Robotics Make a Move Toward Autonomous Service
June 30, 2010
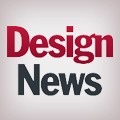
With costs coming down for sensor-based technologies,vision and tactile feedback robotic systems are becoming increasingly moreintelligent, people-aware, and are converging on a new paradigm and set ofrobotic applications.
This new direction is focused around three advances: proficiencywithout extensive software coding at the outset of an implementation, theability for robots to work side-by-side with humans, and concepts like cloudcomputing that have the potential to help create more sophisticated learningmachines.
Some developments are still futuristic, but already more and morerobots are finding their way into warehousing, order fulfillment, health careapplications, and may find a place in the future as "autonomous service robots"in automotive assembly plants.
Learning Trend
"We conducted a survey within the packaging industry, andthe results came back very strongly that users of robotic automation are justtired of programming," says Rush LaSelle, vice president of sales and marketingfor Adept Technology Inc. "It's probably the number one dissatisfaction inimplementing robotics. Users want more intuitive, easy-to-deploy technology."
LaSelle says that this trend, along with reduced costs and higherfunctionality with sensory perception-based technologies, is a very strongdriver in the cloud computing thought process. The idea is to create learningmachines that can essentially take algorithms and become more adept andproficient without a lot of extensive coding at the outset of animplementation.
"The value proposition for robots moving forward is the abilityto search, validate and truly become the last mile for intelligent decisionmaking," says LaSelle. "In the same waya surgeon's assistant is tasked with giving precisely the right instrument whenthe doctor needs it, the learning element is all about optimizing the processto predict what a surgeon might need next."
He says that, after the incision, for example, the surgeon mayneed a clamp - and we all know that computers are much better and accurate atprocessing both that type of information and large amounts of data. The abilityto learn, predict and accurately provide a surgeon with the right instrument isvery much data-driven. "So the last mile is taking what's known, anticipatedand expected, and converting it into accurate physical activity," LaSelle says.
Service Robots for Automotive Assembly
General Motors, the largest user of robots in the world,with a fleet of 25,000 robots used in factories around the world, is alsostepping up its robotic investigations with a specific long-term target:assembly operations where future robotic solutions will assist people inbuilding better and safer cars.
"We have been observing robotic advancements in Japan andEuropean countries for years, and believe a new field and era in robotics isemerging for what we call service robots," says Dr. Roland Menassa, GM'sadvanced robotics manager in the Manufacturing Systems Research Lab.
The focus at GM is on developing humanoid, two-arm-type robots,which is behind a current five-year collaborative agreement with NASA's JohnsonSpace Center that began in 2007. In April, NASA announced it will launch thefirst human-like robot into space later this year. It will become a permanentresident of the International Space Station. Robonaut 2, or R2, was developedjointly by NASA and General Motors under their cooperative agreement to developa robotic assistant that can work alongside humans, whether they are astronautsin space or workers at GM manufacturing plants on Earth.
The 300-lb R2 consists of a head and a torso with two arms andtwo hands. R2 will launch on Space Shuttle Discovery as part of the STS-133mission planned for September.
"We don't have a finished product at this point, and I don't wantpeople to have the misconception that GM will put humanoid robots into theplants tomorrow. That is not the case," says Menassa. "The technology willcontinue to evolve but along this journey we stand to benefit from the spin-offtechnologies that have been developed for eventual use in other facets of themanufacturing process."
From the GM perspective, walking robots are not attractive in amanufacturing setting, so the focus has been on the upper torso, the dexterityof the hands and degrees of freedom to do real work. There has to be a level ofintelligence so that you can interact with the robot in a human, intuitiveway. And the development needs to drivea new set of safety technologies which GM intends to deploy in othertraditional areas.
"Our position is that the technological advancements achievedwith the collaboration between GM and NASA will enable us to offer customerssafer vehicles and build them in a safer way," Menassa says. "If you look atthe control and sensor advancements that we are developing with this robot, itcan help us drive the development of future vehicles and safety systems, aswell."
Over the very long-term future, measured in decades, the goal isto have a robot that can use the same tools that humans can. And unliketraditional robotics where there's a need to spend 3x to 10x, depending on theapplication, to enable the robot in the process, this new technology does notneed traditional support equipment such as fencing, light screens and safetymats.
"From an assembly perspective, we think these robots can enable aflexibility solution that we cannot provide today," says Menassa. "And at theend of the day, GM uses robotics or any automated solution to enable theprocess. Process is what drives everything."
Autonomous RoboticWorkcells for Surgical Instruments
Robotic Systems & Technology is bringing contemporaryautomation and robotics into an area of the hospital system called sterilesupply with the development of autonomous, robotic workcells to manipulate,track and process surgical instruments and supplies.
RST's latest product, PenelopeCS, is intended to revolutionizethe way hospitals manage inventory of surgical instruments. PenelopeCSautomates key functions in the hospital's sterile supply department whereused/dirty surgical instruments are cleaned, sorted, inspected and repackedinto containers to be sterilized for the next procedure.
"We are introducing a very smart robot - a real robot with eyesand a brain into the workplace," says Dr. Michael Treat, a surgeon and founderand leader of Robotic Systems & Technology Inc. "This represents a newtrend in robotics and a new approach for medical applications. There are robotsin the operating room but those are teleoperated devices and basically serve assophisticated power steering for the surgeon."
Treat says the expertise developed over the last six years hascentered on designing machine vision routines for surgical instruments and theintelligence built into its software to recognize and organize the instruments.But the challenge is both technical and organizational, configuring the machineand software to fit nicely into the existing process. "It's an interactivemanufacturing process, and really a new kind of robotics in the sense that it'smore involved with people than assembly line robots," says Treat. "PenelopeCShas a brain which is focused and limited, but there is independence andindependent activity that the software in the rule base generates. The goal isto advance both robotics and hospital efficiency using a man-machinepartnership."
Intelligent, Mobile Robotic Control
From individual robots in hospitals to fleets of AGVs infactories and warehouses, automation solution providers are increasinglyrelying on autonomous mobile robots to handle navigation, positioning, taskingand configuration.
Mobile Robots Inc. has been manufacturing automated guidedvehicles for 15 years, and has thousands of robots installed around the world.The company is a tool and component supplier, not a maker of end-user solutionsand they supply design engineers with a base autonomous robot.
"Our robots are designed to do the most sophisticated, autonomousbehaviors, navigation and localization without having a roboticist orprogrammer involved," says Jeanne Dietsch, CEO for Mobile Robots Inc. "They aredesigned for engineers to add onto and integrate into warehouse managementsystems, external scheduling and inventory control systems."
The company's Motivity technology is centralized aroundautonomous navigation and localization but it is more than that. It usesnatural, feature-based autonomous navigation and localization which eliminatethe need to install lines or beacons used with other AGV solutions. Softwaretools for setup and installation of the robot, along with networking andinterfacing tools plus a real-time control GUI, reportedly make it easy for theinstaller to use ready-made robot behaviors and responses. "An engineer cancreate a system by dragging and dropping objects that would take months for aprogrammer to create," says Dietsch.
MobileEyes software tools provides a way to set up, implement andmonitor robots, and serves as a monitoring station or command and controlstation for users, if desired. Mobile Planner enables customization of aproject, so application designers can create missions, tasks, behaviors andpersonalities appropriate for their specific workplace, whether it's an industrial plant or a hospital patient's room.
The robots learn to recognize their location in a facility basedon natural features; for example, learning the facility layout by looking atwalls, parts of the factory or the ceiling in a dynamic space like a warehouse.Because they don't require beacons or lines in the floor, it reduces theupfront cost of the system. With older AGV systems, before you put in the firstAGV, there is normally a huge infrastructure investment and it isn't somethingan engineer can try out in a facility beforehand to see how well it works.
Dietsch says that one example of where Motivity systems haveproven very useful is an intractable problem for tire factories. In the tiremanufacturing process, a manual process is typically used to carry tires fromthe gantry where they are stored and cured for about two weeks to the presswhere they are cooked. This process of carrying the tires had been donemanually using carts because of the distance from the gantries to the presses.Though there are many forklift trucks and people moving within the facility,robots deployed to handle this task have been able to deal with the traffic andhave driven millions of miles per year safely.
In the largest installation for Motivity, there are 38 robotsrunning simultaneously, and the system made a 25-percent throughput improvementover the manual system. The robots are now waiting for the presses to clear,rather than vice versa, and five global tire manufacturers are deploying thesesystems.
The advantage of Motivity is that it enables flexible automation,and users no longer have a robot that can only go from point A to point B.Instead, the robot can move from A1, A2, A3, A4, A5 and A6 to B1, B2, B3 and B4in any sequence. Locations can be randomized, unknown or dynamically guided.
"Instead of going onto a cart where it is distributed by someone to various locations where it is actually beingused, the material goes onto a robot, and the robot can take it the last mile.The first mile and the last mile are always the most difficult in any deliverysituation, and our robot is excellent in those applications."
About the Author(s)
You May Also Like