Pre-Integrated Sensors Cut Costs & Design Risk
January 14, 2014
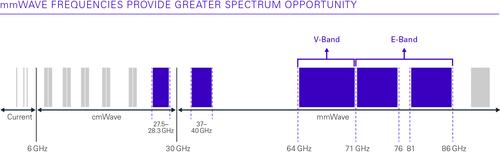
Designing the sensor elements of monitoring or control systems which require accurate, reliable, real-world inputs can be one of the most challenging parts of the product development cycle. It's no wonder then, why many designers now opt to purchase either off-the-shelf or custom pre-integrated sensor modules.
Offloading most of the design, test, and manufacture of sensing elements to a third-party vendor can help make the most of an engineering team's limited resources while shortening a product's time-to-market. Nevertheless, there are still many critical decisions a designer must make which have a major impact on their products' performance, reliability, and cost.
To help design the optimal system, let's look at pre-integrated sensor elements -- specifically the advantages they offer -- and familiarize you with some of the key issues you must consider to create a solution which best meets your application's requirements. Even an experienced engineer may find that designing the sensor elements which provide accurate, reliable data about the real-world conditions within HVAC systems, medical devices, process control, or other factory automation equipment can be one of the most time-consuming and expensive parts of a product development cycle. This is in large part because sensor design is an interdisciplinary process, which requires a design team to consider myriad electrical, mechanical, and manufacturability issues.
Once you've identified the sensor element(s) best suited to your application, you must decide how to integrate it with the rest of the system. This process includes pairing the sensor with the right combination of signal-conditioning circuitry, termination, and interface connector. Next, it's time to decide whether there's a standard off-the-shelf package that can house the resulting assembly or if your application's space and environmental requirements are best met with custom-fit packaging. A custom package may even integrate one or more sensors and other elements to create a next-higher assembly, such as a pressure sensor with an integrated manifold for use in blood analyzers and ventilators.
Remember, too, that as the sensor design evolves, so must its test plan. Your design must include the procedures needed to verify that the final assembly will operate accurately and reliably when it's integrated with its host system.
The case for an integrated sensor
Pre-integrated sensor solutions are becoming a popular and increasingly cost-effective alternative to the traditional sensor selection and integration process. In many cases, careful selection of a single known-good package, which may include the sensor (or multiple sensors), signal conditioning elements, and other critical components, can help accelerate a product's development schedule while reducing its design, manufacturing, and test costs. This can also help manufacturers shorten the certification testing schedules because once an integrated solution is certified to comply with an industrial or medical standard; developers who use it in their design don't have to recertify their upgraded products (figure1).
In most cases, any cost differential between pre-integrated/pre-tested sensor assemblies and discrete components is repaid several times over with lower unit production cost and reduced testing costs. Using pre-integrated sensor solutions also eliminates the overhead associated with maintaining and tracking the many discrete components a manufacturer would have to stock for a traditional solution.
Care should be taken however, to ensure that your sensor assembly fully meets the application's requirements in terms of performance, operating environment, testing, and reliability. Likewise, make sure the packaging options offered by a sensor vendor are well suited for the intended application.
Another less obvious consideration is the level of design support provided by the sensor vendor. In today's lean corporate culture, most companies tend to concentrate their limited engineering resources on the elements of their products which serve as market differentiators and rely on reference designs or canned solutions for the system elements which support them.
As a result, you'll likely need to consider how much assistance your engineering team will require to fully define your application's requirements, identify potential solutions, and objectively analyze which approach best meets them. In some cases, value-added assemblies can become a key part of your system's differentiation and should be considered early in your design strategy.
All integrated sensor manufacturers offer some level of design support. This can range from occasional online chats or exchanging email with a randomly assigned apps engineer to a full-blown design team which "embeds" itself with your engineering group for the duration of the design.
Since pre-integrated sensor solutions address issues that affect design, manufacturing, and marketing operations it can be tough to get a complete picture of benefits they offer. One of the best ways to get a better sense of this is by looking at a real-world example.
One recent success story began when a manufacturer approached Honeywell's design team to see if it could help them reduce the cost of the valve position-sensing element they used in their airflow control products. The valve could be actuated and monitored with standard programmable logic control (PLC) signals commonly used in factory and building automation systems. The customer wasn't satisfied with the traditional position-sensing technologies they were using (e.g., Hall-effect sensors and magneto-resistive arrays) which were relatively expensive to implement and required frequent calibration. Since the applications their equipment were used in didn't need the incremental position data produced by conventional sensors, they wondered if there was a less costly way to reliably produce the simple open/close/fault indicator signals they needed.
Working closely with the customer's designers, Honeywell's Value-Added team developed a reliable, lower-cost alternative based on its TruStability board-mount pressure sensor. In addition to a lower total solution cost than the sensing elements in their previous designs, the sensor offers lower lifetime costs for both the manufacturer and its customers. This is primarily due to its rugged construction and robust components, which produce the low-drift characteristics, which help them maintain accuracy throughout their service life. As a result, the end systems can be shipped as pre-calibrated units, which eliminate the need for the costly initial set-up and periodic recalibration required by many conventional sensing technologies.
Related posts:
- Valerie Rothermel is a senior global product marketing manager at Honeywell.
About the Author(s)
You May Also Like