Lock that shock, but make it painless
February 5, 2001
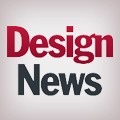
Bethel, CT -Descending a steep, bumpy grade, any rider could appreciate a mountain bike equipped with shock absorbers. But the same shock that cushions the big hits also dissipates pedal pumping energy during out-of-saddle sprints and uphill climbs. That's why many shock-equipped bikes have a lockout option that allows racers to turn off the shock on climbs and sprints when energy loss is most critical.
Nonetheless, activating a manual lockout system can be risky. The rider must remove one hand from the handle bar to actuate the lockout. This restricts use opportunities because one-handed riding sacrifices control, handling, and stability, and is almost impossible during stand-up sprints and uphill rips when the lockout is most needed.
To overcome the shortcomings of manual lockout systems, engineers at Cannondale set out to automate the damper lockout mechanism on the company's line of Lefty single-leg front suspensions. The electronic lockout feature they developed, called the Lefty ELO(TM), offers all the advantages of manual systems with none of the drawbacks.
One touch of a button activates the lockout; a second touch deactivates it. Pushbutton ease-of-use means the rider can lockout far more frequently, conveniently, and precisely. And no matter what the rider's skill level, it takes less than 1 sec to lock or unlock the shock.
But designing an automated damper lockout mechanism that fits within existing space, size, and weight constraints, proved somewhat daunting. Engineers achieved many objectives in early "proof-of-concept" prototypes, yet still they had a long way to go. One early prototype had a somewhat large motor mounted on top of the fork. "There wasn't enough room for the electronics and battery inside of the fork due to the long drive system between the motor and the lock-out piston," explains Cannondale Project Engineer James Gardner.
To minimize the drive system engineers had to put the motor powering the system deep inside the shock, limiting the motor's maximum outside diameter to 8mm. When they discovered a miniature motor from RMB (Ringwood, NJ), according to Gardner. "Bang! There's was a home run right there!"
Worse case scenario. The engineering effort leading to the final product got into full swing in the fall of 1999. "We wanted to use as many off-the-shelf parts as possible, minimize part changes, or at least use the same form factor as the parts in our mechanical lockout damper," explains Gardner. So the team pulled up the mechanical damper in Pro/E NGINEER , and used that as their footprint. Then put Pro/ MECHANICA to work for all of the FEA required in redesigning the entire valve for electromechanical actuation. "It ended up being hard to tolerance just because there was lots of stack up," Gardner says. "So we modeled everything in the absolute worse case scenario."
To simplify sealing challenges associated with the generation of high forces, engineers decided to put the motor as close as possible to the point of use. "Originally we thought we could put the motor on the dry side," Gardner explains. "But sealing bearings that small against the kind of pressures generated during lockout wouldn't work. We knew oil would seep into the motor over time, allowing air into the damper and giving it a bad feel. So we immersed the motor in the oil."
Ultimately, an 8-mm motor and a 1:25 ratio gearbox with a linear screw shaft was customized to fit inside the shock. With the base mechanical design decided, the challenge turned to system performance. Here engineers had to balance valve actuation time, voltage, current draw, and motor capability. "We gave equal weight to system power and the battery target life of 3 months," Gardner says. "Smoovy gave us so much smoothness and efficiency, that we made out on all counts. Using a standard 9V battery, we got the desired speed and torque, and the battery lasts six months with average use."
Engineers arrived at the optimum actuation time through design iterations varying lead screw pitch, motor starting ramp, system voltage, and oil characteristics. This included rigorous riding of prototypes through the autumn and winter of 1999. Hard riding in harsh New England cold, together with accelerated life testing, led to further optimization of these design variables in early 2000.
Riders race tested pre-production ELO prototypes at World Cup races last spring. Then ELO made its Olympic debut in Sydney with all seven of the Volvo/Cannondale riders using totally new ELO-equipped super light forks. Christoph Sauser, a Swiss, even won a bronze medal.
About the Author(s)
You May Also Like