Lessons from QS-9000
October 6, 1997
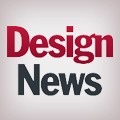
Chicago, IL--As 1997 draws to a close, the handwriting is on the wall for companies supplying the auto industry: Make QS-9000 certification an urgent priority or risk being shut out of future contracts.
QS-9000, as most engineers know, is the auto industry's supplier quality standard that's based on ISO-9000. Not only does it contain additional provisions peculiar to that industry but it is also being evaluated closely by other manufacturing sectors, such as aerospace.
How important is QS-9000? Ask Richard Dagiel, manager of corporate quality for NTN Bearing Corporation of America. "It is absolutely necessary for NTN to meet the objectives of the QS-9000 and ISO international standards," says Dagiel. "Anymore, customers demand it, and the Big Three of the automotive industry mandate it. If you don't comply with these standards, you can't expect to gain any new business or have a very big piece of the global market."
Dagiel just helped steer NTN through the QS-9000 certification of its Elgin, IL, plant. By the end of 1998, he expects all six North American NTN plants supplying the auto industry to be certified.
It's no easy process. Bud Batcher, NTN VP of marketing, notes that QS-9000 registration entails a lot of expense, careful documentation, and the expertise of outside consultants. Paving the way for registration typically takes a year and a half.
With one half of its revenues tied to automotive, NTN had no choice but to pursue the standard. Yet the process was a "real eye opener," setting in motion a number of changes within the company--
Elimination of many "wheel-spinning" procedures that offered little value added to product development or customer service.
New steps to redesign many manufacturing processes.
A conscious decision on the part of management to empower employees to take more responsibility for their jobs.
Renewed commitment to continuous improvement in products and processes.
In addition, the pursuit of QS-9000 prompted a greater sense of the contributions of all departments within the manufacturing enterprise. "Those of us in engineering hadn't fully appreciated the role of people in such areas as manufacturing and inventory control," says Dagiel.
Dagiel and Batcher believe that QS-9000 and ISO-9000 have taken the quality movement well beyond the product itself, which was often the focus with the Commerce Department's Malcolm Baldrige Award.
"The quality movement has shifted from the hardware side--issues like statistical process control, defects per thousand, and high-precision processes--to the soft side, the people side," says Batcher.
These soft-side issues include such goals as building successful teams, the quality of the work environment, and a broader range of customer services, such as fast delivery and strong applications engineering support. NTN, for example, provides customers not only highly precise, defect-free bearings but also address mounting, lubrication, and system-design problems.
The growing demands of customer service have become so important, explains Batcher, that suppliers will have to be just as careful picking their OEM customers as the OEMs are in choosing suppliers. "You can't afford to just go out and double the number of customers," says Batcher.
NTN's managers stress that it is wrong to say that quality is a "given" in today's environment. "There are many sides of quality," concludes Batcher, "and the companies that survive and grow will be those that embrace this broader definition."
About the Author(s)
You May Also Like