Thermopolymer-driven actuators challenge hydraulics
February 20, 1995
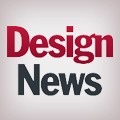
Eastlake, Ohio--Although indispensable to aircraft, hydraulic systems are costly in a number of ways. To name just a few, they leak, make noise, vibrate, and require elaborate power development, distribution, and control systems. Worst of all, they add weight-an aircraft's biggest enemy.
Seeking to overcome the shortcomings of hydraulics, research funded by the Air Force's Wright Laboratory Flight Dynamics Directorate may have discovered a partial solution in TCAM (thermochemically activated motion). Inventor Edward Schneider, founder of TCAM Technologies, calls the new technology "a solid-state, electrically controlled method for creating hydrostatic pressure vessels using thermally expanding polymers."
Though they look like hydraulic cylinders, TCAM actuators develop force without vibration or sound. They work when a system heats the enclosed polymer, which then liquefies and expands against a piston or diaphragm. Eventually the device overcomes any preload and load forces, and the piston moves outward. The actuator retracts upon cooling. Actuation speed depends upon the polymer's heating and cooling rates.
Patents cover TCAM Technologies' heat transfer methods. Each actuator contains an electrically and thermally conductive carbon-fiber or silicon-carbide lattice impregnated with a thermally reactive polymer. The fiber lattice carries electricity and converts the electrical input to heat. Secondarily, it helps remove waste heat. Depending upon the application, this energy may be dissipated in a number of ways.
Hand tools
Robotics
External combustion engines
Engineers achieve the desired TCAM power and operating speed by appropriate selection of the polymer, core construction, spring preload setting, and heating and cooling speeds. Suitable polymers display a range of viscosities and exhibit bulk moduli (hydraulic stiffness) between 10,000 and 1,000,000 psi, depending on preload pressure. Their melting points range from -50 degrees F to 625 degrees F.
Proportionally controllable, TCAM actuators develop 200 to 500 times the force of a same-size solenoid. They allow nearly linear position control with accuracies to 0.001 inch. Their ability to produce 300% or more of their normal operating force-limited only by housing strength-makes them well-suited to systems that encounter high startup loads or stiction.
Over short distances, TCAM actuators can develop and maintain full-stroke pressures of 10,000 psi, and emergency pressures exceeding 30,000 psi. They require minimal supporting hardware and maintenance, and cost one tenth as much as comparable hydraulic systems.
For force control, a low-bulk-modulus polymer and a low load-pressure (10,000 psi) provide a constant-force source that remains fairly insensitive to position. This behavior resembles that of a hydraulic pressure-relief valve. For automatic control, a high-bulk-modulus polymer under high load (30,000 psi) exhibits a small position change under varying load. An actuator designed this way proves three times stiffer than conventional hydraulic systems.
A 1-inch-diameter, 2.5-inch-long TCAM prototype was created for the Air Force to replace the 20-Hz (50 msecond) hydraulic servovalve actuators that control F-16 flaperons. To date, a 175 msecond (5 Hz) rate is the fastest performance achieved by this 300W, 50-lb (200-lb emergency-force mode), 0.20-inch-travel prototype. Though cooling rate limits the device's operating speed, theory says a 50-msecond performance is possible.
Project manager Mike Sturdevant thinks TCAM technology can replace many, if not all, hydraulic systems on aircraft. "If we reach faster actuation speeds, then we can replace hydraulic servos," he says. More compellingly, he asserts that "since our current technology outperforms hydraulic end effectors-without the need for control servos, we can build an all-electric aircraft today." Such an aircraft would offer weight, cost, and performance advantages.
Meanwhile, Detroit may soon apply TCAM to wiper and window motors, and other applications. Since TCAM will work off low-temperature heat sources, vehicle radiator-fluid heat-normally wasted-can power many accessories.
Additional details...Contact Edward Schneider, TCAM Technologies, Inc., 33900 Curtis Blvd., Eastlake, OH 44095, (216) 942-2727.
About the Author(s)
You May Also Like