High-speed motor and drive target next-generation fuel cells
October 20, 1997
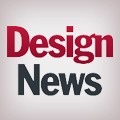
Los Angeles, CA--An experimental high-speed motor and drive may help engineers create long-range, flexible-fueled electric vehicles for use early in the next millennium. Powering a small turbine compressor--not the car's wheels--the motor feeds oxygen (air) to a prototype fuel cell, one of several different designs bidding to bypass batteries as the primary source of onboard electric energy. Developed by AlliedSignal Aerospace (Torrance, CA), the motor turns the turbine at a dizzying 104,000 rpm and is controlled by a custom drive supplied by Westamp (Chatsworth, CA).
The effort is part of a DOE project involving Detroit's Big Three and many supplier companies to develop viable electric-vehicle fuel cells. Many engineers see fuel cells as a way to leapfrog the problems with batteries and enable electric cars with the range and refueling flexibility of today's gasoline vehicles. Invented by Sir William Grove in 1839, fuel cells remained laboratory curiosities until NASA began placing them on space vehicles in the 1960s.
But the past few years have seen renewed interest for application in electric cars. In fact, Daimler-Benz unveiled a fuel cell A-Class car, known as NECAR 3, at the Frankfort auto show in September.
Fuel cells combine hydrogen and oxygen to produce electricity and a friendly exhaust product, water. While hydrogen could be supplied directly from tanks, this method faces several obstacles: no current infrastructure exists to supply it; and the public commonly believes hydrogen is uncontrollably explosive.
'Reformer' fuel cells are considered a practical way of generating electricity for electric cars. They derive the hydrogen they need from a readily available source, such as methanol. A compressor feeds oxygen (air) as the other fuel-cell reactant. |
As an alternative, hydrogen can be generated on demand from readily existing fuels, such as methanol, in what are called reformer fuel cells. Typically, after the hydrogen is extracted from the methanol, the remaining components are burned in the turbo-compressor to aid efficiency. (The theoretical efficiency of fuel cells is considered to be much higher than that of internal combustion engines.)
Oxygen, on the other hand, can be supplied directly from the air. It's here where the high-speed motor and drive play their part. The DOE is evaluating various air-compressor methods, and AlliedSignal's turbo-compressor is one of them. Its advantages are compactness, low weight, and superior efficiency compared to scroll or piston compressors. The prototype (which leaves much room for optimization) measures roughly 12 x 9 inches and weighs less than 20-lbs.
A custom, ultra-high speed brushless servo motor drives AlliedSignal's turbine compressor at 104,000 rpm. The compressor feeds air into an experimental automotive fuel cell. |
Engineers at AlliedSignal designed the turbo-compressor to feed 11-lbs/min of air at a pressure ratio of 3.2:1 to the fuel cell. It's turned by a custom permanent-magnet, brushless servo motor turning at 104,000 rpm. "Our uniqueness is that we can make permanent magnet motors that operate at turbine speeds," says Bob McConnell, electrical systems engineer.
The motor is a derivation of a basic family developed by AlliedSignal. It contains a simple rotor to keep down windage. At the center lies a permanent magnet contained by a stiff sleeve which attaches directly to the turbine shaft. Outboard of the rotor is a stator stack of laminations and windings. Output is 7.7 hp at 104,000 rpm on 300-400 volts.
Inside a reformer fuel cell hydrogen-derived from methanol-combines with oxygen from the air to create electricity and a pleasant exhaust, water. |
The motor rides on air bearings chosen for several advantages. Namely, they don't use oil, which can easily contaminate a fuel cell. And they handle extremely high speeds with aplomb. Their downside? Below about 10,000-15,000 rpm--the point where the shaft is finally supported by a cushion of air--the drag can be rather high.
This drag defines the peak current for Westamp's drive. "It has to output 150 amperes up until "liftoff" of the shaft," says Brad Landseadel, president and CEO of Westamp. Average output is 70 amperes RMS at up to 400 volts DC. Peak power output of the drive is 48 hp at 300 volts, which outputs a more than necessary 38 hp at 104,000 rpm.
Surprisingly, the drive is a one-off version of the production SP 150 series. Engineers at AlliedSignal selected Westamp partly for this reason. "We chose the SP 150 because it uses programmable logic and gate arrays that allow for easy customization," says Landseadel.
An example of that customization can be witnessed with the motor feedback. Instead of the normal encoder feedback, AlliedSignal used only Hall-Effect sensors. This prompted engineers to modify the drive to derive velocity signals from the Hall signals. Engineers take the Hall signals and redirect them with gate array logic into a frequency-to-voltage converter, and then use the Hall signals for a velocity signal in place of the usual encoder signal. "It is very coarse information to work with, but we had to make do to accomplish what they wanted," Landseadel explains.
And what they wanted to do was formidable. "They told me 104,000 rpm, and I thought the decimal point was off," he says. "We've never worked on anything like this."
To attain this high speed, engineers had to optimize the current loops. Because no complete motor was available, they performed a mathematical analysis of the drive and a single coil of the motor. After generating a Bode plot to find the frequencies and break points, they were then able to compensate the amplifier so that the motor and drive functioned as a complete package.
To date, the prototype has run past 55,000 rpm, and engineers say the full 104,000 rpm should be attained within weeks. "We had always said that the programmable logic in our devices allowed for great flexibility," says Landseadel. "This was really the first application to prove that."
Other Applications
High-speed machining
Turbomachinery
Compressors
Additional details...For motor drives, contact Westamp, 9006 Fullbright Ave., Chatsworth, CA 91311, (818) 709-5000, [email protected]
For turbomachinery, contact Mark Gee, AlliedSignal Aerospace, 2525 W. 190th St., M/C TOR-36-2-93084, Torrance, CA 90504
About the Author(s)
You May Also Like