Designing High Performance Motion Systems with Linear Motors: The Straight Story
April 28, 2004
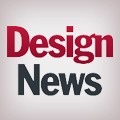
Linear motion positioning stages are found in many applications from material handling and assembly to inspection and testing and employ many different technologies. Just looking at the different drive types one finds linear stages based on flexible belts, ballscrews or leadscrews, and linear motors. Here we will evaluate the use of linear motors in a precision positioning stage, examine the factors that affect its performance and suggest ways to optimize designs
Linear motors have several benefits relative to the other drive types: high speeds, high accelerations, long travels and the advantages associated with their non-contact configuration such as no wear, cleanliness and little to no friction. These benefits make linear motor-based stages very attractive for use in electronics manufacturing and medical or biological applications, but must be balanced against higher costs and increased complexity. The challenge of using linear motors, therefore, is to understand and account for this increased complexity to fully exploit their benefits.
For this discussion we will consider an ironless type linear motor composed of two parts: the forcer and the magnet track. The forcer is analogous to the electro-magnet stator of a common brushless rotary motor, and the magnet track is like the rotor with permanent magnets (see Figure 1 for a cutaway view of a linear stage). Unlike a rotary motor that includes rotary bearings to hold the rotor in place, the designer must mount a linear motor in a linear bearing system to allow linear motion while maintaining proper alignment of the magnet track and forcer.
In the design of a linear positioning stage, the designer can select which part will be fixed in the base of the stage and which part will be moving. For long travel applications, the magnet track is fixed and the forcer is attached to the carriage or moving portion of the mechanism. The carriage is connected to the base with a linear bearing system. Long travel can be achieved by mounting shorter sections of magnet track end-to-end to form long magnet tracks. This configuration is simple in concept but complex in practice because of five main factors: maintaining forcer-to-magnet track alignment; managing stiffness in the linear bearing system to reduce off-axis errors; integrating the linear encoder; managing electrical connections to the moving forcer; and accommodating for external forces such as gravity.
Breaking down the complexity
Maintaining alignment and managing stiffness
For precision applications, maintaining the correct alignment between the forcer and magnet track is critical. This is true not only for proper operation of the motor, but also to reduce the torque ripple that can occur if the forcer moves toward and away from the fixed magnets in the tracks as the forcer moves along them. This alignment must be held in three dimensions. When multiple magnet tracks are used for long travel, the alignment of the magnet tracks must also be held to tight tolerance. The choice of linear bearing system and the configuration of its components ultimately determine the tolerance of this alignment. For a precision linear motor stage such as the Primatics PLG series (see Figure 2), two linear guides are placed in parallel on a precision machined base. The base includes features to accurately locate and align multiple magnet tracks. A carriage is attached to the guides in four places with recirculating ball type trucks. The forcer is attached to the carriage. In addition to maintaining proper alignment between the forcer and magnet tracks, this configuration also provides high stiffness to reduce roll, pitch and yaw errors as the carriage moves.
Integrating the linear encoder
Most linear motor positioning stages also use linear encoders. Care must be taken to locate the encoder to minimize errors due to geometry. If the encoder is placed outside of the linear guides in the example above, yaw angle movement of the carriage will result in encoder position errors. These errors can be minimized by locating the encoder between the linear guides. Similar to the linear motor, linear encoders are composed of two parts: the encoder scale and read head. Like the magnet track, the length of the encoder scale is matched to the length of travel of the stage. And like the forcer, the read head is attached to the carriage of the stage.
Managing electrical connections
Now that the linear motor, linear bearing system and encoder are properly placed, reliable electrical connections must be made to the forcer and read head. The most common method to make these connections is with a cable track attached to the outside of the stage. The cable track routes the electrical signals through cables installed in the track. These cables and the track are fixed to the base at one end and attached to the moving carriage at the other. The designer must select a cable track and cables to maximize cable life and minimize size. Often overlooked, however, is the importance of minimizing the drag force imparted on the carriage from the cable track system. A cable track with cables acts as a spring that wants to relax. When attached to the carriage of the stage, it imparts a force in the direction of the curve of the cable track. This force may be small in most cases, but for some applications, this force can be significant - particularly when it comes to tuning the servo loop. As an alternative, the Primatics PLG stage in our example uses flat flexible cables inside the stage (see Figure 1). These offer the advantage of small size, remove the need for a cable carrier and impart very small forces to the carriage. As a side benefit, this method is better suited to cleanroom environments, takes up less space than an external cable track, and is protected by the stage itself.
Accommodating for external forces
The last factor to consider is the effect of external forces on a linear motor stage. Linear motor stages have inherently lower friction and drag than a similar ballscrew stage because of the non-contact feature of the linear motor. This can create a problem if an external force is applied to the stage carriage. A simple example is using a linear motor stage in a vertical orientation where gravity is applying a constant downward force. The problems are two fold: the external force (gravity) must be compensated for in the servo loop tuning, and allowance must be made for the loss of servo control and possible uncontrolled motion of the carriage (it falls). The most common solution for this situation is a counterbalance. In most cases a counterbalance is implemented by the user, but factory solutions are available from some manufacturers. For example, the Primatics PCR43 series of linear motor stages can be ordered with a pneumatic assisted counterbalance system for vertical applications. This system includes a vertical mounting bracket, a pneumatic cylinder providing the counterbalancing force matched to the payload and a small-profile pulley and cable system that keeps the overall size to a minimum (see Figure 3).
Payoff is better performance for precision systems
The ultimate payoff with proper consideration of these factors is improved performance of the resulting system. This is particularly true for precision systems. Motion control systems have three major parts: motion controller, motor drive and positioning stage. For precision applications, high performance digital motion controllers are typically used. These controllers have very fast servo update rates, high encoder bandwidth, advanced servo algorithms and many features for the system programmer to ease application development. They are often paired with digital servo drives. These drives offer many performance and convenience advantages over their analog cousins: easily configurable operating parameters (current limits, gain, current loop characteristics); encoder-based sinusoidal commutation; and safety features (encoder feedback loss detection, commutation error detection, etc.) Many digital drives also allow operation in either torque or velocity modes.
Most digital motion controllers offer tuning tools that include plotting frequency response of the system to aid in servo loop tuning. Here is where the importance of a good stiff mechanical layout is realized. Off-axis compliance between the forcer and magnet track can allow the forcer to wiggle side-to-side or up-and-down as it moves in the magnet track, which can result in torque ripple. Similarly, lack of stiffness that results in relative movement between the encoder read head and forcer can adversely affect the frequency response.
Both the servo controller and the digital drives rely on encoder feedback to operate the servo loop and commutation timing. This emphasizes the importance of a well designed encoder system. Errors in the encoder output feedback represent misinformation to the motion controller and drive that adversely affect their performance.
Commonly the drive is operated in torque mode where the digital motion controller commands torque (current) to the drive and on to the linear motor forcer. The controller closes both the velocity and position loops based on the linear encoder feedback. Care should be given to reduce unnecessary force perturbations from the mechanics. Bias and feed-forward terms in many motion controllers can be used to counteract the effects of external forces and friction, but it is difficult to tune a servo loop under changing conditions that could be present with poorly implemented cable management.
Precision linear positioning stages using linear motors offer many benefits relative to other technologies for certain applications. However care must be used in the design or evaluation of these products to assure that these benefits can be achieved.
|
|
|
About the Author(s)
You May Also Like