The Raven: Another Blackbird for the record books
September 11, 1995
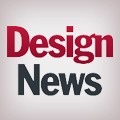
Paul Illian believes that man's fascination with human-powered flight lies at a deep, subconscious level, possibly something that's encoded in our DNA. And the evidence leans in his favor.
Leonardo Da Vinci sketched drawings of human-powered ornithopters 500 years ago; Greece's mythical Icarus soared near the sun a millennium before that; and nightly, untold millions of sleepers spread their arms and fly free in their dreams.
But Illian, chief engineer of the Raven human-powered airplane, is one of the few who have attempted to translate that dream into reality. Should all go as planned, Raven and its human motor/pilot will fly non-stop 100 miles from Boundary Bay, BC, to Seattle, WA, setting international distance and duration records in the process. Numerous pioneering design efforts went to the project, including material and construction techniques, and the first use of a complete fly-by-wire control system and autopilot.
Between today and Boundary Bay lie hundreds of engineering and flight-test hours. Raven's first flight, scheduled for mid-1996, will use a larger-than-necessary, 350-sq-ft wing. A series of flight tests in the Mojave Desert will follow, enabling engineers to gather drag and performance data to calculate the area of the wing to be used in the 100-mile flight (estimated at 210 sq-ft). Two records--those for female distance and duration--may be set with the large wing. However, in 1997, with the new wing attached and a stable of half a dozen trained pilots "peaking" at weekly intervals, the record attempt will begin.
The project teams about 200 industry professionals, 11 undergraduate institutions, and 11 professional societies. Groups of four to five engineers and 15 to 20 students concentrate their efforts on one of 19 different tasks ranging from technical issues like fuselage, wing, or tail design, to operational functions like weather research or flight tests.
Groundbreaking design. Comparisons to past human-powered aircraft seem inevitable. The current record holder, Daedalus, flew 71.52 miles across the Aegean Sea in 1988. This roughly doubled the record of the Michelob Light Eagle set in 1987, and more than tripled that of Paul MacReady's Gossamer Albatross, which hopped 22.3 miles across the English Channel in 1979.
Illian began penning Raven's design the year Daedalus flew. He chose, arbitrarily, a 100-mile goal. And to stay within the limits of his 0.25-hp engine, he imagined a five-hour flight requiring 20 mph. These figures--distance, speed, and power--drove the entire design. It also presented engineering problems whose solutions make Raven a very different bird from its ancestors.
Raven flies one-third faster than Daedalus and twice as fast as the Gossamer Albatross. Thus drag, a function of velocity squared, must be cut significantly. "We need just 4.22 lbs of drag at 20 mph," says Illian. "Daedalus had about 6 lbs of drag at 15 mph."
In addition, available thrust is a function of power divided by velocity. With the power held constant, if velocity increases, thrust decreases. Raven would therefore not only have to fly faster than Daedalus, it would have to do so with less thrust.
Lastly, using an estimated takeoff weight of 245 lbs, Illian computed a lift-to-drag ratio (L/D) of 58 to 1, a figure very close to that of a high-performance sailplane and 50% greater than Daedalus. "This showed us where to concentrate our efforts," he says. "With a L/D of about 60, drag is about 60 times more important than weight."
Illian tackled the problem by eliminating things that hang out in the wind, reducing wetted area, and paying extremely close attention to interference drag. First to go was wire bracing. Though seemingly too thin to be important, "a wire's drag is a function of the arc it vibrates through," he says, "not its diameter."
To reduce interference drag, Illian researched 509 NACA fuselage-wing intersection studies from the 1930's and found that a blended wing/fuselage was the best performer. Mounting the propeller directly to the fuselage, and the elevator and rudder to the tail boom further reduced the number of drag-producing intersections. To prove the design, he built a wind-tunnel model and ran CFD analysis using V.S. Aero from Analytical Methods of Redmond, WA.
Featherweight construction. Drag might be Raven's biggest foe, but the aircraft is no heavyweight. Sans pilot, it tips the scales at 75 lbs, allotting 12 lbs for the 3-m-long by 1-m-diameter fuselage, 45 lbs for the 115-ft-long wings, and just 1.5 lbs for the 9.5-ft-diameter propeller. Initially too progressive in its design, Raven had to wait until the 1990's for technology to catch up. "We were within 10% of existing materials and electronics," says Illian. "It wasn't producible at the time."
Construction for the wing, fuselage, and tail structure deviates from the traditional Mylar-covered framing. "Mylar scallops between the ribs," Illian explains, "and we need a smoother, more aerodynamic surface." Engineers chose instead to sandwich 0.10-inch-thick polystyrene foam between skins of ASM Carbon Nonwoven mat. Produced by International Paper New York, the carbon weighs just 0.2 oz per square yard. "The hardest thing is to convince yourself is that you can make something this light and it will hold together and fly," says Troy Van, a student on the wing team.
Spaning 115 ft-- 11 feet more than a Boeing 737's--the wing borrows the airfoil design created by Mark Drela for Daedalus. It consists of two roughly 60-ft halves laid up in molds built by students at Western Washington University in conjunction with Pocock Racing Shells of Everett, WA. To save weight, complexity, and drag, no ailerons clutter the Raven's trailing edge. Instead, it relies on natural dihedral for stability.
The wing blends smoothly into the egg-shaped fuselage. Inside, Raven's 140-lb recumbent argonaut pedals a CNC-machined hollow aluminum crankset from Precision Technology, Woodinville, WA, at 90 rpm. The crank drives a 2-ft-long, 1-oz carbon-fiber propeller shaft via a set of straight-cut bevel gears.
Out front, the two-bladed propeller turns at 135 rpm. It's controlled by a microprocessor-driven variable pitch mechanism housed in the hub. "The blades are balanced so that there is no torque on the spar when flying at the design condition," says Illian. "If they are off, the microcomputer reads the torque and zeros it."
As with all of Raven's geometry, the propeller was first defined in AutoCAD. Students at Renton Technical College converted the CAD data to CNC toolpaths, and carved molds from high-density foam donated by General Plastics of Tacoma, WA.
During his continual quest for reduced drag, Illian focused his attention on a seemingly insignificant detail of fuselage design: the pilot cooling system. In the past, designers simply cut small holes in front and back of the fuselage. On Raven, such impromptu surgery would add a small but intolerable amount of drag.
"Ours works like a very-low-temperature, low-efficiency ramjet," Illian explains. A pair of inlets at the propeller hub draw in air and pass it through a diffuser to slow it. The upper inlet directs flow over the wind screen, while the lower one cools the pilot's legs. Air exits through a convergent nozzle at the rear of the fuselage that uses an inflatable, pilot-controlled, variable-geometry plug to vary the flow.
Brain in the tail. Raven will be the first human-powered aircraft to fly its record run with an all-electronic control system. Not simply an engineering exercise for students, "the autopilot is one of the keys to Raven's success," says Illian. "With cables, friction and aeroelasticity would give us 40 to 50% control-system hysteresis."
The system's design falls to Roger Johnson, who by day is manager of electro-optics and motion control at Quest Integrated, Kent, WA. He developed a "stegosaurus" concept in which the control system's brain, a Motorola 68332 microcontroller, resides in Raven's tail. It receives sensor and command inputs via two fiber-optic cables running inside the 20-ft-long, carbon-fiber tail boom that provide full RS-232 communication.
To conserve battery power, the microcontroller outputs commands just five times a second. The commands direct a pair of "top-band" elevator and rudder drive systems powered by standard model-airplane servos.
Each servo drives a capstan wrapped once with dual (for redundancy) stainless-steel cables. The cable-ends attach to a torque arm that acts as a yoke to rotate the elevator or rudder shaft. "I got the idea for a top-band drive from computer hard disks," says Johnson. "They use this type of mechanism to position the read/write heads."
The control system gathers data, such as altitude, heading, turn-rate, and airspeed, from a set of sensors. Since Raven flies so low (20 ft), Johnson chose to measure altitude with an ultrasonic transducer from Cambridge, MA-based Polaroid that bounces sound waves off the surface of the water. A barometric sensor from SenSym of Milpitas, CA, serves as a backup altimeter, while another SenSym product, a silicon strain-gauge, measures airspeed.
Heading information comes from a magnetometer built by Precision Navigation of Mountain View, CA, while a rotary, inertial Gyrochip from Systron Donner of Concord, CA, measures Raven's turn rate. Johnson's team is still developing a way to measure angle-of-attack, since no off-the-shelf product does the job.
Sensors that output a digital signal are converted to analog using small "PIC" CMOS processors provided by Microchip Technology of Chandler, AZ. The sensors are programmed with a software package from Parallax of Rocklin, CA. Johnson finds the combination extremely flexible, powerful and easy for even the students to use.
The pilot directs Raven rather than steers it. Commands are punched on a small keypad and processed by a two-axis autopilot. Preprogrammed takeoff, landing, and cruise modes off-load the aircraft's tricky handling characteristics to the control system, allowing the pilot to concentrate on pedaling. A four-line by 20-character LCD screen displays critical flight data. In emergencies, a small joystick lets the pilot manually steer Raven to safety.
About the Author(s)
You May Also Like