Classic fatigue fracture causes bicycle accident, leads to lack of consortium lawsuit
June 22, 2010
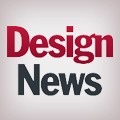
By Kenneth Russell, Contributing Editor
Bicycling is touted as healthy exercise, which it usually is. I commuted 16 miles a day this way for years. But there are hazards. My worst scare was from the door of a Cambridge, Mass. Dept. of Public Works truck that opened right in front of my oncoming face. I somehow ducked to avoid a beheading, but have never figured out just how. My only real injury came while mounting the bike while on an up slope. I threw my full weight on the pedal, which promptly snapped. I hit the pavement with such force that I bounced back over to the other side of the bicycle. My injuries, a bruised leg and wounded pride, healed fairly quickly.
The case at hand for this column involves a similar pedal fracture. The plaintiff suffered back injuries serious enough to cause lack of consortium. I had met the plaintiff and his significant other before the accident. They were young and obviously in love, so the loss of their sex life was a very major blow to them. They sued and their attorney retained me as a metallurgical expert to do a failure analysis.
The subject pedal shaft broke perpendicular to the pedal axis. The sharp threads constitute stress raisers, so the roots are suspect as fracture initiation sites. Such was not the case here, however. The fracture occurred outboard of the threads on the smooth cylindrical surface on the shaft.
Scanning electron microscope study of the fracture surface showed half to be rough and half to be smooth, a classic fatigue failure. The smooth region arose from the stepwise propagation of a crack. Every time the pedal was loaded, the crack moved a very small distance. Finally, the pedal was so weakened by the fatigue crack that it simply snapped, resulting in the accident and subsequent injury.
Often fatigue starts at a crack or notch arising from manufacture. In this case, however, there were several circumferential cracks on the shaft surface, any of which would have led to fracture. The pedal shaft was simply not up to the load it received.
The shaft surface had been hardened to a case depth of 6/1,000 inch. The core was much softer. There are some fairly simple rules for predicting the fatigue behavior of materials of uniform hardness. But how does one predict the behavior of a composite member such as the shaft?
The field known as fracture mechanics provides an answer. In simplest terms it states that failure stress for certain classes of material depends on the presence of cracks normal to the stress axis. Failure occurs when the product of the applied stress and the square root of the crack length exceed a material constant known as the fracture toughness.
The fracture toughness of steel increases with the tensile strength to the point the steel becomes brittle. The hard surface was still ductile enough to have high fracture toughness. Yet, this fracture toughness was not enough to prevent a series of fatigue cracks from forming and propagating. The interior of the shaft had lower fracture toughness, and presented less resistance to crack propagation. The combination of weak steel and a deepening crack resulted in rapid fatigue failure.
The failure could have been delayed if not totally prevented by using more expensive alloy steel that could be hardened all the way through. By the same token, lighter loads on the pedal would have had a similar effect on fatigue life. So, in the end, which way does the finger of guilt point?
The plaintiff was not overweight and so subjected the pedal to an acceptable load. I concluded that the stronger steel should have been used. I was not privy to the outcome of the case.
About the Author(s)
You May Also Like