Servos key to managing multiple motions
May 7, 2001
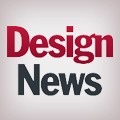
St. Louis -Stacking boxes on pallets might sound like it's a relatively straightforward job. But the multiple-axis gantry robots designed to do this task must operate with extreme precision and travel through fairly complex pick-and-place motion profiles.
"Picking two, three, or four boxes at a time and building a particular load pattern requires a lot of different coordinates," says Tim Simone, engineering manager of Robotic Products for Alvey Systems. "When you consider additional build stations and conveyor infeeds, the number of possible positions grows exponentially."
A recent switch to servo systems coupled with planetary gearboxes and computer control allows Alvey's #520 gantry robotic palletizer to handle the job efficiently. Three servo motors (Rexroth Indramat; Hoffman Estates, IL) power the X (gantry), Y (bridge), and Z (mast) axes. All three motors are controlled by one 4-axis controller card (Motion Engineering Inc. (MEI); Santa Barbara, CA).
Three servo motors power the X (gantry), Y (bridge), and Z (mast) axes of Alvey's robotic palletizer, which performs complex pick-and-place motions at multiple pallet stations. All three motors are controlled by one 4-axis controller card. |
Motion profiles differ depending on customer needs. In a typical palletizing operation, all three components of motion-velocity, acceleration, and position-are used to control the load. Velocity and acceleration are maximized to transfer the load safely and quickly. Position control ensures the robot accurately places each box on the pallet. Maximum positional error throughout the entire travel of each axis is plus or minus 1/16 inch, due mostly to the tolerances in the gear reducers and the rack-and-pinion systems.
A customer request for a longer bridge drove engineers to rethink the design of the robot's 3-axis gantry. The typical length of such a bridge, which is driven up and down the gantry via a single servo motor and worm drive, is 15 ft. Drive shafts connected to the worm drive extend the length of the bridge and connect to a rack-and-pinion system. Due to the worm drive limitations, motor input speed maxed out at 2,000 rpm, yielding a maximum bridge speed of 50 inches/sec and acceleration of 50 inches/sec 2.
The customer's requirements for a 20-ft-long bridge raised concerns about longer and heavier drive shafts, the need for additional bearing supports, gearing efficiency, and drive wind-up. Engineers replaced the single motor/drive shaft system with two servo motors and planetary gearboxes, one pair at each end of the bridge, linked in parallel by the motion control card to directly drive the rack-and-pinion system. This scheme allows for motor speeds of up to 4,000 rpm with bridge speeds of 90 inches/sec and accelerations of 85 inches/sec 2. "Eliminating the drive shafts gave us fewer parts and a more responsive axis, especially since the bridges can be 20 ft long," says Simone.
For more information
Go to www.designnews.com/info or enter the number on the Reader Service Card:
Servo motors from Rexroth Indramat: Enter 550
Gearboxes from Alpha Gear Drives: Enter 551
Motion controller from MEI: Enter 552
Alveys 520 gantry robotic palletizer at-a-glance | ||||
---|---|---|---|---|
Axis | Payload (lbs) | Travel (ft) | Speed (inches/sec) | Acceleration (inches/sec 2) |
X (gantry) | 300 | 100 | 90 | 85 |
X (gantry) | 1,000 | 100 | 90 | 60 |
Y (bridge) | 300 | 13,15,20 | 85 | 90 |
Y (bridge) | 1,000 | 13,15,20 | 85 | 50 |
Z (mast) | 300 | 100 inches | 60 | 90 |
Z (mast) | 1,000 | 90 inches | 60 | 50 |
About the Author(s)
You May Also Like