Building blocks of automation
May 4, 1998
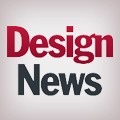
Buffalo Grove, IL--The spread of concurrent engineering has forced design engineers to give more thought to how the products they create are manufactured. It also has forced those who design manufacturing systems to tailor production setups for handling customized designs.
Few companies have a better view of this design-production interface than automation system integrators. This rapidly growing class of companies has played a major role in the big productivity gains that the U.S. has enjoyed in the '90s.
Typical is the Illinois-based Mid-West Automation Systems, which started in 1965 as a designer of machines to produce electrical connectors. Over the years, the company, part of DT Industries, has grown rapidly by developing specialized manufacturing cells to produce, test, and inspect all manner of products. Typically, the systems are modular, allowing customers to expand or change the cell, according to product mix.
What do Mid-West's customers--mostly Fortune 500 types--want most from automation systems? Engineering Director John Carlson notes that the number one demand is higher parts-per-minute production rates in a minimal amount of floor space. Flexibility or reconfigurability is key because of the short life of many products. Meeting global safety standards also has become crucial, as machines get shipped from place to place.
To meet such demands, Carlson cites several trends:
- Servo motors are increasing in use because of their ability to provide closed-loop feedback for accurate placement.
- Actuation systems for high-speed, compact pick-and-place systems often involve ball screws or belts driven by servo motors.
- In controls, PC-based solutions are clearly on the rise--as are open systems. "We like to plug in anybody's vision card, anybody's servo card," says Carlson.
- The design of pneumatic circuits is quite important because of the demand for higher piece rates. Carlson sees more use of smaller pneumatic valves mounted right at the pick head, or use of constant-vacuum pick heads to accommodate quicker reaction.
- In sensors, proximity and photo cells work well for part detection. But when the applications are more demanding, as in color detection, automation designers opt for vision systems.
- Absolute encoding--either rotary or linear--"is the way to go," notes Carlson. "The days of the stepper motor are pretty well gone because parts lose positioning too easily."
- For part tracking, bar codes are becoming more and more popular.
- And on the regulatory side, components with the CE mark, such as safety switches or lasers used in safety guard systems, are in big demand.
In developing new automation systems, Mid-West tries to work with a customer's design engineers as early as possible. Carlson advises engineers to play close attention to anything within their designs that will complicate parts feeding or slow production rates. To make it easier to reconfigure an automation system, designers also would do well to adhere to a standard family of parts for their products. And, whenever possible, they need to keep parts count to a minimum.
"A great idea isn't any good if you can't produce it," says Carlson. "So it is very important that design engineers keep in mind both the technology and the skill set available on the manufacturing side."
About the Author(s)
You May Also Like