Strength in Plastics
June 16, 2003
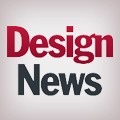
Not too long ago, "structural plastics" meant "metal replacement." And to some extent it still does. Today's applications, however, also involve the refinement of products that have already embraced plastics as a structural material. As engineers struggle to reduce manufacturing costs or improve performance of existing products, they increasingly ask themselves not just "should it be metal or plastic?" but also "should it be a different plastic?" And that last question has become more difficult to answer now that improvements in plastic design know-how and molding technology have made plastics suitable for more structural jobs than ever. The growing diversity of structural plastics applications recently took center stage at a design competition held by the Society of the Plastics Industry.
Part of the society's annual Structural Plastics Conference (www.plasticparts.org), the competition comprised entries from a diverse group of industries-including automotive, agricultural, computer, recreation, military, medical, and furniture. The 55 entries employed a variety of manufacturing methods with advanced variants of injection molding and reaction injection molded (RIM) urethanes as the most common manufacturing methods. Though very different, the applications together highlight the diversity of structural plastics-with a combination of first-time metal replacement jobs and enhancements of similar products that already use plastics.
Big trim panels
One of the most noticeable structural plastic jobs in the competition could be found on the Case IH AFX7010 Combine sitting in a parking lot outside the conference. Measuring 15-ft high x 32-ft long x 17-ft wide, the combine is covered in 12 exterior panels that took home the competition's Agriculture, Lawn & Garden Award. "We believe it's the first time such a large Class A surface has been enclosed with plastics from a single molding process," says Jeff Halpin, a combine development engineer for Case's CNH Crop Harvesting unit (Burr Ridge, IL).
|
Combine trim panels such as these have traditionally been metal. But with this project, Case's design team opted for plastics after going through a rigorous materials-selection process. It involved putting all the possible material choices and processes in a matrix and evaluating each with respect to a long list of design goals-including mechanical performance, total cost, styling, surface finish, manufacturing and perceived quality, serviceability, damage tolerance, and more. "In going from steel to plastic, there was a lot of second-guessing," Halpin says. But a soybean-based polyurethane RIM material from Bayer Corp. (www.bayer.com) ultimately emerged as the winner. Switching to RIM saved about 400 lbs of weight compared to a steel design, Halpin reports. And the use of plastics allowed Case to integrate features such as the mounting hardware and pockets for lighting that eliminate the need for mounting brackets.
Yet the choice of plastic wasn't clear from the get go. "SMC was a close contender," Halpin says. Its advantage came primarily in the stiffness department. As Halpin points out, SMC has a flexural modulus of roughly 1 million psi compared to about 240,000 psi for the RIM material. "That would have enabled us to design thinner panels," he says, noting that the material savings would have offset some weight advantage that RIM structural foam would have gained because of its low density.
But structural foam had some clear advantages over SMC. RIM offered a chance to get a Class A surface right out of the tool, thanks to the use of an in-mold coating system developed by the molder, GI Plastek (www.giplastek.com). "The in-mold coating process gave us a phenomenal depth of image and gloss," he says. RIM also offered a financial incentive, mostly through savings in tooling costs. According to Halpin, RIM's nickel shell tooling-single-cavity tools for the main side panels and two cavity family molds for the corner panels-cost about 50% less than comparable SMC tooling.
To cover such a big expanse with plastics, Case and a design consultant, Innovative Design Consulting of Elmhurst, IL, wisely performed extensive computer modeling of the panels. FEA work, for example, identified a need to add some stiffening frames behind the RIM panels. "We initially thought ribbing would do the trick," recalls Eric Jacobsthal, an engineer and principal at Innovative. But some load cases related to extremely high wind conditions-in excess of 50 mph-convinced the design team to add the stiffening frames. Solid models of early panel concepts, which were done in Pro/ENGINEER, flagged a potential problem with the doors opening properly. "For easy servicing, we wanted all the doors to open independently," Halpin points out. But with straight narrow split lines between adjacent panels, some of the early door designs would have opened if an adjacent door was pulled open first. Case avoided that problem in the finished combine with a clever design twist: they subtly curved some of the split lines to avoid any interference.
Better bumpers
In the automotive category, an injection-molded bumper assembly for VN heavy trucks from Volvo Truck North America (Greensboro, NC) took home top honors. Volvo has traditionally molded these bumpers in one piece-most recently from Metton polydicyclopentadiene (PDCPD). The new bumper, by contrast, is crafted from seven different parts, all of them injection molded from PC/ABS.
Three pieces joined primarily by a special snap-fit joint form the bumper's fascia, while four box structures adhesively bonded to the back of the fascia provide some structural reinforcement. Two metal brackets, which ultimately join the bumper to the truck chassis, bolt onto the back of the bumper assembly. The design also incorporates space and mounting points for fog lights and the antenna for the truck's collision avoidance system. Mack Molding Corp. (Inman, SC) optional molds and assembles the entire structure, using a robotic adhesive dispenser and custom-designed assembly fixture to bring all the parts together. The finished bumper measures 96 inches wide and ships as single part. All that assembly work might seem excessive, especially when past designs were based on a simple single molding. But the new bumper serves some important design goals. "It allowed us to do things we couldn't do with a one-piece design," says James Bird, the Volvo design engineer responsible for the new bumper.
|
Volvo's multi-piece design makes repairs a snap-literally. Bird explains that the bumper's snap-fit joints allow for the replacement of individual sections at a far lower cost than replacing an entire single-piece bumper. "No bumper will withstand an 80,000-lb truck hitting something substantial," he says. "So it was important we minimize the repair costs."
Another aspect of this patent-pending bumper design further limits collision damage by containing impact forces locally. "Each section isolates itself," Bird says. This isolation comes down to careful joint design. The snap-fits disengage upon reaching a certain impact threshold. "Hitting a small animal, for instance, wouldn't cause the joint to separate," Bird says. A moose would be another matter. Should a joint disengage in a collision, it would do so in a controlled manner. As Bird explains, each section is designed to deflect on an axis that keeps it from impinging on adjacent sections or other components-like the hood. Aside from the geometry of the joint itself, the location of the metal mounting brackets also play a role in controlling each section's bending axis, Bird adds.
Bird notes that the bumper serves an important aerodynamic function-which also has become more important than ever as truck makers try to boost fuel economy and offset the engine-efficiency losses associated with new federal emissions requirements. "The bumper sets up the air flow under the truck," he says.
Finally, the design supports Volvo's need for high-caliber cosmetics. The PC/ABS has a high enough HDT to make it through Volvo's painting process, Bird reports. And the use of adhesive bonding also helped protect the cosmetics. At one point, Bird considered molded-in structural features on the back of the fascia-such as ribs. But these would have shown up on the front of the bumper. "We were worried about rib read-through," Bird recalls. Adhesively bonded box structures proved to be a good alternative. They add vibration-fighting stiffness to the bumper without any visible trace on the show surfaces. And the box sections have the added benefits of protecting the fog lamps from tire spray and keeping snow, ice, and dirt from accumulating on the bumper.
Thick plastics go airborne
In a great example of how molding technology can open up new design possibilities, an injection-molded jet aircraft canopy developed for the Air Force's Lockheed F-16 won in the Military and Industrial category.
With polycarbonate walls in excess of 2-inches thick and a shot size of roughly 30 lbs, the canopy might not seem like a good candidate for injection molding. But EnviroTech Molded Products Inc. (www.empslc.com) has successfully molded the parts using its proprietary "bulk injection molding" process, which uses molding machines fitted with big accumulators and proprietary controls that can handle such thick parts. Forrest Day, the company's technology director, says the process can make parts even bigger than aircraft transparencies. Some production jobs have had shot sizes up to 400 lbs and wall thicknesses of 5 inches. Equally important, he adds, the process avoids the high molded-in stresses, voids, sinks, and dimensional instability that tend to plague thick-walled molded parts.
EnviroTech took on the canopy project for the Air Force Research and Development Group, which wanted to reduce the cost of the canopies. Day points out that the canopy manufacture currently involves the hand lay up of laminates within vacuum bags and autoclaves. But high costs, manufacturing times measured in weeks, and significant amounts of rejects and rework all drove the Air Force to look for an alternative manufacturing method. And replacing all those steps with injection molding promises to save more than $1 billion over the life of the project, according to an estimate Day gave during the conference.
The molded parts aren't all about the money. The molded canopies have to meet stringent-and confidential-functional requirements. These include light transmission, optical clarity, and impact resistance. The design also had to attach to the aircraft without a metal frame-an important detail for stealth models.
Though the competition featured a developmental transparency produced for the F-16, EnviroTech and the Air Force have other models slated to go into production over the next couple of years. First up is a canopy for the T-38 trainer, followed by a model for the F/A 22. Another canopy for the Joint Strike Fighter is in development.
Senior Editor Joe Ogando can be reached at[email protected].
About the Author(s)
You May Also Like