Ask The Search Engineer 12865
December 13, 2004
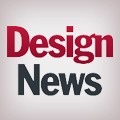
Infrared heat . . . Double-sided adhesive foam . . . Ultrasonic sensors . . .
Dear Search Engineer: I am looking for an infrared heat source that can be used in an industrial application for melting vinyl at 500F. The issue is not producing UV at the same time so that it does not discolor the vinyl. I've been down the path of ceramic heaters, quartz lamps, etc. Any suggestions on where to go from here? -N.E., Dillsburg, PA
Dear N.E.: All heat sources will generate some UV. The higher the temperature of your heat source, the more UV will be generated. You may need a lower-temperature heat source over a larger area or longer time. You could also get either UV-absorbing filters to remove the UV by absorption or dichroic filters to reflect the UV back to the source or away from the vinyl.
Dear Search Engineer: I need to get a reasonably clean hole in some rubber balls without resorting to molding it in. The balls already exist and there is no time to remanufacture. They are about 25 mm in diameter and the hole size needed is about 3-4 mm. Any suggestions on how to do this?-B.S., DN reader
Dear B.S.: I suggest you chill the rubber using dry ice or liquid nitrogen. Then drill (in a drill press or milling machine) using a sharp, shallow-angle drill bit at a slow rpm. Be careful when you fixture the ball; when it is chilled, it may be susceptible to cracking. Or, for other detailed directions, start by obtaining a suitable diameter thin-walled brass tubing from a hobby shop. Sharpen one end (crude method: chuck the other end in a drill press, and use a single-cut file tipped 15 or 20 degrees off vertical to make a shallow taper. Use a pocketknife to clean out the internal burr that results.) Now use the tube to "core drill" the rubber balls. Water is usually a decent lubricant for rubber. A little experimentation will tell you whether it is needed at all. Cutting or grinding a small hole into the side of the tube 30-40 mm above the cutting edge will allow dripping water inside the tube.
If you can find a piece of solid material to fill the chucked end, you'll get less distortion of the tube. Grinding three flats roughly 120 degrees apart on an Allen-head capscrew, down to flush with the shank, gives you a removable filler that clears the chuck jaws. You'll need it removable so that you can push out the core from the ball after drilling.
Drill a through-hole in a piece of material (wood, aluminum, etc., clamped to your drill press table), making a close fit on the O.D. of the tube. Without moving this piece, make a large enough counterbore or countersink to locate the ball. Drilling with the prepared tube will be along a diameter, and you can tear down and set up again using the pilot hole and tube to position the fixture. If needed, a similar piece can be inverted above the ball to serve as a hold-down. A couple of guide pins flanking the ball will align it, and fingers are probably enough for clamping in this size range. If not, it shouldn't be difficult to find a better means. I'd advise having a tiny amount of clearance in the upper part's pilot hole, over the tube, but it may still provide additional guidance for the core drill. Obviously, if you need the hole offset from center of the balls, simply move the fixture base by that amount, and add a second pilot hole to handle guidance and setup duties.
Dear Search Engineer: I want to build my own car with pipe structures. It can be circular tubes or square/rectangular tubes. How can I join these tubes other than normal welding methods? Any suggestions on better methods so that structural performance of the car will not be hampered (i.e., structural rigidity, tortional stiffness, etc.). -A.D., India
Dear A.D.: I suggest you check out Modu-Tek extruded aluminum beams (www.tekno.com/indexproducts.html), which come in various rectangular cross sections. The product line includes a variety of fastening means. Otherwise, try contacting the North East Sustainable Energy Association (www.neses.org). They run the American Tour De Sol, a road rally for alternative cars. Someone there should be able to point you to a team that has built a car using exactly the methods you have described.
Dear Search Engineer: I am looking for a conductive silicon adhesive to mate black chrome-plated metal to NiAu-plated land on PCB, and withstand =500 cycles of temperature cycling at -40 to +125C. Any suggestions? -D.D., DN reader
Dear D.D.: One candidate to try for the conductive silicon adhesive is Master Bond's Master Sil 705S (http://rbi.ims.ca/3860-524). Or Zymet (www.zymet.com) makes a silver-filled conductive silicone adhesive also.
Dear Search Engineer: I am currently using a double-sided adhesive foam (polyethylene foam) to install a three-way valve (its label side) onto an aluminum-mounting bracket. But after some time, the foam peels off from both parts. Could you suggest other double-sided adhesive foams that bond well on most surfaces? -R.A., UK
Dear R.A.: If you have not already done so, examine the Very High Bond (VHB) double-sided tapes from 3M, as well as the 3M 300 Series Hi-Tack. The tapes are offered in a variety of foam backings and adhesives.
Dear Search Engineer: I need the math process for the circumference of a helical trapezoidal thread (1) revolution. I must cut a pattern and need the exact length, without using my CAD program. Any suggestions? -S.L., New Albany, IN
Dear S.L.: Merely "unwrap" the thread and the answer will be obvious. The length of the helix thread is really the hypotenuse of a triangle whose other sides are the circumference of the round part and the lead distance formed by the pitch of the thread. Therefore the formula would be:
helix length = square root of [(PI x diameter)^2 + (pitch length)^ 2].
Dear Search Engineer: We are building fuel tanks out of sheets of aluminized steel (carbon steel with an aluminum coating, sort of like galvanized). I am trying to find a way to improve the appearance of the welds on these boxes as they are. The welds tend to get a surface rust immediately while the aluminized sides of these boxes look great for years. The rust has never been a threat to the structural integrity of the tank; I am simply trying to improve the appearance. From a cost standpoint, I would like to avoid painting or powder coating the entire tank if possible. Any suggestions? -G.M., DN reader
Dear G.M.: Try using a different alloy for the weld filler metal-possibly one with a high nickel or chromium content. Or try electroplating the seams and some adjacent areas by dipping into the electrolyte only the welds. Or a third option is to make the tanks, aluminize the outside, and finish with epoxy coating the inside.
Dear Search Engineer: I've designed a vibration fixture. The forcing frequency range was to be 10-2,000 Hz. The mass of the UUT is about 20 kg. The mass of the fixture was to be no heavier than 25 kg due to shaker limitations. After considering all the constraints, I designed a fixture and analyzed its mode shapes and resonant frequencies. In my analysis, I constrained the fixture by assuming the counterbore faces in the bolt holes were fixed. Based on my analysis, I predicted a fundamental resonance at 2,200 Hz, where the fixture was constructed. Upon testing the fixture on a shaker, a fundamental resonance of 1,800 Hz resulted. Why does my FE result differ so much from the actual result? I reran the model with no constraints, and my FEA program was able to predict a third fundamental at 1,800 Hz resonance. In fixture design, how should the FE model be constrained to yield the correct results? -A.S., CA
Dear A.S.: Assuming the bolt holes you mentioned are for mounting the fixture to the shaker, the problem is that your FEA model constrains the fixture at points where the shaker is moving it. If you mount a small accelerometer on one of the bolt heads and drive the shaker with a sinusoid of slowly varying frequency, what you will observe should be a minimum response at 2,200 Hz. That is the frequency that your model predicts for the case where the bolt holes do not move.
The proper way to model the vibration fixture is to remove all constraints, divide the moving mass of the shaker armature by the number of mounting bolts, and add the resulting mass to the vibration fixture at each of the bolt holes. Generally speaking, unless you have a very lightweight flexible structure clamped or welded to a large block of steel, a true rigid constraint cannot be achieved easily.
Dear Search Engineer: I'm looking for an encoder to be mounted on a 1/18 motor shaft to measure speeds from 0 to 3,500 rpm and to feed back to a PLC analog card. Any suggestions? -F.L., DN reader
Dear F.L.: You can try Agilent's Analog Small Optical Encoder Module, HEDS-9710, HEDS-9711. To view the Agilent Technologies data sheet, go to http://rbi.ims.ca/3860-525.
Dear Search Engineer: Has anyone developed a method to induce a current (power source) from the flow of methane (natural gas) in a pipe? -C.J., Sechelt, BC, Canada
Dear C.J.: While I don't know know if you are asking about an induced electric current or not, there are thermoelectric generators used to provide power from natural gas heat sources. These are generally used at remote locations such as well heads to power instrumentation where there is no other power source. Take a look at these three websites for thermoelectric generators: www.pgiint.com/ThermoElectric.asp, www.globalte.com/introduction.html, www.remote-site.com/thermo.html.
Dear Search Engineer: I work as an electrical engineer in our trim shop. Our bodyshop has asked us to do door flushness checks on the painted vehicle. I have lots of experience with vision systems and I know what a challenge this would be. Do you know of anyone using ultrasonic sensors for the above application? My plan was to use two sensors wired to analog input cards. The sensors would basically subtract each other for the net difference. Any thoughts? -B.G., DN reader
Dear B.G.: One of our readers responded that his experience with ultra sonic sensors has been less than optimal. He writes: It is difficult to aim them precisely; they are prone to interference from each other's waves; the sound waves can be deflected if the target is not square with the waves; and did I mention you can never be sure with any precision what exactly they are hitting. I would suggest using a visible laser with an analog output.
Visible lasers are available with many different resolutions and ranges, are not really affected by color, and give a good signal off of just about everything that they hit. You may want to try some of the lasers from a company called Keyence (www.keyence.com); You could also get acceptable results with some of the lasers manipulated by Baumer, particularly Type OADM (www.baumerelectric.com).
About the Author(s)
You May Also Like