Magnesium Sheet Technology Eyes Niches
July 30, 2010
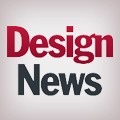
A new lightweight, high-strength magnesium sheet technology targetsapplications in military vehicle armor, resorbable biomedical implants andstructural aerospace applications.
The new sheet is said to provide 200 percent higher strengthand improved toughness compared to conventional magnesium, while also providingthe strength of carbon steel sheet at one-fourth the weight.
Magnesium Sheet Technology Eyes Niches_A |
The new sheet technology has been developed by a company callednanoMAG, a subsidiary of Thixomat, AnnArbor, MI. The approach is related to the thixomolding injection moldingprocess which converts magnesium alloys into complex parts.
"This is a significant advancement in magnesium that bringsunprecedented performance in terms of strength and light weight, meeting thechallenging demands of the automotive, military, biomedical and aerospacemarkets," says Stephen LeBeau, president of nanoMAG. The company received a two-year $730,000 contractfrom the U.S. Dept. of Defense to develop lightweight composite militaryvehicle armor using nanoMAG sheet as the base structural carrier for vehicleplatforms.
The patent-pending process features isotropic fine-grainedstrengthening that permits low-volume manufacturing for specialty applicationsat a competitive cost.
According to nanoMAG, magnesium alloysheet traditionally has been cost prohibitive, difficult to form and limited inavailability.
Developed with the University of Michigan, the ThixomoldingThermal Mechanical Process (TTMP) produces ultra-fine-grain "nanocrystalline"magnesium sheet with properties superior to conventional metals. The nanostructure is produced in-situ in a bulk form, avoiding the manufacturing issuesassociated with the handling of fine powders.
The process uses thixomolding toproduce a sheet bar which is put through secondary thermomechanical heatprocessing. A key factor is the precise control of the microstructure whichincreases the yield strength of the original stock by more than 200 percent tomore than 250 MPa along with 10 percent elongation. The result is an advancedmagnesium sheet/plate with a superior strength-to-weight ratio than competitivematerials.
Magnesium Sheet Technology Eyes Niches_B |
nanoMAG describes its manufacturing plant as a "mini-mill,"a term that usually refers to production of steel shapes through remelting ofscrap.
The operation consists of discrete manufacturing cellscapable of producing 500 tons per year with a relatively small initial capitalinvestment compared to construction of a greenfield metals plant that performscasting and rolling.
nanoMAG says the fine-grain sheet material also forms easily,allowing fabrication of net-shape finished components currently not available.
nanoMAG estimates that the global market for magnesium sheetis 1,250 tons a year, with revenues totaling $50 million. The global market formedical implants is estimated to exceed $4 billion with roughly 50 percent tiedto ligament repairs that could benefit from improved fastening systems usingmagnesium resorbable implants. This approach to temporary metallic implants isone of the latest developments in biomaterials. Scientists have reported thatside effects of special degradation products are unlikely since magnesium is animportant micronutrient, and its role in biological systems has beeninvestigated extensively.
For structural applications, laminated composites ofmagnesium sheet with carbon fiber have been successfully fabricated.
New aircraft designs will make greater use of lightweightmaterials, such as carbon composites, titanium, aluminum-lithium alloys andmagnesium.
nanoMAG and the University of Michigan received a NationalScience Foundation (NSF) grant to demonstrate the commercial feasibility of thematerial. Another NSF grant for $500,000 has been awarded for scale-up work. nanoMAGhas a pilot/pre-production plant in operation in Ann Arbor, MI. The company isactively seeking development partners to test and validate early pre-productionsamples tailored to end-use markets.
About the Author(s)
You May Also Like