CADalysts for easy data transfer
November 6, 1995
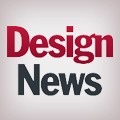
After years of hassling with often-clumsy translation schemes, engineers are looking for simple ways to move their CAD data between different software packages. And, led by Hewlett-Packard, MacNeal-Schwendler, Autodesk, Bentley Systems, and Intergraph, the software industry is finally scrambling to accommodate them.
"It's going to be fascinating to watch," says Bruce Jenkins at Daratech, a CAD market-research firm based in Cambridge, MA. However, with several different standards efforts underway, there is a danger of too many vendors developing differing methods, he notes--not unlike the proliferation of UNIX "flavors" a decade ago.
But there's also good news for users, he adds: "Vendors are participating in each other's initiatives."
One endeavor underway: the Industry Alliance for Interoperability, aimed at developing an industry standard for "objects." That will allow whole models and parts to be easily manipulated among different applications. Bentley Systems, initially concerned that the Alliance was weighted toward founding members such as Autodesk, recently decided to join the group--which one member called the "acid test" of AIA's openness.
Autodesk is spearheading another data-sharing effort, the Mechanical Application Initiative (MAI), with a dozen partners including MacNeal-Schwendler Corp., Ansys Inc., Moldflow Pty. Ltd., CAMAX, and Mechanical Dynamics. That initiative is working on standards that will allow analysis, manufacturing, and other third-party software to use Autodesk CAD model data directly without need for any data translation. The ultimate goal: Offer "associativity" throughout the design cycle, not simply within a CAD program.
Now, associativity changes other, related facets and dimensions of a design when one variable is altered. Autodesk says its MAI will provide the same convenience across software packages. So, for example, when a design measurement is changed, the analysis mesh and numerical-control data could be automatically updated as well.
Major savings. The ability to easily move CAD data between different software packages goes far beyond mere convenience. At Hewlett-Packard, the company's own manufacturing divisions slashed 40 to 60 percent from product-development time after adopting an "Open Environment" architecture, according to Cliff Gumkowski at HP.
Open Environment and Engineering Data Exchange, developed for use within the company, eases the flow of data among different software packages and sites, he explains. Now, it's being made available to outside customers.
"It's no longer the features of a CAD product" which convinces engineers to buy, Gumkowski says, but "the capability to take data in and out." IGES, a translation format used by many software packages to move data around, often does not retain all the data richness of a 3-D model.
That can be particularly vexing for a company replacing one CAD system with another. Generally, to bring in CAD models to another software package, you need feature definitions, constraints, and history. Typical translators don't include those attributes, says HP Product Manager Paul Hamilton. "With HP Solid Designer, you don't need them," he says. "You can modify the model as if it originated in Solid Designer."
Hendry Telephone Products, Santa Barbara, CA, recently moved from a 2-D CAD system and separate sheet-metal package that could only model one part at a time, but not simulate assemblies. Hendry adopted HP's Solid Designer CAD software and became a beta-tester for an HP in-house sheet-metal package that would not only model all parts but put them together in an assembly to check fit. Data easily moved from design to manufacturing, he says.
"We probably saved well over 50% of design time," says Chris Chapa, LAN administrator at Hendry, which makes parts for the telecommunications industry. "We know now when we go out and punch it out in the shop, those assemblies are going to fit together." The system also allows Hendry to read in 3-D CAD files from customers.
Tom Danowski, designer/CAD system administrator at Safety-Kleen, Elk Grove, IL, says moving data among different formats is key to dealing with suppliers. After his department was cut from 11 people to four, he notes: "We rely more heavily on outside vendors and resources." A prime factor in selecting a new CAD system--Cadra from Adra Systems--was the ability to move DXF files in and out, as well as its built-in translators for various other formats. Safety-Kleen designs large sinks, vats, and drums for the auto-repair industry.
Broadening standards. Several companies that have developed standards for the industry now seem willing to share them with other vendors. Spatial Technology recently said that it would publish specifications for its popular ACIS(R) SAT 3-D modeling data format, allowing outside companies to develop ways to share ACIS data among applications. Details are available on the Internet at ftp.spatial.com (anonymous ftp) and http://www.spatial.com/spatial (World Wide Web).
Intergraph Corp., meanwhile, has developed a set of engineering-specific extensions to Microsoft Corp.'s OLE (Object Linking and Embedding) that is available throughout the software industry.
Conventional OLE allows Windows users to easily "cut and paste" drawings and other objects between different applications. OLE for Design and Modeling "makes OLE understand geometry," explains Mike Hamman at Intergraph. This will let engineers take 3-D CAD models developed in a Windows-based application, and copy them into any other Windows software package--keeping the geometric information intact.
OLE for Design and Modeling supports transparent and translucent objects, multiple objects in a single model, multiple simultaneous views, and combines 2-D in 3-D settings or vice versa.
One obvious use for the standards: Moving models from one engineering package to another, says Kim Corbridge at Intergraph. But engineers could also link their models to spreadsheet calculations--or send the models into Purchasing Dept. software.
David Titzler, senior mechanical engineer at Hauser Inc., Westlake Village, CA, believes things are improving for engineers using multiple software packages and platforms. "There are some standards in place," he notes. "We are having some good luck" transferring data from different software.
Hauser, a consulting firm, needs to take CAD models developed on a wide variety of CAD packages used by its customers. The company itself uses CAD software from HP, Parametric Technology, Ashlar, and Autodesk, among others. "The ability to smoothly go between CAD packages is always going to be of value," Titzler says.
Down the road, industry-watchers say, the STEP initiative may come up with standards for an effective, "neutral" data-transfer format. Many software companies have pledged to incorporate STEP in future releases as the initiative evolves.
"Useful standards are emerging, but slowly," says Jenkins at Daratech. "Major vendors may move more quickly and with more directiveness."
About the Author(s)
You May Also Like