Beyond 'bang-bang'
June 21, 1999
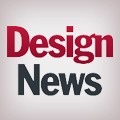
If you're like most engineers, you probably believe that pneumatics is no more than a "bang-bang" technology. Air cylinders, after all, have long been used to quickly move loads from one end of a stroke to another, with no stops in between.
But that's changing. For the past five years, a handful of air cylinder manufacturers have been teaming with sensor makers to add brains to pneumatic brawn. The result is that many of today's pneumatic actuators can perform two feats that were unheard of in the bang-bang era.
The first of those feats is feedback. Many of today's actuators "know" where they are within their prescribed stroke. What's more, they can report their position to a controller, which tells the operator through a display.
The second of the two new feats is position control. In some cases, users report that they've positioned loads to within half-a-thousandth of an inch. In many more cases, they consistently achieve positioning accuracies of two or three thousandths of an inch.
For users of motion control equipment, that's good news. "Pneumatics has always been an inexpensive, easy way to move a load from place to place," notes Fred Howse, vice president of business development for Penny Giles Controls Inc., a sensor manufacturer in Schaumburg, IL. "Now, users are starting to see it as a cost effective way to precisely position that load."
Incorporating sensors. The key to the new emphasis on positioning is electronic control. Up to now, pneumatic cylinders have found their greatest use in classic bang-bang applications, such as pushing, clamping, and braking.
Precise positioning, however, was another matter. The reason for that was simple: Air is hundreds of times more compressible than hydraulic oil, and its behavior is inherently non-linear. As a result, engineers struggled to move an air cylinder's piston to within a quarter-inch of its target.
But by developing controllers that incorporate the non-linear characteristics of air in their algorithms, engineers changed all that.
With the advent of such controllers, cylinder makers needed only to add sensors to the cylinders in order to close the loop. And in today's new breed of cylinders, they're doing that.
Cylinder manufacturers now employ sensors that fall into one of three categories.
Potentiometers. The simplest and least costly of sensors used in air cylinders, potentiometers are like big resistors. The resistor--in the form of a sliding mechanism along the length of the cylinder--produces a variable output voltage. As the load moves along the resistor, the output voltage changes. And as the output voltage changes, the controller "knows" where the load is positioned.
The primary advantage of a potentiometer is cost. Potentiometers, in many cases, cost less than a third of competing technologies.
Magnetostrictive transducers. These sensors employ the phenomenon of magnetostriction, in which certain alloys (usually nickel alloys) deform in the presence of a magnetic field. By measuring the time it takes to send an electrical signal across a deformed magnetostrictive wire, sensor manufacturers can precisely pinpoint the position of a load on a pneumatic cylinder.
Magnetostrictive sensors offer two key advantages. First, they're very accurate. Second, they are non-contact devices. As a result, they last far longer than potentiometers.
The disadvantage of magnetostrictive sensors is cost. Magnetostrictive sensors can cost between $300 and $800, which is why cylinder makers tend not to use them for simple position feedback. They are ideal for such applications as X-Y tables, where precise positioning is critical.
Inductive sensors. Like magnetostrictive transducers, inductive sensors rely on the presence of a magnet to produce a position signal. Their position signal is slightly less precise than a magnetostrictive sensor's, but they cost less. They also offer the advantage of non-contact performance.
In pneumatic applications, inductive sensors have not yet attained the popularity of magnetostrictive sensors or potentiometers. But experts expect their use to increase.
Internal or external? The other major feature on which cylinder manufacturers differ is mounting.
Mounting the sensor internally offers several advantages. The first is protection. Internal mounting protects the sensors from dust and dirt in industrial environments.
The second advantage is packaging. Cylinders employing internally mounted sensors tend to offer a more compact package. "There's nothing hanging off the side of the cylinder," notes Mark Rossi, product manager for MTS Sensors (Cary, NC). "It makes for a sleeker package."
The advantages of external mounting are considerable. Externally mounted sensors are simpler to install and easier to retrofit. They don't require cylinder manufacturers to make special changes to the cylinder body. In the end, sensor makers say, that translates to lower cost. "People who use pneumatics for positioning are looking for lower-cost feedback solutions," notes Rob Matthes, product line manager for Balluff Inc. "This helps meet those needs."
The next step toward closing the loop, however, may be to mount the sensor internally, in close proximity to the controller. A new system from MTS Sensors and Paw-Taw-John (Rathdrum, ID) integrates the sensor and controller into the cylinder's end cap. The advantage: faster data updates.
Known as the ServoSensor, it offers a servo loop update time of about 500 msec. In contrast, conventional configurations typically offer 2 msec--about one-fourth the speed. The reason for the higher speed: proximity. "All the data is being processed right there in the cylinder head," notes Jerry Johnson of Paw-Taw-John. "It doesn't need to travel back and forth from an external controller, which takes time."
Ultimately, such innovations are expected to increase the demand for "smart" pneumatic systems. "More and more facilities are looking for a medium that's environmentally friendly, like air," Johnson says. "Among industries that move light loads and need to control motion, the demand is going to continue to increase."
FESTO CORP., Hauppauge, NY
Sensor type: Potentiometer
Mounting: External
Feedback or positioning: Both
Electropneumatic "Smart Soft-Stop" systems direct ramping speed of rodless pneumatic cylinders to provide controlled starts and stops for high-speed, gentle-handling applications. They effectively eliminate high cost and complex motion profiling tasks generally associated with electromechanical drives and servo axis controllers. Soft-Stop systems reportedly offer 30% faster travel, higher machine cycle rates, and lower maintenance while reducing noise and vibration.
The system consists of four basic components: pneumatic rodless actuator, analog linear potentiometer, proportional flow valve, and an end position controller module. The system operates independently, or in conjunction with a PLC or electrical input/output source. No programming is necessary and no I/O or software changes are needed.
Festo's controller, known as the SPC-10, provides a closed-loop means of measuring and controlling the direction and rate of the piston displacement. Feedback from an externally mounted analog linear potentiometer is processed and compared to the set point to derive the appropriate acceleration/deceleration.
SMC PNEUMATICS, Indianapolis, IN
Sensor type: Magnetoresistive (non-contact)
Mounting: Internal
Feedback or positioning: Both
SMC manufactures several types of position-sensing pneumatic actuators. All employ solid-state, non-contact, magnetoresistive sensors to read magnetic etchings. Resolutions as tight as 0.01 mm are achieved with repeatability of plus or minus 0.02 mm. A pair of sensor heads produce digitized sine and cosine waveforms that enable distance and direction of travel to be determined by a counter or controller.
SMC uses this sensing technology to create actuators with both feedback and positioning capabilities. The company's CE1 unit offers resolution of 0.1 mm with repeatability of plus or minus 0.05 mm when used with a CEU1 counter. A more recently released unit, the CEP1, achieves 0.01 mm performance with plus or minus 0.02 mm repeatability. Both of these cylinders can be used alone, or in tandem with another cylinder, to determine position of a piston rod.
SMC also combines sensing functions with brakes in both tie rod-type cylinders and rodless cylinders. Both are capable of resolving to 0.1 mm with a repeatability of plus or minus 0.05 mm. The tie rod-type senses position off the piston rod; the rodless employs an integral scale bar. When teamed with the company's CEU2 controller, these cylinders can learn to position within plus or minus 0.05 mm of a set point.
BIMBA MANUFACTURING, Monee, IL
Sensor type: Potentiometer
Mounting: Internal
Feedback or positioning: Positioning
Bimba's Position Feedback Cylinder (PFC) contains an internally mounted potentiometric linear resistive transducer (LRT), resulting in a compact unit. The LRT acts as a voltage divider, providing a voltage output that varies proportionally with the cylinder's position. The cylinder output approaches zero volts when fully retracted, and increases to full scale when extended.
When coupled with a Bimba DPM controller, accuracy is plus or minus 0.001 inches per inch of stroke. As a result, it can be used for process quality applications, because it can work and gauge parts at the same time.
When used with a special low friction option, the PFC also can serve in closed-loop pneumatic positioning applications. The low friction option uses seal and lubrication options that provide very low breakaway forces (the amount of force needed to generate cylinder movement with only one side of the cylinder pressurized.) It also produces low breakout forces (the amount of force needed when both sides are pressurized).
Using a PLC- or PC-based controller, the PFC can also do "on-the-fly" applications. Set points can be programmed in ladder logic, rather than mechanically.
IMI NORGREN INC., Brookville, OH
Sensor type: Potentiometer
Mounting: Internal
Feedback or positioning: Feedback
A Linear Resistance Transducer (LRT) (potentiometer) employs a simple resistive element and a wiper to provide an analog output signal of cylinder position. The LRT probe is installed into a "gun-drilled" cylinder piston rod. A wiper carriage assembly travels with the piston as the cylinder extends and retracts. As the piston and rod assembly move, a measurement of cylinder position is transmitted to an electrical interface, which reads the position. Position repeatability of plus or minus 0.001 inches is common with LRTs. With the exception of a three-pin electrical connection, there is no visible difference between an LRT-equipped cylinder and a standard NFPA tie rod cylinder.
PARKER HANNIFIN CYLINDER DIV., Des Plaines, IL
Sensor type: Magnetostrictive and potentiometer
Mounting: Both
Feedback or positioning: Both
Parker Hannifin's positioning feedback cylinders use magnetostrictive linear displacement transducers (LDT) and linear resistance transducers (LRT). They apply those sensors to several pneumatic cylinder styles, including: NFPA (steel and aluminum), ISO 6431, and rodless. Sensors can be embedded in the piston rod to maximize space and protect the sensor, or they can be mounted external to the cylinder and mechanically coupled to the rod ends. Also, a non-contact LDT can be mounted externally to an aluminum body cylinder with a magnetic piston. No mechanical attachment to moving parts is required for this option--the sensor provides position feedback by detecting the standard piston magnet located inside the cylinder.
Future Applications
Industrial gearboxes
Automotive transmissions
Aerospace hydraulic systems
Industrial process control
Theme park motion bases
About the Author(s)
You May Also Like