CV Joint Delivers More Torque in a Smaller Package
Designers can opt for best combination of torque capacity, size, and weight.
July 10, 2017
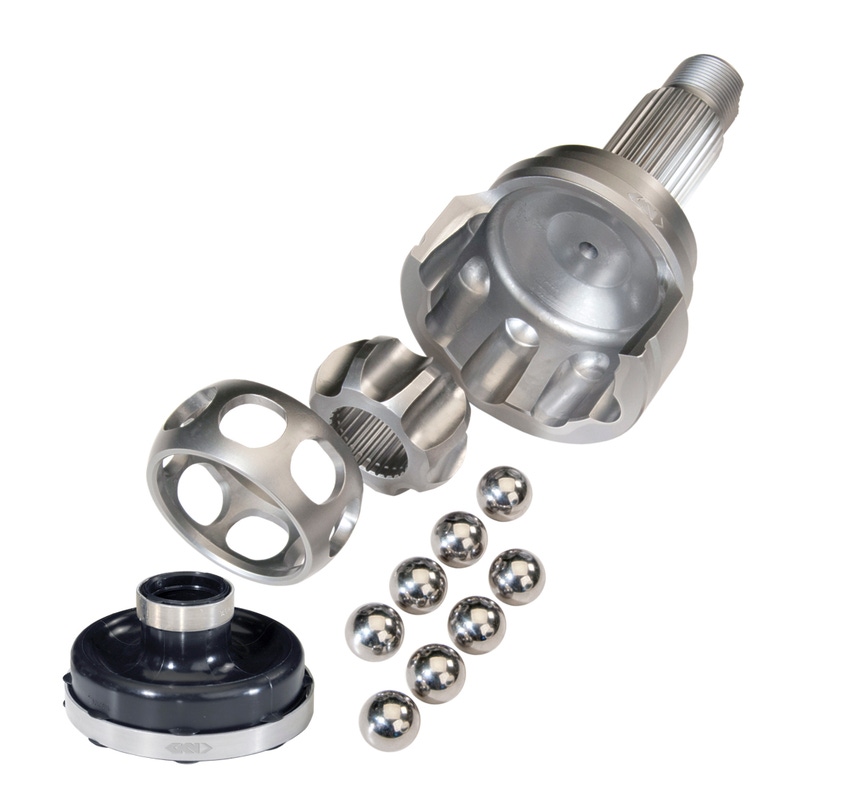
A clever new constant velocity (CV) joint is smaller and lighter, freeing up room for space-constrained automotive designers.
The VL3 CV joint, currently being used on the side shaft of independent rear suspensions on the BMW 5 Series and 7 Series luxury vehicles, is said to deliver 27% more torque with no increase in packaging size.
“We’re transmitting power more efficiently, doing it in less space and, at the same time, saving some weight,” Edward Kwon, senior director of engineering for GKN Driveline, told Design News.
The VL3 CV joint uses GKN’s Countertrack design, in which every other track faces in the opposite direction. It also employs eight ball bearings, instead of the standard six, giving it greater torque-carrying capacity. (Source: GKN Driveline) |
The VL3 accomplishes that through the combination of two advancements. The first advancement is the use of GKN’s Countertrack technology, in which every other ball bearing track faces in the opposite direction. Countertrack is a compact way to enable the CV joint to move angularly (articulate), while also moving axially. The axial capability is particularly important in allowing the CV joint to “telescope,” which is needed to accommodate the length changes of a car’s axle, especially as it drives along bumpy roads.
The product’s second advancement is its use of eight ball bearings, rather than the more standard six-ball design. Using eight smaller balls, instead of the six larger ones, results in a smaller design envelope, Kwon said. “Having more ball elements enables us to carry more torque in the same outer-diameter packaging space because each of the balls are stressed slightly less,” Kwon told us.
In the past, CV joints used fewer balls (as few as three in the 1960s), largely because more balls added to the challenge of manufacturing the product. But GKN solved that problem by employing S-shaped tracks in the housing to simplify assembly.
“It’s always been a compromise between manufacturability and functionality,” Kwon said.
The additional torque-carrying capacity provides designers with more choices. They can increase torque capacity by 27%, or reduce package size by up to 10% and cut weight by 25%, or opt for a combination of those benefits.
Kwon said that such choices are important for designers of feature-packed vehicles, like the BMW 5 Series or 7 Series. “There’s a need for components to be lighter and smaller, so that there’s room to include all of the features that consumers have come to expect,” he told us. “This enables them to make those choices.”
The VL3 CV joint is being used on the side shaft of independent rear suspensions on the BMW 5 Series. (Source: BMW) |
For its ability to provide designers with those choices, the VL3 was the winner of Automotive News’ PACE innovation Award in December, 2016.
Such recognition is important, Kwon said, given the industry’s emphasis on fuel efficiency. “There’s a drive to make powertrains more efficient, which is good, but when you make engines more efficient, the power still has to go through the gearbox and out to the wheels,” he said. “That’s where we come in – we want to make sure the losses out there are minimized.”
Senior technical editor Chuck Murray has been writing about technology for 33 years. He joined Design News in 1987, and has covered electronics, automation, fluid power, and auto.
About the Author(s)
You May Also Like