Engineering News 7598
December 2, 1997
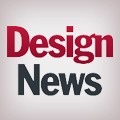
High-tech holidays
Newton, MA--Tis the season to be jolly. It's holiday time again and we're racking our brains for that ultimate gift. Rather than relying on those old "fall-back" ideas, here are some novel technologies that answer your wish list.
Fulfilling part of your order, Explore Technologies, Santa Clara, CA, brings a round-the-world experience to the gift market. No, this product isn't your typical CD-ROM, videotape, or computer game adventure but rather Odyssey, AtlasphereTM an interactive electronic atlas.
Users activate Odyssey by stimulating a response through the use of a stylus. Using voice synthesis, the Atlasphere reports requested information or activates one of five Nintendo-like games, punctuated with catchy sound effects, music, and speech. All information is stored in a built-in database.
Initially, the design was envisioned as a vertical structure that would easily house components such as batteries and speakers. But Odyssey's designers wanted to preserve the visual and tactile experience of a traditional globe, while providing the geographical detail of an atlas with the speed and flexibility of a computer. To achieve this goal, they enlisted the help of Studio Red, (Menlo Park, CA), an industrial design firm specializing in computer, medical, and industrial technologies.
"The challenge of design," says Philip Bourgeois, president of Studio Red, is that "While you can make it [the globe] look incredible, you have to consider mechanical, manufacturing, and service issues."
Both the housing and acoustic design were completed using Intergraph's EMS software and prototyping was done on Maxmill software from Intergraph. Studio Red also uses Altas and Pro-E CAD systems in the design process.
A global challenge. Given the geometry, the design team faced some unique fabrication challenges. Production begins with a flat piece of pre-printed sheet vinyl that is vacuum-formed into the shell of the sphere. The sphere is then insert-molded into the desired shape, back-filled with 331 polystyrene, and cantilevered from a lower housing and arm assembly (injection-molded, high-impact ABS) at an 11-degree tilt. At the base, below the cantilevered section, is a tab that when lifted allows the user to remove the Atlasphere from its base.
Besides providing support, the base also houses the electrical components, including a large speaker. Because zones define the boundaries of the acoustic areas a port and chamber are not required.
One challenge Studio Red faced in developing the speaker housing was that by placing a large perforated area onto the aesthetic surface, knit lines could develop and as a result a need to repaint the device. To avoid this, Studio Red introduced Troy Plastics an injection-molding company out of Hayward, CA, to the design team. They eliminated this extra step by modifying the material's technology and tool processing.
Another design consideration was the storage of the stylus. Standing the stylus in the base of the globe presented the potential for damage. To resolve this Studio Red conducted a series of tests and fine-tuned a knock-away pocket that automatically releases the stylus if it is accidentally knocked, yet secures it for storage.
Engineers at Explore Technologies developed Near-TouchTM, a patented, interactive, proximity-sensing technology that is charged by a proprietary conductive urethane on the inside of the sphere.
"This technology can be used with any 3-D shape; human body, rocket ship, or automobile," says Jim Marggraff, co-founder of Explore Technologies with Mark Floweres and Dave Conroy. "It allows us to make any 3-D surface touch-responsive with high resolution at a very low cost. NearTouch is also economically scaleable for large, flat applications."
This pen-like object activates electronically defined quadrants in the sphere. Made from urethane rubber and ABS, the stylus evolved from the initial flexible rubber-body design to one with a center rubber section encased in a plastic cone.
Included in the package are two video game cartridges featuring five games, one of which plays a Jeopardy-like tune while users race to find the locations a digitized host announces. Additional overlay vinyl globe sleeves, removable read/write information cartridges, and two-way connectivity with a personal computer will be available down the road.
The Odyssey Atlasphere is available at Sharper Image, The Nature Co., Brookstone, FAO Schwartz, Barnes & Noble, Zany Brainy, and Hammacher Schlemmer for $399. Orders can also be placed through Explore Technologies at (888) 456-2343.
An inventors' world. Unique design technologies such as those incorporated in the Odyssey Atlasphere provide alternative solutions to everyday designs.
In pursuit of offering such products, Hammacher Schlemmer hosts a yearly contest called Search for Invention. This national competition is open to inventors of patented consumer products that have yet to reach the marketplace.
When all your holiday shopping is said and done you may want to kick off the new year with a spill-proof design from Calvin A. Page, of Spill Not Designs, Wellfleet, MA.
His invention, a pendulous beverage server, is for transporting and serving drinks without fear of permanently staining your carpets.
A molded ash-wood tray with recessed pockets secures the beverages in place. Extending from the center of the tray is a tapered cone with a recessed interior of approximately 1 inch in diameter and 3/8 inch long. A large piece of steel piping about 1 inch long is crimped onto the end of a nylon-woven rope with an epoxy. The other end of the rope is secured in an ash-wood handle with an epoxy and clothespin spring mechanism. When you lift the handle the rope and piping mechanism raises. The piping then acts as a weight to pull the rope in when you are done serving drinks.
The bottom of the tray is sealed with a water-based polyurethane and the bottom with a lacquer. This unique gift is sure to rock the boat without any messy waves. Call 1-888-SPILLNOT to order the pendulous beverage server for $30 plus shipping and handling.
And still to reach the market... LiteRite, a handwriting force-control training aid was developed by 13-year-old Jamesen G. Saviano of Norwalk, CT.
This magneto-mechanical device teaches the user to apply a lighter force when writing, eliminating broken pencil tips and hand and finger fatigue.
LiteRite is compatible with standard pens or pencils, and can be installed or removed quickly. It is made of a thin, metal or plastic tube, a pair of magnets oriented in attraction, or a magnet and steel configuration. Writing is conducted as normal. When a writer applies too much pressure, the mechanism separates according to the threshold magnetic effect and forces a sudden hand movement that leaves a pen or pencil mark on the writing surface. The device instantly resets when the user reduces the applied pressure.
Traveling west we find Thomas Merritt and his invention, an electric hairdryer.
Normal hairdryers operate on up to 15A at a maximum of 1,850W. Merritt's hairdryer operates on thermoelectric cooling and heating modules, consumes 1/10 of this power, and is rated at 144W (24V dc). In testing, this hairdryer can dry short hair in approximately 90 seconds without damage.
This dryer heats or cools the air to the appropriate temperature by adjusting to the conditions of the ambient atmosphere to achieve operation at 20% relative humidity. Other features include a motor-driven fan, at least one electric switch, and a 20V 6A power supply.
The motor-driven fan forces ambient air across each face of the thermoelectric module at a high velocity. In turn, the module behaves like a heat pump. It absorbs heat through a first heat sink, in contact with one side of the module, pumps that heat through a module with a low-voltage dc electric current, and rejects it through a second heat sink in contact with the other side of the module. A heat pipe releases the air for drying purposes.
Zooming in on areas that receive large amounts of snowfall, it appears that sledding is a popular sport.
Brent Lee Farley of Baltimore, MD created a snowsuit for sledding, Sled pants. With this invention your body now becomes the sled.
Farley's initial prototype was fabricated from a purple, foam-covered leather. However, he envisions the commercialized version as an inflatable body sled.
The "pants" consist of an ergonomically contoured seat and leg component that covers the back, avoiding a suit full of snow. Pivoting lower-leg sections can be raised or lowered for getting back up the hill. Adjustable leg and waist straps provide a secure fit. Sledding will never be the same.
This is only a sample of the remarkable gifts that lurk beyond your doors. Although not all of them are available yet, if you dig deep enough you'll find a world of gifts with a history of design.
Material switch boosts knee bolsters
Dearborn, MI--Ford selected a material for the knee bolster in its 1997 F-Series pickups and Expedition sport-utility vehicles for its cost and weight savings. The problem was that performance standards were not met when it came to fit and finish, paintability,and durability.
Teaming with Dow Automotive (Southfield, MI), Ford found a material that could meet both performance and cost targets. After looking at many materials to replace the compression-molded, thermoplastic, glass-mat-reinforced polypropylene, the Ford/Dow team switched to Dow Chemical's PULSE(R) 830 PC/ABS resin. The team then designed and implemented the new knee bolsters in 12 months. The redesigned driver's-side and glove-box door assemblies had greater dimensional stability, fewer paint adherence and repairability issues, and little or no post-molding rework.
"We didn't come in with a preconceived idea of what material to use," says Brian Grosser, senior program manager for Dow Automotive. "With Dow's broad product portfolio, we were really 'material neutral.' That means we could offer a solution that provides lower cost, while meeting performance requirements, as opposed to a supplier that's driven by a limited offering of materials."
The new material system had to meet, or exceed, current FMVSS 208 crash performance standards. It also had to provide improved quality and reduce scrap costs, with a minimum of tooling investment. PULSE measured up to the task on all counts.
The running change to the new resin saved costs; production increased and scrap rates dropped. Also, fit/finish improved, surface defects were reduced, and, when paint chips or scratches did occur, they could be repaired on line.
"Not only does the part look good," says Grosser, "but its long-term durability means it will continue looking good."
The redesign has a steel plate behind the plastic cover. However, Dow Automotive has under development with Ford an all-plastic, mold-in-color, energy-absorbing knee bolster design. It should debut with the 1998 model year.
Composite helps Indy car 'wing' to victory
Hilliard, OH--In Indy-car racing, the winning edge sometimes comes layer-by-layer in the car's design. That's the case with the PPG CART World Series competition Team Rahal.
To gain that edge, Team Rahal employs the advanced composite Hy-BorTM in the rear wing structures of its 230 mph Reynard/Ford-Cosworth Indy cars. Team sponsor Textron Systems (Wilmington, MA) developed the material using a proprietary process that combines the company's boron fibers with a graphite prepreg. The result: a material with limited weight and exceptional strength.
"We use Hy-Bor in our superspeedway wings because its strength-to-weight ratio enables our engineers more design freedom," says Team Rahal Team Manager Tim Cindric. "The freedom has resulted in more overall downforce, a much more consistent airfoil under dynamic loads, and greater performance predictability at the race track."
"To gain the same strength we can achieve with Hy-Bor," adds Production Manager Joe Strausbaugh, "we would have to double the ply of conventional unidirectional carbon fiber in the rear wing. An extra ply means extra weight, and weight restricts performance. We can't have that."
Close cooperation between the two parties added to the design's success. In fact, Textron Systems spent several years working closely with Team Rahal in the design, development, and testing to make this opportunity possible. "We're confident that the result of our efforts will be better handling and improved lap times for drivers Bobby Rahal and Bryan Herta," reports Tom Shahood, Textron Systems product applications manager.
HY-BOR BORON/GRAPHITE HYBRID PREPREG |
Tensile Strength |
2110 MPA |
Tensile Modulus |
255 GPA |
Strain |
Compression Strength |
3233 MPA |
Compression Strength |
283 GPA |
Flexure Strength (3 point) |
3006 MPA |
Short Beam Shear |
117 MPA |
Opel saves weight with hydroforming
Bochum, Germany--Opel is installing a 20 million DM hydroforming system at its Bochum plant in Germany to make mild steel engine cradles for the new Astra. The fully automated system is the most comprehensive hydroforming application anywhere in the world, claims Dietmar Kay of Schafer Hydroforming, the German company that supplied the new equipment.
In hydroforming, the first blank is placed in the die. As the die closes around the blank,the open ends of the bland are plugged by two axial rams. Water is then injected into the blank and the pressure increased until it is sufficient to force the blank to deforem and fill the die. In addition to engine cradles, hydroforming is already being used in the production of exhaust manifolds, dashboard cross members, and structural parts for roll-over protection.
Hydroforming is a weight-saving technique used to form components that can be made from a hollow section blank. It requires a hydraulic press with a two-piece die, two axial rams, and a counter holder.
In the new Opel system, a 2.6m length of tube is turned into a finished engine cradle ready for assembly. After a pre-forming operation, the tube passes to the hydroforming press. Here it is shaped and punched before going through a washing station and a final machining station, where the cradle ends are finished. Six-axis Fanuc robots do all the parts handling. When full production starts in January next year, the line will produce 1 million engine cradles a year, running on three shifts, five days a week.
Easy-to-learn CAD software eases change to 3-D
Munich--German machine builders have always had a strong reputation for high quality and good reliability, but how are they coping with the integration of modern design software? In an industry based on the manufacture of capital-intensive products, a certain degree of critical conservatism with regard to new methods is a laudable asset. What does a machine designer, more familiar with two-dimensional techniques, look for in 3-D CAD software?
Kaspar Walter GmbH manufactures machines and equipment for producing the high-precision copper cylinders used in the rotogravure printing process. A typical application for this process is the colored printing on candy bar packaging. The industry expects a high degree of customization, so the machines are relatively design-intensive. After a number of years using 2-D CAD software and early disillusionment with the long learning period of some other 3-D software, the company's design department has started to change to Intergraph's Solid Edge 3.0 running on Windows NT. After starting with just two Solid Edge workstations for use on new projects only, Klaus Hofmann, Walter's technical director, expects his designers to gradually change completely to Solid Edge as each product design cycle comes to a close and a new one begins.
At the start of a new design project the company adopts the "top-down" approach, starting with the whole machine and breaking it up into smaller assemblies using Solid Edge's Pathfinder to keep track of features. With the designers themselves working directly on the assemblies, the technical draftsmen are no longer needed because Solid Edge handles much of the detail. The software has freed this section of the workforce to produce documentation, such as operating manuals and other items of technical literature, by cutting and pasting output from the program. With its feature-design approach, which lets the designer produce a solid model as he or she would make it, Hofmann rates Solid Edge as very easy to learn. Since experience equates to age, this is important at Walter where experienced, older engineers must be able to learn the system quickly.
Walter's engineers like the program's drawing revision capability, but the parts lists are still managed on a separate system using the company's own nomenclature coding. Another feature the designers find useful is the SmartSketch 2-D drawing tool, which is handy for quick modifications and eases the transition from 2-D to 3-D. The company also fully exploits Solid Edge's 3-D modeling capability by using it to help customers visualize the product. This improves customer confidence, speeds up the specification process, and helps prevent any misconceptions.
The main benefit, though, is the shortening of the machine design cycle. "We have been able to substantially reduce the design time for our machines from nine to four or five months," Hofmann says. Intergraph's Industrial Marketing Manager in Germany, Michael Muller, confirmed that Walter's savings are fairly typical. He adds, "Provided the customer accepts the philosophy of 3-D modeling, he can quite easily save up to 50% of the design time compared with conventional methods."
Partnership pares time-to-market
Buenos Aires--As engineers everywhere seek to reduce the size and cost of the electronics in their designs, the use of single device PCs (SDPC) is on the rise. The strength of the technology is that it provides all the functionality of a desktop computer in a package measuring only about six inches square, and is as easy to integrate as a semiconductor device.
"The applications today are coming from literally all over the map," says David Feldman, president of ZF MicroSystems, a flourishing startup company that designs SDPC modules for the embedded PC market. "We're getting interest from OEM makers of communications devices, medical instruments, and test equipment, to name just a few," Feldman emphasizes.
Some companies are choosing to develop the technology in-house. But a whole new industry has recently sprung up, consisting of small companies like ZF that are using their expertise in embedded control to help OEMs--even computer technology leaders like IBM--bring products to market faster.
That was the case for IBM Argentina. In 1992, the company received a contract to provide on-board fareboxes for about a third of the 15,000 buses operating in the greater Buenos Aires area. Intended to relieve harried bus drivers who are busy fighting traffic in the bustling metropolis, the boxes make change, print tickets, log passenger traffic, and perform other administrative tasks.
IBM's initial farebox was an eight card, microcontroller-based design. At 201.4 cubic inches, designers weren't thrilled with the size of the box. But the more critical issue, says project manager Ray Brinks, was its nearly 1,000 interconnects. "In my experience, connections are expensive to assemble, and they're expensive to maintain," says Brinks. "And there we sat, with cables snaking all around and a seemingly endless number of contacts."
Given the poor state of repair of many of Argentina's roads, coupled with the fact that many busses use truck-type suspension systems, reliability concerns became the driving force for change. "We knew if we could drive down the number of interconnects, the mean time to failure would go way up," says Brinks.
In the first redesign, IBM moved to a much more compact 3-board design. A 386SX-based PC/104 CPU module eliminated the complexity of traditional motherboards and backplanes, reducing the number of interconnects by nearly half. But not yet satisfied, the engineering team looked at ways to further improve their design--by going to a single card design.
IBM initially considered developing the technology in-house, but opted instead to partner with ZF MicroSystems. The startup company had recently introduced an SDPC that is small (2.2 by 3-inch), yet powerful, with all the functionality of a motherboard, including: a 33 MHz 80386SX CPU, DRAM controller, serial and parallel I/O ports, 8 or 16-bit ISA busing, floppy and IDE disk controllers, AT-compatible BIOS, an embedded version of DOS, and 356 kB of flash memory for applications and data storage. It has all that, but the power output is a mere 3w.
Brinks recognized the difficulty in trying to work with a company located thousands of miles away. So he relocated one of his engineers to Palo Alto, CA, where ZF is based, to assist in developing the layout for IBM's single board design. The collaboration resulted in a final product, Brinks believes, that defines the state-of-the-art for computer-based transportation systems.
A mere 254 cubic inches in size, the new, single-board design has only 254 interconnects as compared to the 940 on the original eight-board design. Brinks estimates that as a result the system has 10 times the reliability, which is key with so many bus drivers out on the road.In fact, a farebox has not failed yet. The cost of the system is also less: approximately 32% less than the original design.
"I think it would have been a much more expensive and time-consuming effort if we had had to develop all the skills in-house," says Brinks. "From our perspective, once that module is in place and running, we don't really need to know too much about how it works inside."
Prospector follows Clementine to Moon
by Rick DeMeis, Associate Editor
Sunnyvale, CA-- Twenty five years ago this month, Gene Cernan shook the lunar dust from his boots as the last man to walk on the Moon--and NASA hasn't had a direct, dedicated mission to Earth's satellite since. This month, if all goes as planned, the agency's Lunar Prospector spacecraft begins beaming back data from lunar orbit as the first of its peer-reviewed, competitively selected Discovery missions. Brought about under the mantra of "better, faster, cheaper," Prospector follows the DOD-led Clementine mission of 1994 that used Star Wars sensor technology to image both the Moon and an asteroid. Program budget is $63 million--effectively less than one forth the cost of 1966's Lunar Orbiter.
Ever since Clementine's sensors indirectly indicated water ice in a permanently shaded crater at the south lunar pole, investigators have been anxious to return with specific divining instruments. Lunar Prospector is a compact, 650-lb spin stabilized probe whose year-long mission in polar orbit aims to map geological features and minerals, including water. Three 8-ft booms projecting from the 4.5-ft diameter drum-shaped body, 4.25-ft high, carry scientific instruments, isolating them from spacecraft bus-generated EMI.
The instrumentation consists of:
A gamma-ray spectrometer to determine lunar-surface elemental composition.
A neutron spectrometer to detect water.
An alpha-particle spectrometer to sniff out gases.
A magnetometer and electron reflectometer for mapping magnetic fields.
A Doppler gravity experiment will also be conducted using the spacecraft telemetry signal. Here, by detecting changes in Prospector's orbital velocity, lunar mass concentrations will be mapped.
The Prospector spacecraft was developed, built, and tested within 18 months. One key was concurrent development of an electrical set for testing the main spacecraft bus systems such as attitude control, telemetry, and electrical power, both solar and battery. Hewlett-Packard's Test and Measurement Organization (Palo Alto, CA) developed the set from commercial off-the-shelf components. "The only custom parts are the cabling, rack, and software," says Mark Triolo, HP account manager responsible for liaison with prime contractor Lockheed Martin. "We were involved early in the design process, which helped in defining and meeting the short schedule," he adds. Lower cycle time was also aided by using the HP VEE (Visual Engineering Environment) graphical programming language for software development.
For testing, the system furnishes spacecraft power in lieu of batteries or solar cells on line. It also stimulates bus systems, such as the sun sensor, separation, and RF systems, and monitors the responses. The test set is modularized so that the roughly half of it needed for final checkout can be shipped to the launch site. These modules are remotely operated and ruggedized to withstand the heat, humidity, and vibration in the launch-pad bunker. Finally, HP designed the test set with an eye on future spacecraft based on similar buses. The system can be customized via software for their specific missions.
Cutting rodless cylinders down to size
Alpen, Germany--Where space is at a premium, pneumatic system designers often prefer to specify rodless cylinders for actuation tasks. For example, a rod-type cylinder measuring 25 mm diameter with a stroke of one meter only makes about 40% of its installation length available as useful stroke. With a rodless cylinder of the same size, the figure increases to 80%. But this advantage reduces for shorter strokes; for example, with a 500-mm stroke only 60% of the length can be utilized. Clearly, designers would welcome any reduction in the basic length of a cylinder, particularly for shorter strokes.
With its LINTRA-LITE(R) rodless cylinders IMI Norgren has tackled this problem from a number of angles. One important design criterion is the sealing of the movable yoke in the cylinder slot to achieve minimum leakage. The stability of the extruded-profile cylinder wall is crucial here, and Norgren development engineers used finite element analysis to optimize the cross-sectional shape of the cylinder. This analysis showed that the slot widened less under pressure if the grooves for switch mountings were positioned on the upper sides of the cylinder. Deformation in the all-important slot area is less than 0.3 mm.
A polyurethane strip seals the slot on the inside, which is zipped together with a polyamide cover strip on the upper side. A strip divider separates the two strips as the yoke moves to and fro along the cylinder, and the choice of materials is critical. Gradual parting of the strips gives less friction, but takes up more space.
In the LINTRA-LITE, a sharper separation angle is used to reduce size, and the seal material ensures minimum friction. Commenting on the design, Werner Hubl, Norgren's managing director at Alpen, says: "We've just about reached the cost-effective limit on the ratio of stroke-to-installation length." He quotes materials handling and door actuation as typical applications. In fact, cylinders based on a modified LINTRA-LITE system operate the doors of the ICE express trains on the German Federal Railway.
Ice cream, heat transfer, and Modern Art
Newton, MA--Here'sa stocking stuffer idea for that someone with a sweet tooth on your shopping list: a self-defrosting ice cream scoop.
Manufactured by the Zeroll Co. (Fort Pierce, FL), the basic objective of the product is to warm up that frozen scoop of rock-hard fudge swirl. "Ice cream typically comes out of the freezer at about 10F," says Zeroll owner Tom Funka, "Which means you practically need the forearms of a weight lifter to get a serving of ice cream into the scoop,not to mention a way to gracefully serve something that has now frozen fast to the scoop."
The scoop consists of a 0.125-inch- thick die-cast aluminum shell, partially filled with what Funka describes as a special "defrosting liquid." The scoop transfers heat to the ice cream by relying on the high thermal conductivity and low heat capacity of aluminum in conjunction with a high-heat-capacity liquid. The surface is hardcoat anodized for better wear, and the producer can also apply a non-stick teflon coating.
The system works by transmitting heat from the scooper's hand through the high-conductivity handle into the high-heat-capacity liquid, which then flows into the scoop, where the heat is released to melt the ice cream. Why not simply make the scoop out of solid metal? The thermal transfer across the interface would go way down, not to mention the residual stresses created by two materials with different rates of thermal expansion.
A major advantage of the scoop's design, which is on display at the Museum of Modern Art, says Funka, is the absence of any mechanical devices. "There's nothing to break," he points out. How well the Zeroll scoop actually works compared to others on the market is debatable, but millions have been sold since the product was introduced in 1936. To wit, ice cream giant Ben and Jerry's uses the scoop. This writer, however, recommends more exhaustive field testing involving copious consumption of ice cream.
The Zeroll scoop is available at Williams Sonoma and Crate and Barrel stores or call Zeroll at (800) 872-5000. It retails for about $15.
About the Author(s)
You May Also Like