A Look at Specialty Coatings for Bearings
September 5, 2014
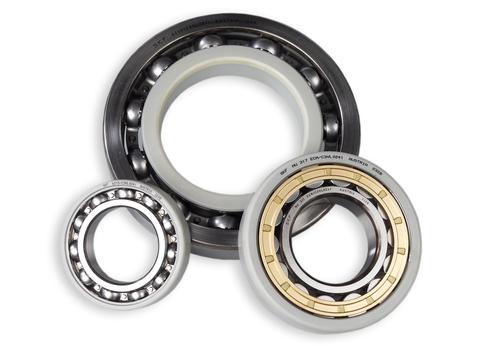
Rolling bearings perform vital roles in rotating machinery by helping to reduce friction, transmit loads, and locate and support shafts. Thousands of bearing types and styles offer designers a wide range of solutions suitable for applications across industries. But some application conditions will present particularly daunting challenges for bearings, which pose threats to optimized performance and service life.
Among other safeguards, a variety of specialty coatings uniquely formulated for bearings offer added lines of defense against adverse operating conditions. Most bearing types can be coated. Coated bearings can be specified into new applications or serve as "drop-in" replacements within design envelopes -- eliminating any requirements for drastic design changes or reconfigurations.
Delivering wear resistance
Bearings can be prone to wear for any number of reasons, whether due to poor lubrication conditions (associated with high temperatures and/or low lubricant viscosities), sudden variations in load or speed, standstill vibration, and/or particle or liquid contaminants. All can dramatically shorten bearing (and equipment) service life over time.
As an effective solution for premature wear, a patented wear-resistant carbon coating can be applied (by the manufacturer) to the bearing rolling elements and/or raceways. The coating (only a few microns thick) covers the contact surfaces using a specialized process ideally suited for bearings. The resilience of the bearing steel is not only retained, but its surface hardness is also doubled compared with standard grades.
To function properly in a bearing, a coating must be able to withstand rolling contact fatigue, create little friction, and prevent adhesive wear. This type of specialty wear-resistant coating succeeds on all counts.
Insulating against electric currents
Applications involving variable-speed electric motors, generators, and associated equipment risk damage to bearings caused by the passage of AC or DC electric current when the current uses a bearing as its path to ground. The resulting damage is referred to as "electric arc bearing damage," and its most common causes include asymmetry in a motor's magnetic circuit, unshielded power cables, and fast-switching variable frequency drives.
Stray currents can damage the contact surfaces of a bearing's rolling elements and raceways (electrical erosion) and rapidly degrade bearing grease. An additional risk develops from high-frequency currents due to inherent stray capacitance -- and the risk of damage increases if the application employs a frequency converter.
Once electric arc bearing damage has begun, excessive vibration, increased heat, increased noise levels, and reduced effectiveness of lubricant will combine to shorten a bearing's service life. The extent of damage to bearings will depend on the amount of energy and its duration, but the effects usually will be the same: pitting damage to the rolling elements and raceways, rapid degradation of the lubricant, and premature bearing failure.
Designers can "insulate a bearing from the outside" by specifying a very thin aluminum oxide coating to form a barrier against electric arcing and subsequent erosion of the bearing rolling surfaces. The coating is applied (by the manufacturer) on a bearing's outer ring or inner ring using a spraying technique and then sealed with a resin to protect against the conductive effects of water and moisture. Standard insulating coatings can withstand voltages of up to 1,000 V DC, or coatings can be developed for voltages as high as 3,000 V DC.
About the Author(s)
You May Also Like