Transforming for Analysis-First Design
March 1, 2010
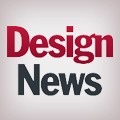
For years, Graco engineers pumped out new products using a trial-and-error design process. They started with a benchmark design, scaled it up with the requisite bells and whistles and built a physical prototype to identify potential performance problems. Next, they worked out the kinks with a new design then circled back to the prototype and test phase, only to start anew. The workflow was functional, but admittedly time consuming and it rarely hatched an optimal design.
Graco's engineering dynamic was put to the test when a team was charged with building a completely new offering: A state-of-the-art plural spray gun for which there was no benchmark. Building multiple physical prototypes would be far too costly, not to mention, greatly impede the company's ability to be timely to market. Using a Computational Fluid Dynamic (CFD) analysis tool, the team was able to simulate critical fluid flow for each design iteration, allowing it to quickly zero in on an optimal configuration. News of the team's success spread throughout the Graco engineering ranks and, over time, multiple teams across all divisions revamped their engineering workflows, making CFD analysis an integral part of the early stage design process.
“Now teams are building time into their schedules to account for CFD,†says Rick Anderson, senior product engineer at Graco, which delivers systems and applications for a variety of fluid handling applications. “On product designs where it's critical to know how to optimize flow and mixing, it's become obvious that this is a useful tool and engineers are making time for it.â€
Whether it's CFD, Finite Element Analysis (FEA) or other forms of simulation, companies like Graco are making it a priority to modify their engineering routines to embrace analysis far earlier in the design process. Simulation work is also branching out to a broader base of mainstream engineers — not just analysis experts. The transformation, proponents say, can be a game-changer for engineering organizations, allowing them to shorten design cycles, reduce costs associated with prototyping and over-designing around materials and, ultimately, boost their ability to conduct more what-if scenarios to hone in on an optimal design.
“We believe every engineer who designs a part should be doing simulation on that particular part,†says Kishore Boyalakuntla, product manager, simulation at SolidWorks. “Every engineer thinks about how a design will work in real life and until they go into a test lab and put it under a test machine, they can't prove it. Simulation is a fantastic way of proving ideas and concepts.â€
Product Watch
SolidWorks, along with most other CAD and CAE tool vendors, have been on a mission this last year to ensure that simulation is up for that kind of starring role. The CAD companies have increasingly been adding basic simulation functionality to their core suites, while the specialty simulation vendors have reworked their programs with automation and other ease-of-use capabilities to make them more accessible and familiar to the mainstream engineering audience. While the buzz of activity has certainly raised awareness around the benefits of integrating simulation into early stage design, there remain cultural and organizational challenges to getting individual engineers on board with making changes to their work patterns, as well as creating synergies between groups (mainstream engineers and simulation experts), which have historically operated independently.
At SolidWorks, the strategy is to embed simulation into the core CAD tool and to map its functionality and workflow to the way engineers are used to working. Autodesk, too, believes the way to promote simulation earlier in the cycle is to make it more accessible, both by embedding functionality into its core offerings and also through automation and alternative delivery models. In that vein, the company recently announced FatigueAnalysis Wizard for Autodesk Algor, a wizard interface that guides users through the steps required to perform complex fatigue analysis. “We want to remove a lot of the burden (around simulation),†says Grant Rochelle, Autodesk's director of mechanical simulation. “There's a lot of work involved in doing this today — meshing, boundary conditions, loads, constraints. We want to figure out how much of that we can lift off users and shift to automation.â€
For simulation leader ANSYS and partner SpaceClaim, the idea isn't to make simulation more CAD-like to attract CAD users, but rather to open up the discipline to engineers who typically haven't used CAD or aren't married to a single CAD system. ANSYS is offering a version of the SpaceClaimDirect Modeler as part of its ANSYS Workbench to allow engineers to quickly create 3-D models or modify existing ones to validate their designs upfront as opposed to waiting until they have a detailed CAD model in hand. “The real trend in simulation is not providing tools for CAD guys, but for engineers who don't use CAD,†says Blake Courter, co-founder of SpaceClaim. “There's more opportunity to use simulation along with a lightweight, easy modeler that's not designed for detailed design.â€
High-end simulation vendor SIMULIA, a Dassault brand, sees the evolution of analysis-led design in a completely different way. While it too is trying to branch out to mainstream engineers, it believes the only way to do so effectively is to provide a more advanced tool with robust functionality that can compensate for the lack of domain expertise by non-analysis experts. “The tools you're putting in the hands of non-experts need to be robust and give you a correct answer to a question in the vast majority of cases,†says Ken Short, SIMULIA's vice president of marketing and strategy. “You need the tool to do some of the work an expert might be able to do on their own.â€
Cultural & Organizational Challenges
Technology improvements aside, the critical factor for advancing the analysis-led design movement is to promote process and cultural change within the engineering organization. While some companies, like Graco, can successfully usher through these changes via a grassroots campaign, other companies will need top-level management support and champions to convince the engineering ranks to modify long-standing workflows. Getting mainstream engineers and analysis experts to collaborate on simulation throughout all stages of design as opposed to handing over a completed 3-D model for test and verification is a major hurdle organizations need to cross. Mainstream engineers traditionally have been hesitant to embrace simulation because they view it as yet another domain to learn when they are already over-taxed. Analysis experts, on the other hand, have been territorial about simulation since they view that domain as their value-add.
“The teams need to be combined to have stakeholder responsibility for overall performance,†explains Short. “It's not the design team's job to create a shape or the engineering team's job to make sure it works before building a prototype or the test team's job to do the fine-tuning. You have to be a holistic team to make sure that the product works.â€
Integrating the analysis experts into the mainstream product development ranks and enlisting their help in defining, documenting and capturing the appropriate simulation workflows and defining benchmarks is key as is creating incentives to encourage experts to share their domain expertise and serve as mentors. By handing off some of the simulation tasks to mainstream engineers, analysis experts will be freed up to focus on more complex simulations — a scenario that can hold appeal to get them on board.
At TiLite, a manufacturer of high-end custom wheelchairs, the march toward analysis-led design has grown with the organization, blossoming from a discipline used by one or two key engineers to a routine practice embraced by most of the engineering team. By enlisting SolidWorks Simulation as a regular part of the design process, TiLite has been able to make its wheelchairs safer, lighter and more affordable, according to Alan Ludovici, vice president of engineering. In one instance, the team was able to virtually prototype an injection-molded composite replacement for aluminum footrests, which were prone to breaking, saving $11 per chair in materials costs. Today, about 60 to 70 percent of all TiLite parts go through simulation, and as engineers come on board, they are actively encouraged to learn and incorporate simulation. “Being a small company, we don't have a lot of money to throw out if we make mistakes,†Ludovici says. “(Simulation) lets us build the best thing we could possibility build without it breaking to avoid over-designing.â€
About the Author(s)
You May Also Like