Hydraulic Controls Make Helicopter Parts Pass the Test
November 16, 2009
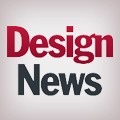
One of the fastest-growing uses for closed-loop hydraulic controls is in the area of production testing, where ensuring that products meet specifications for strength or number of operating cycles is required. Applications range from medical devices to tube and pipe manufacturing, to automotive and aerospace.
In the latter category, hydraulic test stands have been used since the 1950s to place real-world stresses on aerospace components as part of the steps required to certify their designs for deployment in production vehicles. Recently, hydraulic testers are getting "smarter" through the use of programmable electronic motion controllers. Consider the testing of helicopter rotor blades at Helicopter Technology Co. (HTC).
HTC uses an apparatus (see figure above) that exerts force on blades using hydraulic cylinders oriented in different axes. One pulls on the blade simulating centrifugal loads. One tries to flap the blade, and a third one torques, or twists the blade. The loads that are applied by the cylinders, which can sometimes be as much as 25,000 lb, are the same as those measured in actual flight tests, ensuring the lab tests simulate the exact forces encountered in flight.
Laboratory systems used decades ago to test helicopter blades would simply drive each axis' hydraulic solenoid valve with a sinusoidal signal, causing the hydraulic jack to extend and retract, varying the force on the blade. This method required the system to be continually re-tuned to ensure the proper force was being applied consistently throughout the testing period.
About two years ago, Gary Burdorf, HTC's chief engineer, looked for a motion control solution that would perform closed-loop control of the force exerted by each hydraulic axis directly. He contacted Peter Nachtwey, president of Delta Computer Systems Inc. of Battle Ground, WA, who suggested Burdorf use an RMC motion controller for his project. Because the Delta controller is capable of closed-loop control using pressure/force feedback, HTC was able to get higher bandwidth than it could have using just displacement measuring. "Delta's off-the-shelf motion controllers made it possible for us to bring rotor blade testing into the 21st century," says HTC's Burdorf.
About the Author(s)
You May Also Like