In This Case, Both Engineers Were Right
March 19, 2011
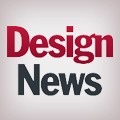
By Jerry Muehlbauer
Here’s a true story from some motor testing I conducted several years ago. Danfoss (my customer) had just developed a new closed loop vector drive and they sent their development engineer and the drive to the Regal Beloit lab to fine-tune the drive’s torque control algorithm. We connected the Danfoss drive to my 250 HP AC induction motor, wired up the encoder (which provides speed and rotor position feedback) and completed the autotune process.
Autotuning empirically identifies the motor’s parameters and greatly improves the ability of the drive to control the motor. We then coupled the motor to the dynamometer, which consisted of an inline torque transducer, a load motor, and a line-regenerative vector drive. Testing went fine until the Danfoss engineer decided to accelerate and decelerate the motor at 150 percent torque to check response of the torque regulator in the new drive.
He programmed a “sawtooth” profile, commanding the motor to accelerate to 60 Hz in five seconds, then immediately decelerate to zero RPM in five seconds, reaccelerate in five seconds, decelerate, and repeat the cycle for five minutes. While observing the torque readout on the drive’s display panel he stated, “See, we’re producing 1100 lbft of torque and it is linear throughout the speed range.”
I glanced at the metering on my dynamometer and replied “It’s linear’ but only 1006 lbft, not 1100.” Alarmed, he double checked his settings and asserted, “No, it’s 1100 lbft. The autotune modeled your motor accurately and my numbers are correct.”
I countered, reminding him that I was reading the torque from a transducer that had just been calibrated and was certified to be accurate. This bantering continued until the answer suddenly struck me and I realized that we were both correct. How could this be?
Answer: The test motor was in fact producing 1100 lbft of torque and the Danfoss drive model was accurate. Because of the sawtooth accel-decel pattern, 94 lbft of torque was being expended to drive the motor’s 81 lbft squared rotor to 1790 RPM and back to zero. Only 1006 lbft appeared at the motor shaft to be read by the dynamometer. When we accounted for the torque lost due to the rotor inertia it was clear that the drive’s torque regulator was accurate. If the test cycle had included a 5 second (or longer) period at 1790 RPM the “inertia torque” would have disappeared and the dynamometer would have read 1100 lbft during the steady state intervals.
Jerry Muehlbauer is a senior application engineer with Regal Beloit’s large motor group, located in Wausau, Wisconsin. He has 25+ years motor and VFD experience, having worked in the drives and motor groups at Rockwell, GE, Marathon Electric, and Regal Beloit.
About the Author(s)
You May Also Like