Combine Risk Analysis Tools to Improve Product Safety
December 8, 2015
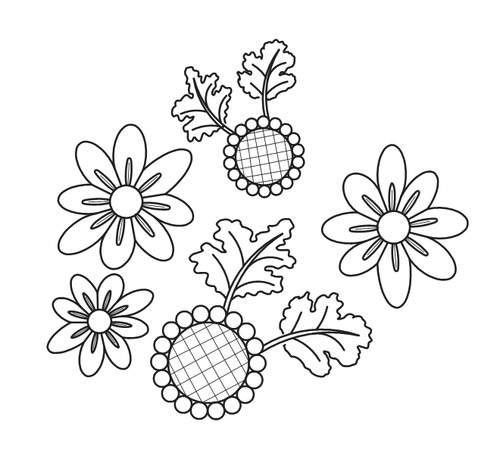
In today's unforgiving product development environments, even the smallest design or engineering mistakes can produce large, costly, and embarrassing consequences. While this threat can be reduced by applying good risk analysis techniques, many companies often perform their assessments too late in the development cycle and only use one type of risk analysis tool.
Design and engineering teams should use a systematic combination of risk analysis tools across the entire product life cycle, carrying out regular risk assessments from the very beginning of the design phase all the way through product launch and beyond. The following methods show how a combination of risk analysis tools can be used together to improve overall risk assessment throughout the phases of product development.
Preliminary hazard analysis
Early on in concept design, a preliminary hazard analysis should be performed to establish upfront baseline risks. By listing all major components and functional requirements of the product and then brainstorming for potentially hazardous situations, teams can start development on the right footing. Standard generic prompts (per ISO 14971 Annex C) can be used, such as "Will the device emit energy?" "Could incorrect display information lead to harm?" or "Could the user interface contribute to a hazard?"
The goal at this stage is to identify as many early hazards as possible, assign each of them a priority, and start mitigating these risks while the design is still relatively flexible. There may be inadequate design detail to create a precise risk model at this stage of development, so comparisons using historical data on similar devices may be used to further improve risk modeling accuracy.
Fault tree analysis
As the design starts to mature, more detailed risk assessment methods can be used. Fault tree analysis' (FTA) top-down method shows effectively how resistant a system is to single or multiple initiating faults, identifying a failure or safety hazard as the top event and then identifying all possible ways in which this event could be recreated. FTA diagrams use a combination of Boolean logic gates to model these relationships. An "AND" gate is used if all the inputs into this gate are necessary for this event to occur. An "OR" gate identifies only one of the inputs is necessary for the event to occur. A basic example of a FTA on a drug delivery pump is shown below:
Failure mode effects analysis
Failure mode effects analysis (FMEA) is a further tool that can uncover faults not caught by fault tree analysis. FMEA is a bottom-up method, effectively listing all initiating faults and identifying the resultant local undesired effects. Each functional requirement for the device is individually evaluated for its potential failure effect.
Severity, occurrence, and detection values are assigned to each failure mode, from which a risk priority number (RPN) can be calculated. Prioritized according to the highest value, PRNs home in on top risks, enabling design and engineering teams to initiate design and process mitigations and improvements. RPNs are then recalculated and the process repeated until all numbers are lowered to acceptable levels. Although somewhat tedious, FMEA is especially effective in systems containing numerous mechanical or electrical components.
READ MORE ARTICLES BY GREG JUNG:
Overall risk reduction
The best mitigation method is to minimize or eliminate the each identified hazard and risk item completely through a design engineering or process change. The second-best option is to design in safety mechanisms or warning features. If neither of these can be done, then the remaining options include reducing risk through warning labels and safety training.
Good risk assessment is not an afterthought and should be done early and often and throughout each phase of the device development cycle. Instead of using just one risk assessment tool, combine the tools at your disposal in a powerful and effective risk mitigation methodology to identify and reduce more problems earlier in the cycle. Performing regular risk assessments using multiple tools throughout the product's lifecycle will improve product safety, decrease time to market, and help eliminate costly recalls.
Greg Jung has more than 25 years of experience designing medical equipment and electro-mechanical products for a wide variety of industries. He also served in various project management roles and has led global, cross-functional development teams for a wide variety of programs. During this time, he developed several award-winning and patented product designs. Greg holds bachelor and master of science degrees in mechanical engineering from the Georgia Institute of Technology.
Like reading Design News? Then have our content delivered to your inbox every day by registering with DesignNews.com and signing up for Design News Daily plus our other e-newsletters. Register here!
Design engineers and professionals, the West Coast's most important design, innovation, and manufacturing event, Pacific Design & Manufacturing, is taking place in Anaheim, Feb. 9-11, 2016. A Design News event, Pacific Design & Manufacturing is your chance to meet qualified suppliers, get hands-on access to the latest technologies, be informed from a world-class conference program, and expand your network. (You might even meet a Design News editor.) Learn more about Pacific Design & Manufacturing here.
About the Author(s)
You May Also Like