New Technology for Variable Speed Pumps Reduces Energy Usage
October 18, 2010
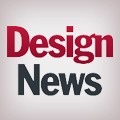
Keydrivers for fixed displacement or dual displacement pump systems are energyefficiency and the need for new hydraulic motion control concepts in marketswhere energy usage plays a vital role. These pump systems use tight integrationwith a drive and an electric motor to achieve intelligent operation and reducedenergy consumption.
"The energy efficiency of the system ishigher, especially when the system is working under partial load," says DaveGeiger, hydraulic systems engineering manager for the Moog Industrial Group."Under full load conditions, the performance compared to the variabledisplacement system is nearly identical. With a medium load, the efficiency ofthe new system is 20 to 30 percent higher compared to the classic system. Ifyou are running without load, or in a standby mode, energy consumption is evenup to 90 percent less."
The classic system for variabledisplacement pumps consists of a pump and an induction motor, which is directlyconnected to the power grid. In this typical system, the motor runs at aconstant speed, normally at 1,500 to 1,800 rpm, and uses an internal mechanismto change the output flow of the pump.
The new system consists of integratedbuilding block products from Moog including a fixed displacement Radial PistonPump (RKP-II), the Maximum Dynamic Brushless Servo Motor and the ModularMulti-Axis Programmable Motion Control Servodrive (MSD). Users can change thespeed of the motor and pump, which enables control of the fluid flow.
Two contributing factors lead to ahigher overall efficiency of the whole system. The heart of the innovation iscentered on the drive because of its control algorithms but also on the use of high-efficiency,low-leakage technology. The MSD drive provides pressure and flow functionalityand, depending on pressure and flow demand values, the drive decides whattorque and speed settings are required.
From the pump and motor side, pump and motorcharacteristics are measured at the factory and saved in the drive, so thesystem has critical information about the attached motor and pump. This createsa more intelligent system, which is integrated on the drive side and has theability to communicate via fieldbus to external systems.
New Technology for Variable Speed Pumps Reduces Energy Usage_A |
Further improving measure is a dual displacementpump design, which provides the ability to change between two displacements. Inthis case, the controller takes into account the actual displacement. This issimilar to a gear shift on a bicycle, and is especially important if the applicationhas a load holding phase. In that situation, the application normally needs lowflow, but also high pressure. The dual displacement pump changes to the lowdisplacement, reducing the required motor torque.
Depending on the operating conditions, thepump intelligently switches from one displacement to the other. This switchoveris controlled by the drive and the algorithm.
With a dual displacement pump design, it'spossible to switch to the smaller displacement, which requires a reduced torque.And as a result, the motor size required for the system can be reduced. Thisleads to energy savings during the application's holding phase due to moreefficient operation of the motor.
Besides energy savings, thetechnology offers additional advantages including a more compact design and mucheasier system integration. The design achieves more compactness primarily becausethe synchronous motor is much smaller than the corresponding induction motor.
With older systems, any fieldbusused in a system would be interfaced through the pump control because it islinked to the automation system. But now the fieldbus is through the driveelectronics, which is identical to an electromechanical axis.
The new system is easier to integrate,because it looks like an electromechanical system. Since their interface is thedrive electronics (MSD drive), the interface is absolutely identical to anelectromechanical axis and the interface is more or less the same whether theyuse the electrohydraulic or an electromechanical system. Integration is muchmore straightforward and the system achieves a smaller footprint.
This variable speed pump system is targetedfor applications using variable displacement pumps today. These pumps changeflow using an internal mechanism but now the new technology can replace thatapproach for use in applications such as die casting, injection molding andwrapping or bending machines. Whenever the focus of the application is onenergy savings, compact design or easier integration, this recently adopted technologyprovides an effective solution.
When comparing the cost of Moog's system witha system that uses a variable displacement pump and a constant-speed inductionmotor, the initial cost will be higher. But calculations and experience showthat the total cost of ownership will be lower. And, typically after two years,energy savings has paid back the higher initial investment.
With mixed technology systems, whether you useelectromechanical or electrohydraulic systems, what matters in the end is theimpact and benefit of the technology on the application. With the Moog variablespeed pump system, the human machine interface is the same regardless of thetechnology and topics like energy savings and safety that are driving the useof the technology. The system has the ability to combine the best of bothelectrohydraulic and electromechanical technology, to create the best solutionfor a specific project.
The technology was actuallydeveloped several years ago, but now adoption is dramatically increasing withChinese and German builders of plastics and injection molding machines lookingcarefully at total cost of ownership as design criteria.
New Technology for Variable Speed Pumps Reduces Energy Usage_B |
"The keys are upfront costs and what it coststo operate and maintain the machine," says Geiger. "The cost of ownership forelectric systems was higher than expected because the initial purchase price ishigher. But upkeep is also more expensive because on an injection moldingmachine, for example, the electromechanical devices are built into theframework of the machinery. It's not like an actuator that can be easily boltedin and later removed because it is integral to the machine."
Geiger says that every few years,when an electric machine is rebuilt, it has to be totally disassembled andre-assembled. The variable speed pump technology is attractive because theenergy consumption is not far away from electric and, while the performance isa little lower, in most applications the higher level of performance from arepeatability view point is not needed.
The value of the variable speedpumps is the 20 to 30 percent energy savings versus variable displacementtechnology, plus the ability to changeover machines without moving to acompletely electric solution. With a view of long-term cost of ownership, thecost of building the machine is very inexpensive and similar to a hydraulicmachine. Plus, the process of rebuilding in the future is much lower becauseyou can disassemble the actuators, put in new seal packages, replace some hosefittings and replace the pump cartridge.
Geiger says the key to higheradoption is the overall value of the variable speed pump. When there is arequirement for high performance and, in particular, high repeatability machines,OEMs move to an electric solution. And for high-speed machines, users typicallymove to servo valve hydraulics. Those are the areas where the variable speedpump technology is not a fit, but it does fit in 90 percent of applications.
About the Author(s)
You May Also Like