Application Digest 7738
January 5, 1998
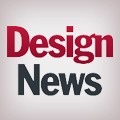
Installing cables in flexing carriers
Gerald Pochurek, Director of Engineering,
Olflex Wire & Cable, Fairfield, NJ
Whether using metallic or non-metallic cables,a properly installed cable-carrier system can in-crease cable life by 5 to 10 million cycles.
To prevent cable twisting and ensure free movement within the carrier, it is important to eliminate any residual twist or bends in cable. After unwinding the cable from the spool or reel, manipulate it by hand until it lays flat for a couple of hours. Then, wrap each end with masking tape and mark the top surface for alignment in the carrier.
Dividers, placed between cables in a flexible track, prevent interference. If installing hoses with electrical cables in the same track, use steel-reinforced hoses for both air and hydraulic hoses to prevent pressure expansion. Allow spacing of at least 10% of the cable diameter between cables, and position all cables in the neutral area of the cable carrier.
Clamp both ends of the cable to the cable carrier at a distance equal to 15 times the largest cable's diameter from the point where the cable begins to flex. Finally, run the carrier through several cycles to verify that no interference is occurring.
To speak with an Olflex Wire & Cable Inc. applications engineer, call (888) 456-FLEX or FAX (973) 575-1267.
Hollow-shaft encoders reduce motion-control costs
Mike Onessimo, Applications Engineer, Dynamics Research Corp., Wilmington, MA
Traditional mechanical mounting for a shafted optical encoder used in a motion-control system requires a bracket to hold the encoder, a coupling between the encoder and motor shafts, and assembly labor to mount components and align the shafts.
A hollow-shaft encoder, such as one of the HS hollow-shaft optical encoders made by Dynamics Research Corp., eliminates the need for a mounting bracket because the encoder is mounted through an integrated flex spring. The coupling between the encoder and motor shaft is also eliminated, because the encoder hollow-shaft bearings are directly coupled to the motor shaft by a keyway, split-collar lamp, or set screw. The flex spring eliminates any loading created by shaft misalignment.
Eliminating the bracket, the coupling, and the labor required to install these parts and align the motor and encoder shafts, reduces overall cost. Using a hollow-shaft encoder also allows a much more compact mechanical design.
Available in five diameters from 1.5 to 3.5 inches, the HS family of hollow-shaft encoders also provides a wide range of electrical outputs, hollow-shaft diameters, resolutions, and mechanical mounting configurations.
To speak with a Dynamics Research Corp. applications engineer, call 800-323-4143, or go to http://www.drc.com.
About the Author(s)
You May Also Like