Compact Linear Motor Gantry
July 19, 2010
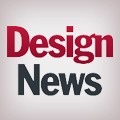
Thedesign goal for Aerotech's new small footprint AGS1500 gantry is to optimizemechanical stiffness of the gantry for precise contouring accuracy in 2-Dspace.
Designedfor a smaller footprint and payload capacity than the company's AGS15000 gantrysystem, the new gantry maintains the same design goals in a smaller format. Itoptimizes the mechanical stiffness in the structure of the gantry, reducingangular errors to improve contouring accuracy. The system is designed fortravel distances up to 500 x 500 mm, loads up to 15 kg and provides velocity to3 m/s, and accelerations up to 5 g using brushless linear servomotors.
Target applications include ultra-precise,high-dynamic contouring, precision micromachining, stencil cutting, fuel cellmanufacturing, solder-ball placement, printed electronics manufacturing,high-speed pick-and-place, automated assembly, vision inspection, dispensingstations and high-accuracy inspection.
Compact Linear Motor Gantry_A |
"Thekey with contouring applications is maintaining precise control of curvedmotions while also maintaining high speeds to maximize throughput," says JimJohnston, product manager for Aerotech's Automation Systems Group. "For manymechanical systems, the throughput versus tolerance trade-off is the keychallenge. Especially with a gantry-type system, there is a lot of inertialenergy to deal with to optimize performance when machining small features ormaintaining small contour accuracies."
As a system executes small contouredmotions, overcoming the inertia of the system during those moves usuallyresults in position errors. With micromachining a square corner, for example,it's impossible to instantaneously decelerate one axis and instantaneouslyaccelerate the other axis, so the system can easily overshoot and producesquare corners that are distorted. The planar design of the AGS1500 optimizesthe motion to reliably machine the sharp corners, or any other contour that maybe required.
"Innovations in the mechanical design includethe gantry's planar design, which helps to reduce both the center of gravity ofthe system and angular errors," says Johnston. "From a software standpoint,advanced control algorithms optimize gantry operation. An Enhanced ThroughputModule measures the energy that the gantry system is inducing into the baseplate, and allows the controller to feed forward or inject that energy signalback into the gantry control."
Gain Scheduling is another feature that ispart of the controller's dynamic toolbox. It reduces settling times andprovides a mechanism within the controller to dynamically change servo loopgains as it completes the move. The result is that an application can move intoposition and settle more quickly by using higher servo gains.
Johnstonsays there are two trends with this type of precision machinery. One trend isto produce components with ever-increasing tolerances as technology improves. Theother trend is to maintain a given tolerance while increasing throughput toexpand capacity by making parts faster. Normally as you increase tolerances,throughput decreases. The AGS1500 design keeps both in mind so that highertolerances can be maintained with higher throughput.
Another goal is optimizing the system forthermal expansion to ensure consistent operation during temperature variations.These variations occur both from changes in the surrounding environment, aswell as differences in application demands such as speed and accelerations fromdifferent part programs.
Temperature variations cause components toexpand and exert different stresses in different areas over travel. As such,lower servo loop gains must be used, which limit the capabilities and bandwidthof the system. Elements designed into the AGS1500 gantry enable it to operateat full capacity over a wide temperature range, allowing it to use a higher setof gains without causing instabilities
About the Author(s)
You May Also Like