Elastomers: More design bounce to the ounce
February 20, 1995
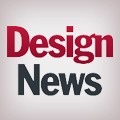
Consumer products, sporting goods, automotive components, wire and cable, industrial equipment, and biomedical devices. These, indeed, represent a diverse range of products. But, in many instances, they have one important element in common-thermoplastic elastomers (TPEs).
The reasoning behind TPEs' choice is not hard to understand. They are a versatile group of resins. Consider, for example, some of their innate property characteristics:
These linear segmented polymers consist of hard and soft ingredients. By varying the relative amounts of the hard and soft components, the resins can meet a wide range of flexibility and performance requirements. This choice alone lets engineers optimize the material to match design criteria when it comes to everything from color or clarity to indoor or outdoor uses.
They are environmentally friendly. Recent resin introductions have expanded this friendliness to include improved recyclability and non-toxin-containing formulations.
Advances in processing technology enable TPEs to be tailored to meet almost any design need, while improving product quality and cost.
Wrap these features in a package and it's little wonder that TPEs have become an increasingly popular entry on the design engineer's material list.
To better illustrate this adaptability, let's look at two industry areas-automotive and medical-where TPEs are making serious inroads as replacements for metals or to complement other plastic materials.
Automotive electronics provide a perfect example of how TPEs can adapt to the changing design needs. The explosion of electronic features in today's automobiles has caused a corresponding increase in the size of electric wiring harnesses. Packaging constraints due to this trend are driving a downsizing of electrical systems. Engineers have accomplished this in two ways: reducing conductor wires, which results in higher operating temperatures, or reducing the thickness of the insulating materials, which requires the need for greater insulating efficiency.
DSM Engineering Plastics has introduced a series of TPEs, Arnitel(R) V, that addresses the needs of both problems. Arnitel UM551-V, a non-halogenated, flame-retardant grade, answers the primary wire insulation obstacle, while Arnitel UM552 fulfills the need for components that require high-temperature resistance, but not flame retardancy.
DSM, the Netherlands-based parent of DSM Engineering, acquired the Arnitel product line from Akzo in 1991. In Europe, Arnitel U has replaced PVC and cross-linked polyethylene based on its environmental, process, recycling, and performance advantages. Relative to other polyester elastomers and typical wiring insulation materials, says Steve Hartig, DSM Engineering Plastics' automotive industry manager, Arnitel can offer:
Continuous-use temperature capability for natural materials up to 338 degrees F (170 degrees C), and for non-halogenated, flame-retardant grades up to 302 degrees F (150 degrees C).
Twice the abrasion resistance.
Excellent UV stability and color fastness.
"We have the expertise of our TPE division here in the U.S., and the experience of thermoplastic manufacturing in Europe," Hartig adds. "This will enable Arnitel UM551-V to find an important niche in automotive under-hood cabling systems."
And when it comes to heat- and oil-resistant materials, particularly for such automotive applications as O-rings, seals, and gaskets, don't overlook a new class of specialty elastomers from DuPont. The Advanta 332 degrees and 365 degrees materials consist of compatible alloys of proprietary polar ethylene copolymers and fluoroelastomers. They are peroxide-curable, whereby the same cure system co-crosslinks both components.
Using the new SAE standard J2236 for determining continuous upper temperature resistance, Advanta 332 degrees qualifies as a 165 degrees C material, and Advanta 355 degrees as a 175 degrees C material, with intermittent excursions to 200 degrees C. "Current lab work promises further improvements in long-term heat resistance," says Eric W. Thomas, senior development specialist at DuPont Elastomers. Processing includes standard compression, transfer, and injection molding techniques. Bonding metal and plastic substrates is possible using commercial primers and bonding agents.
There's also a new family of highly cross-linked, dynamically vulcanized TPE compounds for the automotive market. Introduced by the Plastics Div. of Teknor Apex Co., the Uniprene(R) 7000 TPE olefin-based compounds "have physical characteristics, appearance, and feel similar to vulcanized rubber, but offer superior performance versus competitive products in a wide range of demanding environments," says Thomas Moccia, TPE market development manager.
The materials come in hardness grades of 55 Shore A to 40 Shore D. And, because these products are not hygroscopic, they require no drying. "Additionally, they are readily curable, 100% recyclable, and heat stable up to 232 degrees C," Moccia adds.
Airbag advantage. The increasing popularity of airbags is another automotive area where TPEs' "elastic" properties play a major role. In one case, it helped Chrysler save $12 million a year in the production of driver-side airbags.
For this project, Chrysler worked with Advanced Elastomer Systems (AES) and other team members that included Morton International and Venture Industries. The design involved converting the airbag door from a thermoset to a thermoplastic. The savings resulted primarily from a 40% decrease in the weight of the doors and lower resin costs. However, the simplified design also proved a key factor in the cost savings.
The doors had been made out of reaction-injection-molded, SCRIM-reinforced urethane. They were riveted onto the airbag module. Morton developed a design that uses AES' Santoprene(R) thermoplastic rubber to injection-mold a lighter, easier-to-assemble door that snap-fits to the module.
"Morton reviewed 26 thermoplastic materials before selecting Santoprene as offering the best balance of properties for the application," says Bonnie R. Bennyhoff, AES's account manager for Chrysler. "Specifically, Chrysler was impressed with the "look' and "feel' of the material, and with its ease to process. And we have already delivered test samples that will lead to the next generation of airbag door materials."
And TPEs have one other thing going for them in the automotive world. "This market has a focused priority to address recyclability issues, with elastomeric products one focal point," Bennyhoff explains. "It is expected that the activity in this market segment will carry over into other durable goods markets in setting the pace for dealing with the afterlife and reuse of products."
What's next? "People want to "drive their living room,'" says Mark Wright, director of AES' North American automotive sales. "The focus is on trying to make cars quieter on the inside and outside. In Europe, for example, cars will have to pass a "drive-by' noise limit. Some of this results from engine noise falling down to the ground and vibrating back up."
To counter this, according to Wright, people are adding belly pans or bottom enclosures to quiet the noise. "TPE makes up an important part of that system," Wright explains. "Basically, what you have is flaps that allow opening and closure as the car's velocity picks up. This enables good circulation in the engine compartment as needed, and it also helps to seal off some areas."
The medical arena also affords an opportunity for TPEs to show off their attributes. And they are winning a lot of followers.
The objective here, says Scott Fuson, Dow Corning's manager of medical devices, is for resins producers to help medical-device makers lower user health-care costs. But they also must prove that these materials can stand up under the rigors of chemical attacks, sterilization, and a barrage of lengthy tests required by the FDA.
To help make these tasks easier, Dow Corning introduced a new family of biomedical-grade silicones. The Silastic(R) materials not only meet the Tripartite Guidance standard, but ISO standards. Test results apply to all categories of medical devices that come into contact with tissues, fluids, or blood inside the human body for periods of up to 29 days.
"We wanted to clearly meet the most rigorous standards of testing for our elastomeric materials, even though some of them may be used for external applications," says Fuson. "In the long term, we expect that these criteria will be incorporated into FDA requirements for medical devices." Fuson also notes that new Silastic biomedical grades with improved yield and tear properties will debut shortly.
Polyether thermoplastic urethanes (TPUs) also make good candidates for biomedical products. As a group, these materials resist hydrolysis and fungus attack, as well as the effect of lower temperatures for medical products that require refrigeration.
"The biocompatibility of polyurethane tubing minimizes or eliminates necrotizing dermatitis and reduces platelet damage," says Mike Marasch, senior marketing manager for BF Goodrich's Estane(R) TPU. "Its inherent flexibility resists shrinking, cracking, and kinking-and the tubing can be sterilized. It's also chemical- and solvent-resistant, transparent, and has a high tensile strength. This makes it useful for catheters, connectors, and shunts."
Softness, plus. A "soft touch" also has its advantages in the medical field. With this in mind, GLS Corp. has introduced two Dynaflex(R) medical-grade thermoplastic elastomers: Dynaflex G-2707 and G-27711. With a 32 Shore A hardness, the transparent, high-gloss G-2707 is claimed to be mar resistant, while exhibiting improved puncture and resealing qualities. The G-2711 grade, a translucent resin of 44 Shore A hardness, offers high re-silience, good clarity, and can be resealed.
"Both grades are easily sterilized using gamma radiation, with no significant loss in performance," says John Marshall, GLS market development manager. Typical uses: tubing, EKG pads, mouthpieces, facemasks, hemostat clamp cushions, and syringe plunger tips.
Also, don't overlook thermoplastic vulcanizates (TPVs) when it comes to softness. "TPVs are leading the way over all other thermoplastic elastomers as the "soft touch' material of choice," enthuses Malcolm Thompson, sales and marketing manager for DSM Thermoplastic Elastomers. Thompson considers TPV to be an ideal replacement for EPDM, neoprene, and other mid-performing rubbers, as well as self-skinning urethanes.
Thompson cites DSM's Sarlink 2000 and 3000 TPVs as popular materials for overmolding applications where material compatibility becomes an issue. Overmolded onto polyolefin-based thermoplastics, such as polypropylene, "they achieve excellent thermal bonding, while maintaining recyclability properties and ensuring a soft, rubbery feel," he explains.
Processing breakthroughs. Advances in polyolefins based on new technologies have spurred the production of a new class of elastomeric materials. One of the most recent advances involves the development of homogeneous (single-site) catalyst systems.
One such system, Insite from Dow Chemical, has resulted in elastomeric copolymers of ethylene and octene. Dow sells them under the trade name Engage polyolefin elastomers (POEs). The Dow catalyst process walked off with two major design awards last year: the National Inventors of the Year honor from the Intellectual Property Owners Association, and an "R&D 100'' award from R&D Magazine.
In a paper presented at last fall's technical meeting of the American Chemical Society's Rubber Div., Dow project leader Jeff E. Brann reported that the Engage POEs "have significant advantages versus EPDM/EPM compounds in heat aging, UV stability, mechanical properties, and processing." These enhancements, he adds, make the POEs well suited for such applications as cable insulation, belts, automotive hoses, seals, and other electrical uses.
From an environmentally improved processing perspective, Lord Corp. has developed a method to better bond waterborne elastomers to metal. The single- and two-coat aqueous adhesives for vulcanization bonding "have demonstrated comparable, and often improved performance, compared to existing solvent-borne adhesives," says Lord spokesperson Tony Ciampa. "They provide end users with an excellent alternative to VOC-containing, solvent-borne adhesives."
In a series of tests, the Chemlok aqueous adhesives demonstrated "excellent adhesion to natural rubber, styrene-butadiene, neoprene, nitrile, and butyl rubbers," Ciampa notes. In some cases, they maintained this level of performance after a five minute pre-bake, as well as severe environmental analyses.
"Concerns for the environment; federal, state, and local government regulations; health insurance; and worker safety all serve as impetus to use aqueous adhesives," Ciampa adds. Considerable lab work and production trials have been conducted to help facilitate this transition. Lord recently completed an applications lab that can perform all the operations found in a production plant. Customers can evaluate the adhesive in production conditions that match actual plant operations.
But what really excites those at Lord are the opportunities that will be created by a new line of products based on Lord's controllable fluid technology. These so-called MR fluids are free flowing until they encounter a magnetic field, which converts them to a non-flowing, near-solid consistency. Their application in devices such as exercise equipment will allow the user to "dial in" a desired program of physical intensity. In the automotive arena, seats suspended on MR dampers will pamper operators of off-road vehicles.
There's yet another new trend in the polyurethane elastomer industry, reports Wally Cutler, administrative manager at Innovative Polymers, Inc. His firm has formulated a system for use in rapid prototyping. The 75 Shore D, ultrafast-cure material is meter-mixed and injected into the mold. "This new concept of liquid injection molding holds great promise to produce parts with very little lead time," Cutler adds.
And this is only a sample of even greater things to come. From their meager beginnings in the realm of natural rubber, elastomers, especially the TPE variety, will enjoy a sales gain of at least 7% a year through 1997. That's the prediction of TPC Business Research Group, Lancaster, PA. And of particular interest to design engineers, TPC forecasts that "many new types of TPEs will be developed during that time."
About the Author(s)
You May Also Like