Machine Vision Using Ethernet Powerlink
May 30, 2013
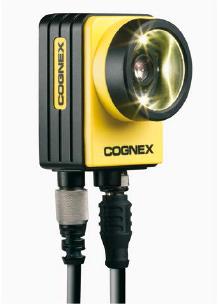
New connectivity between vision systems and automation solutions based on Ethernet Powerlink communications is creating simplified system architectures that enable higher performance application possibilities.
According to B&R Automation, the In-Sight 7000 series from Cognex is the first vision system with built-in support for the Powerlink protocol. This means users no longer need a parallel network for image processing, and can instead communicate process and image data using a single medium. It also offers an integrated solution that unites vision, control, I/O, and motion for process automation and quality control.
"The big benefit for applications, compared to a traditional camera system and control system, is that typically the camera system is communicating with a PC, which then communicates with the control," Stephan Stricker, product manager at B&R Industrial Automation, told Design News.
He said that in high-speed applications, often the only option is to hard-wire a connection to the camera and then trigger the camera to take a picture. In these applications, because the interface is so limited, there isn't information available from the camera, and the resulting speed of operation is not very fast.
Cognex implemented the Powerlink interface using Ethernet communications to connect cameras along with I/O and drives on a real-time network, which enables the control system to exchange almost any kind of information with the camera. This includes triggering the camera but also gathering detailed information about an inspection process. If a user wants to read a 2D barcode, for example, there is a variety of information available beyond the string that is read, including the time needed to identify the barcode and orientation of the barcode on the product.
"This information can be mapped from the camera directly into the PLC, with a goal of speeding up application performance using faster communications with the camera," Stricker told us. "More information is available, and it is easier to retrieve this information without the PC in the middle. With the PC, there was a need to coordinate the communications from the PC to the camera, and then from the PC to the PLC. One goal is to eliminate the PC, and be able to use a control panel for machine control along with managing the vision system."
Cognex also implemented TCP/IP over Powerlink, which provides non-real-time communications, as well as managing cyclical communications. This is especially useful when changing the configuration of the camera is needed, which has typically required a PC. But since jobs are stored in the camera, the PC is actually not needed for the inspection process.
Stricker said there are often a series of steps in an inspection process, and Cognex provides user software tools for configuring these operations. To connect to the camera and change a job, the PLC controller can now route through the network to the camera to achieve a non-real-time communications link, which, in the past, usually would have interfered with operation of the real-time network.
About the Author(s)
You May Also Like