Nutating-sleeve valve simplifies aseptic operations
March 6, 1995
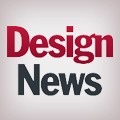
Portsmouth, NH--Imagine the hip action of a hula hoopist and you've got the notion behind the Rotosleev(TM) valve. An eccentric, cylindrical cam within a fixed, flexible sleeve rotates to deflect the midsection of the sleeve toward or away from the valve's inlet port. The design brings a host of benefits to industrial flow-control problems.
The valve was originally built to solve growing pains among biotechnology companies. Diaphragm valves, adequate for small-scale systems, experience unacceptable cavitation, excessive actuation forces, and maintenance problems when asked to control flow through six-inch pipes.
Hans Baumann brought 40 years of experience in specialty-valve design to bear upon these problems. Based on his modified-globe-valve Flexsleev(TM) design, the valve took three years to develop, time largely spent in refining its flow path and finding the proper sleeve construction for long life.
That smooth flow path around the cylindrical sleeve gives the valve a pressure-recovery coefficient of 0.87. The small pressure gradient across the valve greatly reduces cavitation compared to diaphragm valves of similar size. In bio-technology applications, it also reduces fluid shear forces, resulting in minimal damage to cells passing through.
As a throttling valve, the design's flow rate varies nearly linearly with actuator rotation angle, simplifying process automation. Its resilient sleeve, backed by the steel cam, closes tightly, conforming with ANSI/FCI 70-2, Class VI leakage standards. And, because its rotating elements stand completely isolated by the fixed sleeve, the design virtually eliminates stem
Other Applications |
|
leakage. "It's the world's first packless rotary valve," explains Baumann.
Rotosleev's smooth-walled interior drains completely no matter how it's oriented. The valves remain unaffected by 35-psi live-steam sterilization. Compared to diaphragm valves, they require 28 to 35% less actuator force to operate.
Variations on the original design include a three-way valve, an on-off valve driven by a steel ball riding on a face-machined stem, and a live-loaded version for zero leakage in high-pressure applications.
Additional details...Contact Hans Baumann, H.D. Baumann Associates, Ltd., 35 Mirona Rd., Portsmouth, NH 03801, (603) 436-2044.
About the Author(s)
You May Also Like