/VoltageSupply Requirements and Warm-up Shift - As most portable devices are battery operated, pressure sensor powerand voltage supply requirements have traditionally been 5V, though the generaltrend has been a move toward 3.3V or lower voltages, to help further preserveproduct battery life. These lower power requirements facilitate easier customerintegration of sensors into finished product designs, with increasedmeasurement stability and performance. This is because the risk of internalself-heating and related offset shifts are reduced.
When consideringtemperature requirements, warm-up shift is also a concern. The warm-up shift of a device is the effect that power has on devicephysical characteristics in its warm-up phase. An alternate and preferred approach toreducing supply voltage modulates the sensor supply as required by the systembandwidth. In other words, apply power to the sensor only when needed. Thisreduces power to the sensor to the time average (duty-cycle) apA-plied and, therefore,reduces warm-up drift.
To help manage powerrequirements, pressure sensors are offered in both compensated anduncompensated versions. Compensated devices offer lower calibration costs,faster production cycles, lower production equipment overhead and easierdesign-in capabilities. Uncompensated versions are generally designed tooperate at 5V.
Low-voltage pressure sensorsoffer 1.8 and 3.3V power supply requirements, to facilitate sensor integrationinto portable device and equipment designs.
Low-Power Sensing Applications
With the designparameter issues listed above in mind, the following examples help illustratethe successful incorporation of low-voltage MEMS pressure sensors:
HVAC pressure transmitter forbuilding monitoring. A portableindustrial airflow measurement device is used for on-demand measurements of lowairflow beneath HVAC vents within typical office environments or apartmentbuilding setups. Typically, this application requires use of a basic pressuresensor with unconditioned, uncompensated millivolt output signal, and providesa raw output signal for the OEM device. Within the intended pressure sensorusage environment, the selected component must offer long-term reliability andstability, as well as relatively good accuracy and low environmental mediasensitivity. The device application environment itself is typicallycharacterized by modest temperature variations and humidity. In these types of applications,the requirement for low warm-up shift is also important, as the device needs tooperate with stability soon after powered on. Position sensitivity is lessimportant, as the device itself is specifically orientated under duct work. Thesignal-to-noise ratio (or noise floor) of these sensors must be very low, asvery small air pressures are being measured. Low power consumption, due tobattery or current loop operation, is also a significant consideration.
Medical breathing apparatus. An example of an applicationrequiring a higher degree of accuracy and performance can be found in medicalbreathing apparatus used within critical patient care applications. Devicedesigns must be highly rugged, as well as offer high accuracy and reliabilitywithin demanding environments. As medical breathing devices are employed withinhospital, urgent care and other clinical settings, they can be subjected to ongoinghigh levels of shock, vibration and g-force pressures, as well as wide output ranges.The demands placed upon devices within their intended usage environment would require OEMs to specify a millivolt output or amplified pressure sensor,fully calibrated and temperature compensated. Low position and shocksensitivity are also requirements.
Also required for this type ofdevice is the integral amplification of the pressure sensor. The amplifiedpressure sensor component typically houses an onboard ASIC (built-in amplifierwith compensation), allowing control of the millivolt output sensor gain, noiseand compensation. Amplified devices are scaled to fall into the input range ofa common analog-to-digital microprocessor without additional gain. Theamplified pressure sensor can be thought of as an accurate, compensated devicewith an amplified output signal that is more plug-and-play for the OEM. This istypically required when the customer's analog-to-digital converter does not havea built-in gain feature.
This type of application typicallyuses a compensated millivolt pressure sensor. Compensated millivolt low-voltagepressure sensors are calibrated to both zero and span and are temperaturecompensated, to ensure accurate output signal over a specified operating temperaturerange. A compensated device is typically used in an application were accuracyis a priority and the OEM relies on the pressure sensor manufacturer to provideall temperature compensation and calibration within the pressure sensor itself.In this case, a manufacturer typically requires a clean, low-noise outputsignal. The OEM would typically provide an amplifier or ASIC somewhere on theirPCB to increase the mV output signal.
Tim Shotter is director of new productsand Dan DeFalco is marketing manager at AllSensors Corp.
About the Author(s)
You May Also Like