Toyota takes auto assembly digital
February 5, 2001
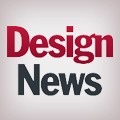
Tokyo-Time is money, especially in the competitive automotive field where cutting the time and cost of car development has turned into a global race. To maintain its world-wide competitiveness, Toyota Motor Corp. has successfully introduced digital manufacturing software, slashing car development time from 18 months to 13 months, while cutting time-consuming and costly mid-stream design changes.
Toyota is using a software package named Envision from Delmia Corp. of Troy, Michigan. But the automaker supplements this software with a knowledge database of problems to watch for during design, as well as a conferencing system that allows widely dispersed engineers and factory workers to see and talk to each other while simultaneously viewing the same drawings. Toyota calls this its Visual and Virtual Communication, or V-Comm, system.
|
"Toyota's strength is in manufacturing, and we've adapted the software to reinforce this strength," explains Takatoshi Negishi, general manager of Toyota's Vehicle Information Research Department. The database, he says, allows sharing of Toyota's institutional knowledge while the conferencing system is becoming a key part of using feedback from factory workers in the design process.
Toyota first tested the system in 1996 for the design of a vehicle cockpit. The company extended its use to an engine compartment in 1997. Finally, last year, Toyota felt confident enough to rely on the software entirely for the bB, a compact wagon aimed at younger car buyers that was unveiled this past February.
Traditionally, clearances among parts or components and the ease of assembly has been checked by building first-stage and second-stage manufacturing test cars. For the bB, Toyota eliminated the test cars entirely. As Toyota uses it, the software allows designers as well as assembly line workers to view individual parts as they are being installed into the car. Interfering parts turn red for easy identification. To check for ease of assembly, the software can simulate the installation using a virtual worker to validate clearances for handling and making connections, even considering the tools to be used.
Knowledge database and communications. This virtual assembly is supplemented by Toyota's own knowledge database, a compendium of problems and things to watch for accumulated over decades. Negishi says computerizing the database and using it in tandem with the visualization software makes it far more useful. There are more than 150 bits of know-how just for the cockpit, covering, for example, recommended clearances between the shift lever and the console housing.
Even sounds can be recorded and added to the database. For instance, engineers had concluded that a door lock used on a previous car sounded "cheap." To avoid such problems in the future, details of the lock's design and even the sound of the lock were put into the database.
The communications portion of the package is essentially enhanced video conferencing software that allows engineers and factory workers to jointly examine the assembly simulations and exchange suggestions. These conferences can be between the engineering center and the factory or between factories in Japan and overseas. Negishi notes that prior to introducing the V-Comm system, different factories relied primarily on faxes to spread news of assembly procedure changes. It sometimes took as long as 2 months to ensure that all factories had successfully accounted for modifications. Now that same kind of information is reviewed and agreed upon in real time.
This system, he adds, is also used during design to gather suggestions and feedback from floor workers, unveiling problems that might not be caught until the car moved into mass production.
Successful results. The success of using the software can be seen by comparing how car development times and mid-stream changes have evolved. Ten years ago, the development of the Toyota Crown sedan took 24 months, required building two manufacturing test cars and involved more than 8,000 design changes. In the mid-1990s, Toyota introduced concurrent engineering and rapid prototyping that cut development time to 18 months and further reduced design changes. With the adoption of the digital manufacturing program and the elimination of manufacturing test cars, development time was cut to 13 months and the number of design changes cut to less than 400.
Negishi says they chose packaged software simply because it made more sense rather than start their own software development program from scratch. But he adds the Delmia software has the flexibility to be adapted to a user's particular needs. He claims that with their focus on "digital assembly," Toyota believes they are using the software in a rather unique way. The software runs on Silicon Graphics workstations and Windows NT PCs.
For the future, they are now developing most of their new cars with V-Comm. In some cases, particularly where a completely new engine will be incorporated into a new platform, they will probably opt to build prototypes, Negishi says. But they hope to increasingly rely on the no-prototype model of new car development. They are also working to extend V-Comm to additional parts suppliers. "We've got to continually cut the time and number of midstream design changes to stay competitive," he concludes.
About the Author(s)
You May Also Like