Electronics Help Cut Costs of Hydraulic Hybrid Trucks
Engineers aim to take hydraulic hybrid powertrains beyond niche status in medium- and heavy-duty trucks and buses.
July 5, 2017
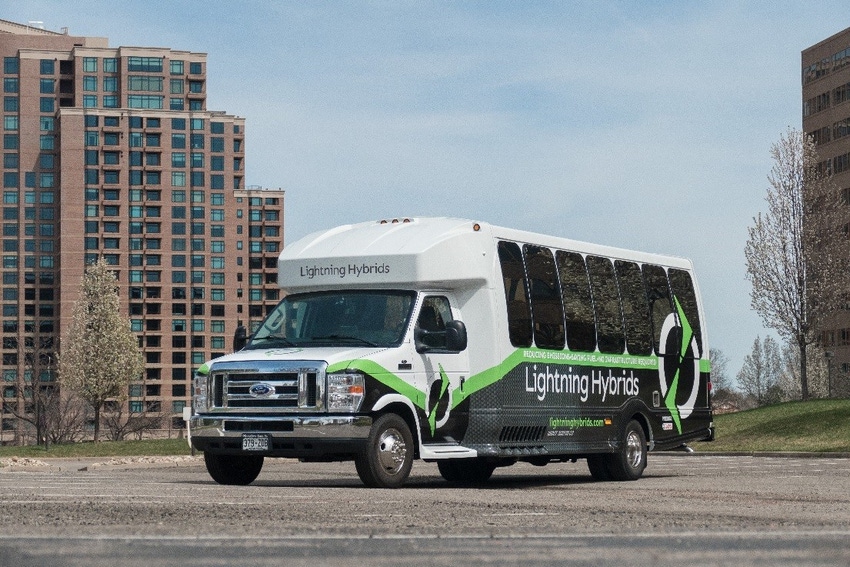
By driving down costs and raising efficiencies, a startup company wants to take the hydraulic hybrid powertrain from the level of technical curiosity to major player in the world of medium- and heavy-duty trucks.
Engineers at Lightning Systems say they have endowed the venerable hydraulic hybrid with greater levels of electronic intelligence, thereby cutting fuel consumption in trucks by 20% and reducing nitrogen oxide emissions by 50%, without a big cost penalty. “We designed it differently from the ground up,” Tim Reeser, CEO of Lightning Systems told Design News. “It’s efficient and cost effective.”
Lightning Systems wants to make hydraulic hybrid powertrains a viable option for medium- and heavy-duty trucks and buses. (Source: Lightning Systems) |
The combination of cost and efficiency is key, Reeser said. To date, the technology has offered efficiency boosts, but the costs were often too high for large-scale adoption. But Reeser believes that truck fleets and OEMs will express more interest in the technology if it offers lower initial costs in addition to operational benefits. The market, he says, is looking for a scale-up option of about $500 per additional percentage boost in efficiency.
“If you can give a 20% mile-per-gallon improvement, then the customer will be willing to pay about $10,000 extra for it,” he told us.
Lightning Hybrids plans to meet that cost constraint. Like all hydraulic hybrid systems, the company’s technology uses a so-called “gas spring” to send power to the truck’s driveshaft, thereby boosting acceleration efficiency and braking capability. To do that, it employs five main parts: a hydraulic pump/motor; hydraulic manifold; gearbox; and two accumulators. During operation, the system uses braking energy to pressurize fluid in a high-pressure accumulator, which in turn stores that energy by compressing nitrogen gas inside it. When a driver then presses on the accelerator, the stored energy from the nitrogen gas drives the truck’s wheels through the hydraulic motor and gearbox. The result is that acceleration gets a boost, cutting the need for gasoline. Moreover, braking gets a boost, too, because the act of pressurizing the accumulator slows the vehicle.
Lightning Systems’ hydraulic hybrid technology employs five main parts: a hydraulic pump/motor; hydraulic manifold; gearbox; and two accumulators. Using pressurized fluid in an accumulator, it sends power to the driveshaft to aid in acceleration and braking. (Source: Lightning Systems) |
“The key difference is we store all the energy,” noted Jonathan Reynolds, lead systems architect of Lightning Systems. “Conventional braking systems convert it into heat.”
Hydraulic hybrids of the past stored energy in the same way, but did so at a higher cost, because they used a variable displacement hydraulic pump to pressurize the fluid, Reynolds said. But Lightning Hybrids cut off a chunk of that cost by employing a fixed displacement design, instead of the variable displacement. The company describes the fixed displacement design as “three to five times” less costly.
To make that happen, the company’s engineering staff made two significant changes – a unique hydraulic design and an advanced controller -- a CompactRIO System on Module from National Instruments. The CompactRIO system, in conjunction with LabView software, gave designers more I/O, more bandwidth, more memory, and the ability to put it all on a printed circuit board about the size of a credit card.
An advanced controller -- CompactRIO System on Module from National Instruments – added a new dimension to hydraulic hybrid technology and helped cut costs. (Source: National Instruments) |
“It would have been easier to control a variable displacement pump, but it would have been way more expensive and a lot heavier,” Reynolds told us. “Doing it this way, we’re able to control a fixed displacement pump like a variable displacement pump.”
The resulting design was a winner of a National Instruments 2017 Engineering Impact Award in the Transportation and Heavy Equipment category. It’s currently being employed on 50 United Parcel Service box trucks in the Chicago area.
Reeser said the use of advanced electronic control gave the technology numerous benefits over predecessors from the 1990s. “Hydraulic hybrids in the early days were choppy, lumpy and noisy,” he said. “By leveraging the faster I/O and hardware, we’re smooth, quiet, and seamless to the driver.”
Although the company doesn’t expect the technology to make in-roads in autos, it has high hopes for medium- and heavy-duty vehicles. Within five years, company executives want to outfit 10,000 vehicles per year. “We don’t see this as a niche product,” Reeser said. “We’re solving a significant pollution issue and cost reduction issue. We want to scale up and make this an impact product.”
Senior technical editor Chuck Murray has been writing about technology for 33 years. He joined Design News in 1987, and has covered electronics, automation, fluid power, and auto.
About the Author(s)
You May Also Like