DuPont 'Doubles Up' to Speed Injection Molding
October 31, 2011
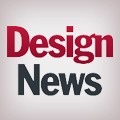
Because so much shrinkage happens during the injection molding of semi-crystalline thermoplastics, these materials usually require longer hold times. In standard injection molding processes, applying hold pressure and dosing are usually performed as two sequential phases. A new In-Mold Hold Pressure (IMHP) technology from DuPont Performance Polymers combines these phases, so they can be done in parallel. This reduces overall cycle times by up to 30 percent.
In IMHP technology, mechanisms that provide both methods are integrated within the mold, one on each side. The first method, applying hold pressure, is conducted by a hydraulically operated piston on the movable side of the mold. The piston is immersed in a specially provisioned and appropriately dosed melt cushion.
In the second method, dosing, the molten material is made available in the hot runner on the stationary side of the mold. This melt volume is fed by pressing it into the cavity using a mechanism that works like a needle valve. DuPont continues to test and refine both methods with the goal of minimizing the additional space required in the combined, two-method mold.
The amount of time that can be saved depends on the degree of material crystallinity and the shot volume. Time savings of as much as 30 percent can be achieved with relatively short overall cycle times or large shot volumes. For example, when molding DuPont Delrin acetal resin using traditional sequential injection molding methods, the hold pressure time comprises a large proportion of the overall cycle time, according to Ernst A. Poppe, European manager for application and processing technology at DuPont Performance Polymers.
"We have conducted numerous injection molding trials with different semi-crystalline thermoplastic grades at our Technical Center in Meyrin, Switzerland, and were able to demonstrate, on the basis of producing standard bars used for tensile testing, the potential efficiency improvements," Poppe says in a press release. "IMHP technology is particularly beneficial when molding DuPont Delrin acetal resin." Delrin acetal homopolymer resins are commonly used in automotive fuel systems, as well as in conveyor belts and chains for industrial assembly.
The trials also demonstrated that no significant changes occurred, in terms of dimensional stability and mechanical properties, between samples produced with standard injection-molded techniques and those produced with IMHP technology.
About the Author(s)
You May Also Like