LifeSense Hose Monitoring
April 1, 2011
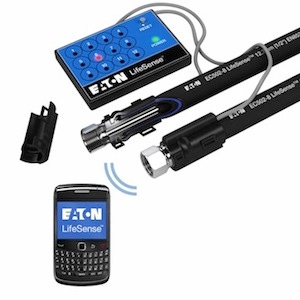
Sudden hose failure has been a majorpotential problem for fluid power applications since hydraulic hose was firstintroduced decades ago. Sudden failures can lead to safety issues, environmentalconcerns and downtime that in extreme cases, such as offshore oil rigs, havebeen estimated to cost as much as $500,000 a day.
But now using a real-time monitoring systemthat senses changes in the electrical resistance within a hose, Eaton Corp.'s new LifeSense hose monitoringsystem provides a way to avoid costly hose assembly failures.
"The uniqueness of LifeSense technology is thatit truly monitors the condition of the hydraulic hose as opposed to systemsthat predict hose failure basically using a time-based replacement process,"says Doug Jahnke, Eaton product marketing manager.
LifeSense Hose Monitoring |
Jahnke says it's impossible to tell when ahose is failing because it fails from the inside out. Most hydraulic hoses havea rubber elastomeric cover, a rubber tube and wire reinforcement. During itslife, the fatigue of consistent hydraulic surges eventually wears out the hose.
"There's been no way in the past to monitorthe condition of the hose and identify symptoms of failure as they areoccurring," says Jahnke. "The idea is to identify these conditions prior tofailure and with enough time that you can replace the hose prior to failure."
Eaton'snew LifeSense hose is very similar to two-wire braid hydraulic hose and wasdeveloped in conjunction with Purdue University and the Purdue ResearchFoundation's Office of Technology Commercialization. The goal is tocontinuously monitor the health of hydraulic hose assemblies and alert userswhen an assembly approaches the end of its useful life.
"Most hydraulic maintenance programs aredesigned to avoid hose failures by replacing assemblies at regular intervals,using a schedule based on usage data or past experience," says Jahnke.
As a result, a large number of hydraulichose assemblies can be discarded long before the end of their useful life outof fear that they might fail. LifeSense hose allows the user to utilize theuseful life of a hydraulic hose assembly, which is 50 percent longer than mosthoses are left in service today, according to Eaton's lab testing.
"A hose is basically part of a hydrauliccircuit, and what we've done with LifeSense technology is also make it part ofan electrical circuit," says Jahnke. "A very low voltage signal is goingthrough the entire length and circumference of the hose and, using feedbackfrom the electrical signal to measure resistance, we can determine if the hoseis nearing the end of its life."
"We've proven very clearly in the lab thatit consistently reports certain feedback that lets us know it's close to theend of its life," he adds.
The LifeSense monitor uses a wiredconnection with wires running from one end of the hose to a microprocessor andsoftware in the monitoring device. Whenever the equipment is on, it provides acontinuous monitoring process measuring electrical feedback using contacts onthe hose.
Right now, each monitor can be connected toup to eleven hoses. Any number of hoses can be monitored using multiplemonitors wired into either a 12 or 24V system, so it can be used on mobile orindustrial equipment. A converter for 110V operation is also available, and Eatonis actively working on a new wireless conection system as well.
The initial LifeSense hose offering includeswidely used -8, -12 and -16 two-wire hose assemblies. It offers performanceequal to industry standard 2SN pressure-rated hose, and is certified to thesame industry specifications as conventional hydraulic hose products. Thetechnology is also currently available for trial with factory-made assembliesincluding straight JIC swivel fittings.
About the Author(s)
You May Also Like