Chest Irritation and Overheating Lead to Cooling Fan Innovation
September 8, 2010
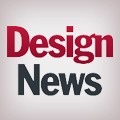
Ruffled blouses and heavy lint accumulation lead to new
forklift fan design with multiple application possibilities.
By Myron J. Boyajian, Contributing Editor
In its day, a manufacturer had a lucrative business leasing its forklifts to the cotton compress industries. The scope of this business, both geographically and commercially, was so large that it required a major co-coordinated, corporate effort to install and maintain a national fleet of forklifts. These trucks were equipped with heavy-duty hydraulics and transmission heat exchangers, selected mast heights and tilt angles, and cotton bale-handling forks.
This application was marked by short, rapid and choppy duty cycles where forklifts quickly shuttled from bulk cotton storage to the baling machines, and then to loading the compressed bales for transport. These actions formed what the industry described as a high-cycle operation. In most locations, these forklifts were standouts in reliability, performance and customer acceptance. However, as time progressed and more of these special trucks went into more locations with more severe weather extremes, engine and transmission overheating became the rule rather than the exception.
Working within the manufacturer’s development engineering group, I was assigned to oversee prototyping and testing of various solutions to the overheating problems. As designers, we try to design equipment that anticipates technical needs, but unforeseen circumstances can affect our goals. A good example of this occurred when we were working on the overheating fan issue. The ladies working on an assembly line at one of the plants where the forklifts were in operation complained that their chests were becoming irritated. Our investigation showed that, as each forklift went down an aisle, the strong air stream exiting the radiator opening ruffled the ladies’ blouses, causing the irritation. Our solution was to change the cooling fans to draw air into the radiator. Since this plant had quite good housekeeping with clean floors, there was minimal dirt and dust blown about, so using a “sucker” rather than a “pusher” fan solved the problem.
The forklifts used in the cotton compress industry, however, presented more complex challenges. Observation showed that cotton lint was accumulating on the radiator and cooler cores, and limiting airflow. A succession of design changes to fan blade pitch angle, blade count and blade shapes were made, all yielding little or no improvement. We also tried different radiator and heat exchanger specs, using wide fin spacing and lower tube counts that would allow cotton lint to blow through, all with no real change. The best solution was a simple screen that trapped lint, but the screen required changing or cleaning several times per shift. Finally, in a burst of inspiration I suggested a simple mesh screen that, in effect, rolled around the radiator. Lint trapped on one side was transported by the moving screen to the opposite side of the radiator where it was blown off the screen by the cooling fan air stream. The experimental department lads built up a prototype that worked just fine, so problem solved?
Well, not so fast. The drive mechanism proved difficult to package and the added complexity was, well, too complex. The solution that seemed to be the simplest and best was to relocate the heat exchangers above the forklift counterweight with an electric cooling fan, well above the stratum of air carrying the lint particles. Now, we could say problem solved!
This particular bit of innovation led to patent number 3,344,854, but also inspired a solution to a similar problem in a threshing machine application demonstrating the wide applicability of solid design ideas.
About the Author(s)
You May Also Like