Vistagy Survey Benchmarks Composites Best-Practices
August 15, 2011
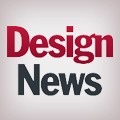
Do you harbor any curiosity as to where peers or other industry leaders stand on domain knowledge and expertise around composite design and manufacturing?
A recent survey conducted by Vistagy attempts to provide an industry benchmark, so companies can gauge where they stand compared with their peers and uncover best-practices that can improve their performance. The survey, based on responses from 140 participants across multiple industries (most prominently in aerospace, automotive, and wind energy), found that use of composite materials is on the rise across sectors. However, a solid 44 percent of responding companies still need to enhance their knowledge of the composite manufacturing process if they want to improve their competitiveness.
"Even as composites extend further and further into industry, there's a general lack of maturity in the processes, as well as overall knowledgeable composites domain expertise in general," Bruce Boes, Vistagy's vice president of product management and marketing, told me. "Even though composites are very widely used in aerospace and have branched out into some other industries, it's still relatively new."
The use of composite materials in design and manufacturing may still be emerging, but it's definitely growing for a number of reasons. The average company responding to the Vistagy survey had 360 engineers on site, with about 10 percent of them actively engaged in composite design. Forty percent of the companies were designing a significant share of their parts (75 percent) in composites, while 30 percent of companies designed less than 25 percent of their parts in the new materials. The remaining 30 percent were somewhere in between.
The primary goals for companies designing with composites were varied. Eighty-one percent were on a mission to reduce weight, 69 percent sought to improve strength-to-weight ratios, 51 percent were attempting to combine multiple parts, 25 percent looked to extend product life, and 31 percent were striving to lower maintenance costs.
One of the key findings of the survey was that many companies (34 percent) are still in the early stages of composite use and are just working to turn metal parts into composites at a 1:1 ratio as part of a weight reduction strategy for the final product.
Best-in-class companies are well beyond this stage. According to the survey results, they are combining six or more parts into one, and 10 percent actually combine 10 or more parts. They are reducing maintenance costs and improving quality by as much as 30 percent by taking advantage of the inherent material properties of composites. And they are reducing weight by 30 percent or more, with 34 percent of respondents claiming they are beating their weight reduction goals.
Best-in-class performers were also the most mature in terms of creating processes around composite design and manufacturing, as well as integrating key technology tools such as specialty analysis software. For example, to achieve target costs, best-in-class performers were investing in simulation tools and other resources, instead of focusing solely on swapping metal parts with composites.
Wind blade design companies, in particular, stood out in the survey results. These designers were more apt than companies in other sectors to design for maintainability and decreased maintenance, and they were more likely to apply analysis techniques and software early in the design process. In fact, the wind energy industry starts with FEA analysis 45 percent of the time, compared to 39 percent for companies in other sectors.
Vistagy's Boes says this is a primary factor in why this sector is out in front with best-in-class results. "A lot of this has to do with what they are designing," he explains. "It's incredibly expensive to maintain offshore blades. You can't really have a failure, because the cost of replacing them can blow the budget."
About the Author(s)
You May Also Like