Fluid power adds high-tech thrills in amusement rides
June 23, 1997
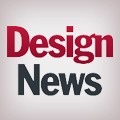
It may be industry's ultimate irony: Fluid power, for decades the technology of choice for producing enormous forces in bulldozers and industrial presses, has found a new niche: amusement parks.
If that seems hard to believe, then take a look at some of the country's biggest and best theme parks. Most are loaded with robotic figures that employ hydraulics and pneumatics to lift, twist, roll, and blink. For the past decade, fluid power has breathed life into animatronic figures ranging from prehistoric dinosaurs to U.S. presidents.
But now that role is expanding. Today, fluid power is primed to deliver high-tech thrills to the smaller venues, such as museums, carnivals, trade shows, race tracks, sporting events, and shopping malls. And it's adding a new dimension of realism to robotics in parks large and small.
Six degrees of entertainment. The clear winner in this new fluid-power trend is the small amusement park owner. The reason: For a comparatively small investment, amusement parks can offer the technology that was reserved for larger, wealthier parks a decade ago.
A prime example: the six-degree-of-freedom motion base. Not long ago, six- degree-of-freedom motion bases were reserved for million-dollar flight simulators. When motion bases became available for the entertainment industry, three degrees of freedom were the norm, mainly due to cost.
But now, at least two companies in the entertainment field have made the jump to six degrees of freedom, with more reportedly waiting in the wings. "Our company took the position that six degrees of freedom is not just the best, but the only way to go," notes Larry Hayashigawa, president of McFadden Systems, Santa Fe Springs, CA.
The reason, he says, is that the human brain is better tuned to six degrees of freedom. Audiences who ride on the motion bases typically watch a movie in a theater setting. When the movie suggests an on-screen movement--a pitch, roll, or yaw, for example--the motion base moves the audience's seats in that direction. Hayashigawa believes that six-degree-of-freedom systems more accurately match those on-screen movements than do three-degree-of-freedom systems.
"The human mind needs to experience realistic onset cues," he explains. "When the rider looks at the screen and expects one movement, but gets another, then motion sickness ensues."
McFadden's latest motion base, known as the 618A, solves that problem by providing motion in six axes. Those axes include x (thrust), y (sway), and z (heave), in addition to pitch, roll, and yaw. It accomplishes that by employing a 15-kW Vickers Integrated Motor Pump, Vickers SM-4 servo valves and servo controller, six hydraulic cylinders with 18-inch strokes, an analog controller, a laser disk player, and a personal computer.
During operation, the computer runs the motion profile and synchronizes it to the laser disk. Commands pass from the PC to the servo controller, which communicates with onboard position feedback transducers to determine whether the actuators are positioned properly. Motion profiles are updated 30 times per second. Along with a sound track and film, the laser disk also carries a time track that enables the system to synchronize the actions of an on-screen movie to the motion base's motion profile.
Lowering the cost. The key to McFadden's success with six-degree-of-freedom systems is its ability to build the units for roughly the same cost as a three-degree-of-freedom systems. McFadden engineers accomplish that through a "semi-mass-produced" design. They employ the same 18-inch Vickers cylinders and transducers. Bearing assemblies are common; loading ramps, control racks, and power units are pre-engineered. All the sound systems are also pre-engineered for a 20 x 25-ft theater.
McFadden engineers say that the development of quieter hydraulic systems has contributed to lower cost. By employing Vickers' Integrated Motor Pump, they contained all the unit's hydraulics within the ride area. Whereas hydraulic motors and pumps were once too noisy to be placed in such locales, they are now virtually unheard over surrounding noise. Because the Integrated Motor Pump emits less than 65 dB, it can be placed only a few feet from riders without causing a noise problem.
"We can now place the power unit right inside the theater," adds Michael Rogers of McFadden Systems. "We get better response and we don't need to build special rooms or dig trenches for hydraulic hoses."
In McFadden's VR Express, a capsule-like motion base and theater, the entire hydraulic power system is housed beneath the unit's loading ramp, within a few feet of riders. Because the power unit is in such close proximity to the ride, engineers could replace conventional welded pipe with hoses for the hydraulic lines. That, in turn, further reduced noise and simplified maintenance, since flexible hoses can be more easily cleaned.
Similarly, engineers at Iwerks Entertainment, Burbank, CA, have realized advantages by incorporating six axes in their newest motion base--the Transporter. The firm, co-founded by former Disney Imagineer Don Iwerks, recently designed a custom 100-seat theater for Dollywood Park, Pigeon Forge, TN, which uses the six-degree-of-freedom technology to deliver a realistic feel to a car racing film.
"Six degrees of freedom allows our engineers to program the motion into our software with some very rich subtleties," notes Vito Sanzone, vice president of marketing for the firm. "It allows the programmers to do certain tricks--the kinds of moves that aren't possible in three-degree-of-freedom bases."
Like McFadden, Iwerks incorporated the Vickers Integrated Motor Pump in its design because it helped reduce noise and, therefore, cut cost. It also adds to the theater experience, Sanzone says. "The people who enter our theater shouldn't think about how fast the seat is moving or how much noise the system makes," he explains. "Our goal is to make them lose touch with reality for five minutes."
Taking the "boing" out of robotics. Innovations in fluid power have also spread beyond the use of motion bases. By applying new techniques in both hydraulics and pneumatics, engineers can create a new generation of more life-like animatronics.
These animatronics move more smoothly and convincingly, mainly because engineers have eliminated a problem that has long plagued animatronic characters. That problem, sometimes referred to as "boing," occurs when a hydraulic or pneumatic actuator reaches the end of its stroke. As it does, the character's movement stops suddenly, causing it to vibrate. Hence, the term, "boing."
At Advanced Animations, Stockbridge, VT, engineers alleviated that problem by applying special hydraulic and pneumatic techniques. They recently designed the T-70 Cinebotic figures for Universal Studios Florida's new interactive entertainment experience, called Terminator 2 3-D: Battle Across Time.
The T-70 robots, which stand eight feet tall and weigh about 500 lbs, use hydraulics to perform eight separate on-stage moves: a body forebend; body turn; and body rotation; as well as forearm, shoulder, and wrist moves. The T-70s also employ pneumatics to turn the head, as well as move it up-down and left-right.
To accomplish the body, arm, and shoulder moves, engineers from Advanced Animations employed a "hydraulic compliance" technique. This enables the system to manage the inertia caused by the quick acceleration of so much mass. It eliminates the stiff motions often associated with older animatronics.
Advanced Animations' hydraulic compliance system involves dual-loop PID servo control. It employs hydraulic cylinders from OilDyne Inc., Minneapolis, MN, and rotary actuators, direct-drive servo valves, and electronics from HR Textron/Micro-Precision Textron. The system also employs tubes and fittings from Parker Hannifin Fluid Connectors.
To provide force feedback, engineers place load cells from Entran Devices Inc., Fairfield, NJ, between the cylinder body and rod end. Force and position data are gathered in separate channels in a servo card. Using a proprietary combination of hardware and software in the servo card, the system processes force and position feedback signals, then responds with commands to dampen potential vibration.
"Our technique looks at three variables: force, time, and position," notes Bob Crean, vice president of operations for Advanced Animations. "Anyone who looks closely at the human body can probably figure out what we do."
For pneumatic dampening, Advanced Animations engineers use a system known as Advanced Inertial Management (AIM). Key to the AIM technique is a small, custom-molded bumper made from Texin(R), a thermoplastic polyurethane made by Bayer Corp.'s Polymers Division, Pittsburgh. Pneumatic cylinders use two of the bumpers--one at each end of the stroke. By employing the Texin bumpers, engineers can program quicker robotic movements, without the associated "boing" phenomenon when the cylinder bottoms out.
Compliance, whether hydraulic or pneumatic, enables engineers to improve animatronics in three ways, Crean says. First, it reduces mechanical stress on the robots during programming, which prevents damage. Second, it smoothes motion, which lowers mechanical stress on the robot during normal performance, reducing the need for maintenance and downtime. Third, it makes the robot's motion more pleasing to the human eye.
"Watching it, you wouldn't necessarily know if it uses hydraulic compliance," he says. "But you'd know that the motion is very realistic."
Science center's ride showcases hydraulics
Toledo, OH--Like good wallpaper, fluid power components often serve an important function with nary a notice. Much of the general public isn't aware of the role fluid power plays in such highly visible applications as automotive and construction equipment, let alone in less visible functions, such as industrial automation.
But when the COSI Toledo science center opened its doors in March, fluid power's anonymity began to slip away. That's because the slick new museum displays fluid power in a way that it's never been showcased before.
With the help of Trinova Corp., COSI has constructed a state-of-the-art hydraulically powered ride that not only employs fluid power, but explains it as well. "Audiences want to learn about roller coasters, rides, and Hollywood effects," notes Joe Wisne, director of exhibition development for the center. "And hydraulics are involved in all of those attractions."
Although the center is geared for the general public, that hasn't stopped it from teaching fluid power while visitors enjoy the experience of riding a six-degree-of-freedom hydraulic motion base. To be sure, it's a light form of entertainment and not a course in hydraulics, but it also serves an educational role. During the ride, a laser-disk-based soundtrack peppers riders with such engineering expressions as "kinematics," "rotational degrees of freedom," and linear degrees of freedom."
Meanwhile, other visitors stand in a separate room beneath the attraction and watch the hydraulic motion base in action. Hydraulic cylinders on the base are specially painted and highlighted with a black light to make for easier viewing. One of the reasons behind hydraulic's new center stage appeal is its presence in some of the technology world's highest profile applications. It now plays a huge role in such theme parks as Universal Studios and Disney World ( Design News, 7/25/94, p. 21 and 11/20/95, p. 78), as well as serving in Hollywood movies and Broadway productions.
Another of the driving forces behind its newfound popularity is cost. Two decades ago, specialty companies built six-degree-of-freedom flight simulators that cost more than a million dollars. Now, such firms as McFadden Systems, Inc., Santa Fe Springs, CA, build six-degree-of-freedom motion bases for a fraction of that cost.
For an industry that has long existed outside the public eye, fluid power's high profile at COSI Toledo serves an important educational purpose, say industry insiders. "We live in a world where hydraulics are an integral part of our lives, but we never see it," says Peter Parsons of Vickers. "This exhibit is designed to stimulate people to understand the fluid power world, and maybe even become a part of it."
Exclusive to Design News Online
Terminator 2 3-D Facts
Terminator 2 3-D is the first time that a feature film's creative production team joined together to bring a motion picture concept in a theme park attraction. This includes stars Arnold Schwarzenegger, Linda Hamilton, Robert Patrick and Edward Furlong ; director James Cameron; and special effects wizards John Burno and Stan Winston.
Over 100 miles of cable is woven throughout the attraction
It costs $60 million and combines 3-D cinematography, digital composite computer graphics, one-of-a-king cinebotics and live-action stunt work.
A series of theatrical rigging linesets, motors and controllers, custom-designed by Scenic Technologies fly scenery in and out on cue.
The three projection screens used in the "ride" each measure 23 feet high and 50 feet long and are coated with an ultra-high-gain material to provide the best possible 3-D imagery.
The hydraulic plumbing system is driven by 25-hp motors and capable of producing over 3,000 psi fluid pressure.
About the Author(s)
You May Also Like