Fastening productivity kit
April 5, 1999
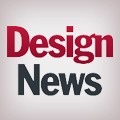
Need more joining force? Use fasteners and adhesives
By Christine M. Ferrara, New Products Editor
Eastleigh, England--Engineers routinely stress-test new joining methods, but no lab could duplicate 50,000 lbs of thrust. That's what the Thrust supersonic car dished out as it broke the world land speed record at 763 mph in late 1997.
In the car's production, the Thrust team focused on its technical parameters rather than production ones since the Thrust team built it like a "very expensive prototype," according to Paul Sennett, marketing manager for Permabond, which supplied the adhesives used on the car.
The Thrust team looked at a number of ways to join the car's many pieces, made from materials including titanium, carbon- and glass-fiber composites, aluminum, and steel. Mechanical fasteners alone would not do. For example, in the case of the titanium panel on the car's jet engine, rivets alone would ping straight out under high speeds, Sennett says.
With all the media attention surrounding the car's development (see DN 4/6/98, p. 114; DN 5/18/98, p. 38), one fact went unreported. To hold together car panels subjected to such speeds, engineers needed a combination of mechanical and material fasteners. On the mechanical side, the Thrust team chose Monobolt Concept blind fasteners from Textron Aerospace Fasteners (Garden City, England) for use on the car's canopy and structural areas, says Mike Legg, Textron's sales and product manager.
Indeed, even though the trend is toward using less mechanical fasteners in a given design, increased mechanical fastener use in harsh environments is an industry-wide phenomenon. "Their quality is continually improved, so they are used in more critical applications," says Dick Akers, staff engineer at the Industrial Fasteners Inst. (Cleveland, OH).
As evidence of this, Akers points to declining nonconforming parts per million counts. "They used to be in the tens of thousands per million, but now they are usually less than 100 per million," he says.
The mechanical integral break-off lock fasteners used in the Thrust car were originally for aerospace applications, Legg says, and did not require modification for use in the supersonic car. The fasteners meet German, French, American, and British national standards.
Mechanical fastener benefits include light weight, high strength, and good fatigue resistance. "Our aerospace fastener customers consistently comment on what good fasteners these are," Legg adds.
On the adhesive side, the Thrust team selected three Permabond adhesive products and a pretreatment for use in various parts of the car. A Self Indicating Pretreatment (SIP) prepared panel surfaces prior to bonding, while A130 threadlock locked nuts and screws were used in places where panels may need to be removed.
Thrust engineers used ESP110 single-part, heat-cure epoxy where heat was high around the jet engine exhausts. The adhesive provides exceptionally high-strength heat resistance, Sennett says. The E32 two-part epoxy bonded the panel work onto the Thrust supersonic car's main welded box beam core. Engineers used E32 in all areas of the car except where temperature resistance was required.
The ESP110 and E32 adhesives for the supersonic car are off-the shelf products. "They did not add weight, and the mechanically fastened panels, working together with adhesives, distributed load over area," Sennett says.
Other applications for the two adhesives are diverse. E32's include the automotive industry's structural end, such as use in filters and electric motors. ESP110 can be used in applications where strong heat resistance is required, Sennett says.
The adhesives' main advantages are threefold. The material fasteners reduce costs, save time through their ease of use, and give products a better appearance. "Rivets hanging out are not always attractive," Sennett says.
"You can't get much more of a test than use in a supersonic car," Sennett adds. "People tend to be very vocal when things fall apart, and E32 and ESP110 have a great history in extreme applications."
Overall, two fastening methods were better than one in this instance. "Neither could have been done independently," Sennett says. "The two work very well together."
Adhesive dispenser reduces assembly time
By Anna Allen, Staff Editor
Elgin, IL--Problem: Circuit-board company needs to improve productivity for producing rigid-flex circuits.
Solution: Use an automatic adhesive dispenser to cut assembly time and increase productivity.
Flex Four Inc. specializes in fast-turnaround prototyping and medium production runs of high-tech circuit boards. As demand for its rigid-flex circuits increased, it became necessary to streamline an adhesive application process that was producing 10 parts/hour.
In a key assembly process, workers apply a precise bead or fillet of a pliable, non-conductive epoxy along the joint where the rigid board and flexible circuit meet. By moving the bending stress away from the sharp edge of the board, the thin bead of adhesive prevents the fine copper traces from cracking.
Controlled adhesive application is key, says Flex Four President Dennis Jones. "The width of the bead determines where the bend will occur--a critical consideration in products where the circuit will be subjected to repeated stress, such as notebook computers and cellular phones," he says.
Previously, the operator carefully masked each part with tape, then spread the epoxy with a toothpick. Although this method worked in prototyping, it was too slow for production runs, says Flex Four Senior Process Engineer Scott Powell. "If a customer needed a few hundred boards in three weeks we had to allow a week for the bonding process."
The company turned to EFD Inc. (East Providence, RI) for a faster application method that was less elaborate than using an X-Y table. EFD arranged an on-site demonstration of its automatic dispensing equipment. During the demo, EFD's product specialist showed Powell and fellow engineer Duane Ziege how to operate the benchtop unit.
An operator loads the material into a disposable barrel, connected to the dispenser by lightweight, flexible tubing. The operator then attaches a precision tip to the barrel, and adjusts the air regulator for the desired flow rate. Then the operator presses the electric foot pedal to make a neat, controlled bead.
"We were amazed by its potential," Powell recalls. "Instead of spending five or 10 minutes on each part, we could touch the foot pedal and be done in a few seconds." Productivity has increased twelvefold--from 10 parts an hour to 10 parts in less than five minutes, he adds.
Curing time is also shorter and the new method has increased reliability. "Knowing you can put the same bead on every single board makes engineering much easier," says Powell. "If a customer specifies a maximum fillet width of 0.080 inch, we know the exact tip gauge and air pressure to use to meet that requirement."
Moving to automatic dispensing has also provided an unexpected benefit--dramatically reducing consumption of the $600/1/2-gal epoxy. In the past, operators were lucky to get 100 parts from a 12-gm batch of epoxy. Today, Flex Four engineers produce more than 300 parts with the same amount, achieving a 70% reduction in adhesive costs.
Fastener facts
62% of engineers specify or approve mechanical fasteners, while 42% specify or approve adhesive or chemical ones.
The primary design objective cited for engineers is ease of manufacture, according to 87% of survey respondents.
Source: Design News
1997 Simmons study
APPLICATION TIP
Here's one way to save adhesive
By Christine M. Ferrara, New Products Editor
Torrington, CT --Sometimes less means more. That's the case with a UV/visible-light curing process from Dymax Corp.
A supplier to major U.S. vehicle manufacturers in the headlamp industry previously used a two-part silicone adhesive to bond a lens to a fog-lamp reflector used on several SUVs and light pickup trucks. This method required the parts to sit for 24 hours to cure completely before they were tested for quality control.
The silicone adhesive provided a bond line width of 3/16th of an inch. Switching to Dymax's UV/visible-light cure process cut the bond width by one third because of the adhesive's strength. This reduction let the manufacturer redesign the fog lamp with a smaller groove and a larger reflector, resulting in a brighter light, according to John Arnold, principal investigator of Commercial Development for Dymax.
The previous headlamp assembly method involved mixing adhesives such as urethane, silicone, or epoxy with expensive, two-part mixing systems. The adhesives' 24-hour cure time required the manufacturer to clamp the headlights to keep them in place while curing. Besides adding cost, using clamps also required the manufacturer to sacrifice production space for storing in-process uncured head lamps, says Arnold.
In contrast, the manufacturer can dispense UV/visible light-curing adhesives with an inexpensive dispenser, clamp parts together with a reusable clamp, and put the part into a 5-ft-long Dymax UV conveyor. Cure rate is approximately 2 ft/min. "When you take the headlamp out the other end of the conveyor, it's done," says Arnold.
The UV/visible light-curing technology also saves space and money, according to Dymax. "You can put about 10 UV-curing lines in the space needed to make one chemical-cure line," Arnold adds. "There are a lot of saving ways that come with the UV process. It changes your entire assembly process."
UV and visible light-curing adhesives use the same chemical reactions with a photoinitiator, a non-light stable chemical which starts the reaction. "It's a catalyst," Arnold says. "When light hits it, it falls apart. When it falls apart it starts the chemical polymerization." What differentiates the two, however, is whether the photoinitiator responds to UV or visible light, or both.
The UV/visible light-curing process' uniqueness stems from the fact that the user cures through the lamp's UV-blocked plastic lens, which blocks 100% of the UV light. This means that only the visible light cures the UV/visible light adhesives.
Did you know...
Epoxies are the most popular adhesive specified by engineers (73%), followed by silicones (52%), and pressure-sensitive adhesives (45%).
Almost all engineers specify threaded mechanical fasteners (97%); next in line are pins (56%), and rivets tied with inserts (51%).
Strength and durability are the most important characteristics in engineers' fastener specifying decisions (89%), followed by ease of installation (74%) and corrosion or chemical resistance (51%).
Engineers work with aluminum the most (83%), followed by steel tied with stainless steel (78%), and plastics (69%).
Application areas in which engineers use fastening products or engineering hardware include: machine tools (26%), industrial/consumer electronics (25%), aerospace (23%), and defense (20%).
Source: Design News Market Beat Survey
Fastening users talk trends
By Anna Allen, Staff Editor
According to the 1997 Simmons study and conversations with Design News readers who use fasteners, application drives design. Yet the push to cut costs, maintain ease of use and assembly, and minimize part count is also a critical fastening considerations.
When it comes to selecting a supplier, users agree that part quality, availability, and cost are key factors. Roger Wheatley, manufacturing/engineering team leader for Fujitsu Ten sums it up best: "A good supplier is someone who shows an interest in what you're looking for, gives the best information, and delivers the product as promptly and efficiently as possible."
Dave Polakowski, materials engineer for Hewlett-Packard, uses fasteners in product assembly and sub-assembly applications such as scanners. The company primarily turns to mechanical fasteners and rarely uses epoxies or adhesives, he says.
Polakowski believes the use of adhesives is increasing across industries. However, he notes, "While this transition is associated with cost and ease of assembly, it's more of an application-driven issue."
Terry Miller, staff engineer at Lockheed Martin agrees. "I think we're moving more and more toward one-unit replacements, so there should be less use of mechanical fasteners."
ASK THE EXPERT
How bolt strength affects tapped-hole thread stripping
Every engineer has questions about components. Design News' Board of Expert Advisors are available to answer them in the Channels section of the magazine's home page, www.designnews.com.
Recently, a reader asked how to determine the length of thread engagements between a grade 8 fastener (tensile strength 150,000 psi) and a tapped hole in G3000 cast iron (tensile strength 30,000 psi). This reader also inquired about the effects of material tensile strength and elasticity on thread engagements. Or more specifically, how does bolt material strength and tapped hole material strength affect thread stripping strength.
Bill Eccles of Bolt Science Ltd. is the expert who answered the question.
Here's his answer:
Answer--Nut thickness standards have been drawn up on the basis that the bolt will always sustain tensile fracture before the nut will strip. If the bolt breaks on tightening, it is obvious that a replacement is required.
Thread stripping tends to be gradual in nature. If it does occur, partially failed assemblies may enter into service. To achieve a reliable design, the potential of thread stripping both internal and external threads must be avoided if a reliable design is to be achieved. Therefore, when specifying nuts and bolts, the appropriate nut grade must be matched to the bolt grade.
In cases when a threaded fastener is tapped into a plate or a block, the fastener and block materials are usually different strengths. If the bolt must sustain tensile fracture before the female thread strips, the required thread-engagement length can be excessive and become unrealistic for low-strength plate/block materials. Tolerances and pitch errors between the threads can make the engagement of long threads problematic.
Long thread engagements can be overcome by adopting one of a number of strategies:
Do not meet the tensile fracture criteria for the bolt; that is, allow for thread shear to occur below the bolt's tensile fracture load.
Increase the shear area of the female thread.
Use a lower tensile strength bolt.
In the particular application that you mention, the fastener is five times stronger than the tapped material. Do you need to use such a high-tensile fastener? Do the loads acting on the joint necessitate a fastener of such a strength grade? I would anticipate that with such a long thread engagement, assembly problems may occur.
Also, is the cast iron's ductility sufficient to allow plastic deformation in the threads to occur and all the threads to come into bearing before the first threads start to strip?
Thread-stripping formulas assume that the material has sufficient plastic deformation prior to failure to allow all the threads to come into full bearing. This point partially answers your next question regarding the first few threads taking the loading. Yes, the threads do take the majority of the loading if you assume that plastic deformation does not occur. However, plastic deformation does occur in the threads when the fastener is tightened.
The thread profile represents a high-stress concentration. Yield in the thread root occurs but not fracture. If fracture occurred when the root of the thread reached yield-only, a fraction of the actual clamp load would be achievable. Thus, it is important to make threaded fasteners from materials with appropriate stress-strain properties. And, because of the nature of how a clamped joint sustains an external load (see the tutorial on the Bolt Science website: www.boltscience.com ), only a small proportion of any applied load is sustained by the bolt. This makes fatigue failure less likely than one would normally suspect when yield in a part has occurred.
In the case of thread stripping, yield in the threads nearest the surface occurs to allow other threads to be brought into full load bearing. For this to be successful, there must be sufficient ductility in the material. With relatively weak non-ductile materials and high-strength fasteners, there will be an engagement length when the threads nearest the outer surface will shear before all the thread length reaches its full shear strength.
Thread stripping analysis is also complicated by other effects that can be taken into account (again, see web site for further details). For example:
The effect that variation in the thread dimensions has on fastener failure mode of internal and external threads.
Tensile and shear strength variations in the material for internal and external threads.
The effect of radial displacement of the nut/tapped part in reducing the thread's shear strength.
Such factors can make the analysis somewhat convoluted, but computer programs can assist in the process.
Bill Eccles is a professional engineer with more than 20 years of experience in solving problems that are related to the design, assembly, and maintenance of bolted joints. He holds degrees in mathematics, computing, and engineering. Eccles founded Bolt Science Ltd. in 1992, a company that specializes in solving problems related to bolted joints.
Products to watch
Fastener
Auto-Bulb(R) fastener offers a large-diameter head and broad bulb spread that diffuse the load over a large space, ensuring a lasting clamp. The Auto-Bulb also features a tapered, hole-seeking tip, which provides for quick installation. Available in a range of sizes and grips, the Auto-Bulb can be used for both repair and production applications.
HUCK Int'l, c/o TRIAD Business Marketing, 2909 Cole Ave., Suite 100, Dallas, TX 75204.
Sealant
The 733 paste-like glass and metal sealant bonds glass and metal substrates in applications such as appliances, heavy machinery, marine equipment, and transportation. The non-slumping RTV material provides unprimed adhesion to cleaned substrates such as glass, non-oily woods, ceramics, natural and synthetic fibers, painted surfaces, and plastics.
Dow Corning Corp, Midland, MI 48686.
Pin sorting system
Pin sorting system sorts non-headed pins in high-volume applications, separating out debris, damaged pins, and pins with incorrect diameters. Pins are fed from a Series 2000 high-performance vibratory feed system through gauging bushings. The bushings trap bent and oversized pins and automatically discharge them, along with undersized pins and other debris into a scrap bin.
Spirol Int'l Corp., 30 Rock Ave., Danielson, CT 06239; FAX (860) 774-0487.
Hot melts
PUR-FECT LOK(R) reactive hot melts allow immediate processing of your part in the next step of assembly. Heat resistance and strength are available in hours due to the ACCELERATION TECHNOLOGYTM curing system. The hot melts provide solvent-free bonding with no VOCs.
National Starch and Chemical Co., Box 6500, Bridgewater, NJ 08807.
Thumb nut
Molded nylon thumb nut "A" is molded in tough, electrically insulating nylon 6/6. The nut is available in nine thread sizes: 440, 632, 832, 1024, 1032, 1/4-20, 5/16-18, 3/8-16, and 1/2-13.
Micro Plastics Inc., Hwy. 178 N., Flippin, AR 72634; FAX (870) 453-8676.
Epoxy compound
EP101HTAO two-component epoxy compound is for potting, casting, encapsulation, and sealing in up to 500F service. The epoxy resin compound comprises a heat-resistant liquid epoxy resin and a curing agent that features thermal stability and presents minimal toxicological hazards during handling. The mixed system exhibits a long working life at ambient temperatures.
Master Bond Inc., 154 Hobart St., Hackensack, NJ 07601; FAX (201) 343-2132.
Bolt connectors
End-to-end variable-angle bolt connectors connect the end of profiles with 8- or 10-mm t-slots at various angles. The end-to-side connector fastens to various profile angles and allows for quick assembly and disassembly. The end-to-side connector can be bent to any angle from 45 to 135 degrees ; the end-to-end connector can be bent from 90 to 180 degrees .
Bosch Automation Technology, 816 E. Third St., Buchanan, MI 49107.
Fastener drive system
Mek-Lock(R) fastener drive system is available in both bolt and nut configurations. Both feature a head configuration that enables a Mek-Lock wrench to clamp precisely onto the bolt or nut for positive and secure installation, even in difficult-to-reach, automated, or critical environments.
Mek-Lock Fasteners, 2965 E. Hillcrest Dr. #304, Thousand Oaks, CA 91362; FAX (805) 495-2747.
Dispense gun
The DotMakerTM dispense gun uses positive displacement technology to eliminate operator guesswork, and provides better control than manual applicators. Typical uses include assembly, touch-up, and repair. The lightweight, portable DotMaker is also suited for maintenance, field work, and other applications where accuracy and mobility are important.
EFD Inc., 977 Waterman Ave., East Providence, RI 02914; FAX (401) 431-0237.
In Print
Product selection guide
ZOOMTM CD-ROM features more than 13,000 Southco products, including latches, captive fasteners, hinges, handles and pulls, and drive rivets. To find a product, the user goes through a quick selection process, entering design criteria, such as panel thickness, access restriction requirements, desired finish, thread size, and material. ZOOM takes the user to appropriate products. The CD-ROM features product descriptions, a glossary of terms, animated vignettes of how to install selected products, and a quick tour demo. ZOOM operates with Windows 95, 98, and NT.
Southco, 210 Brinton Lake Rd., Concordville, PA 19331.
Aerospace fasteners find a place in auto racing
By Anna Allen, Staff Editor
San Clemente, CA--More than 30 years ago, a Gurney Eagle-Offenhauser engine blew up on the starting line of the Ontario Motor Speedway in California. At first inspection, the failure appeared to be the connecting rod, manufactured by Carillo Industries. A closer look revealed the true cause: The fasteners that clamp the rod to the crankshaft had disintegrated under the strain of transferring all the engine's power to the crankshaft and the wheels.
"The biggest concern in the connecting rod business is the fastener," says Jack Sparks, president of Carillo Industries, which manufactures high-quality rods. "Typically, the fasteners are the weakest parts."
In an effort to solve this problem and improve the bolt's strength, company founder Fred Carillo turned to his aerospace industry connections who introduced him to SPS Technologies (Jenkintown, PA), a high-strength-fastener manufacturer. Material selection was a key factor in addressing the corrosion.
"We were a small company at the time," says Sparks, "Our application could hardly justify proprietary bolts. We went to SPS product engineers and said, 'We have a problem, can you fix it?' They assured us that Multiphase alloys would meet our requirements."
The companies decided on MP35N(R) and MP159(R) superWORD NEEDED? alloys, a combination of nickel, cobalt, chromium, and molybdenum tested to 260,000-psi tensile strength. "In addition to material selection, SPS also suggested some changes in the bolt's design," says Sparks. "We incorporated an asymmetric thread design, developed by SPS, to help achieve greater fastener reliability and increase life cycle. This gives us a more comfortable safety margin."
The SPS bolts are pre-loaded to 12,000 to 13,000 lb, based on a 7/16-inch reduced-shank bolt. "The bolt will function and run at yield, but we build in a lot of forgiveness," Sparks says. Now, there are four areas on the Carillo rods with less strength than the bolts.
To verify the strength requirement, SPS and Carrillo Industries developed bolt fatigue parameters for each connecting rod bolt made of the Multiphase(R) alloys. They have modified test criteria several times to keep up with technology advances in connecting rod designs.
Today, SPS remains a primary supplier for Carrillo, which now builds connecting rods for teams competing in the Winston Cup, Trans Am, and Pep Boys IRL races. Carrillo also supplies connecting rods for one of the Big Three automobile manufacturers for use in the development of a small-displacement V6 engine entering production in 2002. Another customer, Lawrence Livermore Sandia Labs, ordered several sets of two-cylinder rods for a test engine it is using to photograph the flame propagation in a diesel engine.
Fastening and adhesive suppliers
Company/web site | Products | Applications | Company contact |
|
|
|
|
|
|
|
|
|
|
|
|
|
|
|
|
|
|
|
|
|
|
|
|
|
|
|
|
|
|
|
|
|
|
|
|
|
|
|
|
|
|
|
|
|
|
|
|
|
|
|
|
|
|
|
|
|
|
|
|
|
|
|
|
|
|
|
|
About the Author(s)
You May Also Like