Two Unlikely Failures Contributed to Southwest Airlines Incident
Metal fatigue may have caused a turbofan blade in the aircraft’s engine to crack and fly apart, hitting the fuselage.
April 20, 2018
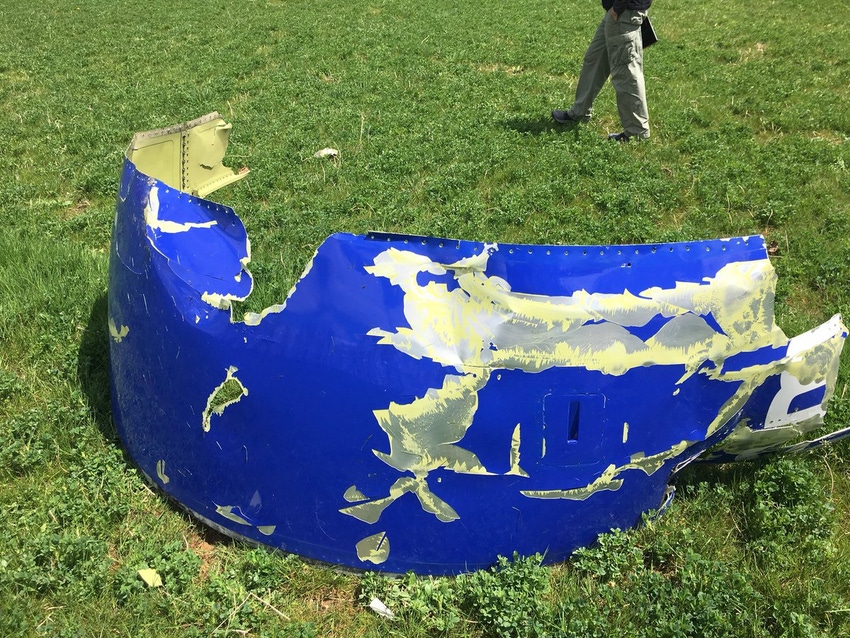
Investigators don't yet know the cause of Tuesday's fatal incident on a Southwest Airlines flight. But they do know that two successive, unlikely events contributed to it.
First, a fan blade on one of the Boeing 737’s engines cracked. That, in itself, is rare. Then the engine’s cowling failed. “It was a very unfortunate combination of factors that caused it to be this bad,” Sammy Tin, a professor of materials engineering at Illinois Institute of Technology, told Design News. “Usually, when a fan blade goes, the housing on the engine is able to contain the damage. In this case, there was also a failure of the cowling. It came off as well.”
NTSB investigators examine the CFM56-7B engine that broke apart during flight this week. (Image source: NTSB) |
The incident occurred during a flight from New York to Dallas on Tuesday morning. Passengers on the Boeing 737-700 said they heard a loud boom. Oxygen masks dropped and shrapnel from the damaged engine slammed against a window, breaking it, according to The Wall Street Journal. At one point, passengers held onto a woman in an attempt to keep her from being sucked out the broken window. That passenger later died.
The crippled plane made an emergency landing in Philadelphia. The engine’s cowling was found on the ground about 70 miles northwest of Philadelphia.
The engine, a CFM56-7B built by CFM International, is a type that is said to have logged more than 350 million miles of safe travel. On Tuesday, however, it broke apart while the plane was cruising at about 32,000 feet. Investigators from the National Transportation Safety Board found two cracks in one of its 24 blades. One crack was located near the point where the blade attached to the engine’s hub; the other was about halfway up. NTSB chairman Robert Sumwalt said that the interior crack was “certainly not detectable from looking at it from the outside,” according to CNN.
Experts said it’s not unusual for such cracks to be located in spots that aren’t easy to see. “If it’s not in a direct line of sight, then they may not necessarily have seen it during inspection,” he told us. “In some cases, to see a crack, they may have to remove the blade to inspect it.”
Within 24 hours of the incident, NTSB investigators had concluded that one of the two cracks showed signs of metal fatigue. Metal fatigue, a weakening of the material caused by high cyclic loading, is a phenomenon common to virtually all metal structures as they age. If not detected, it can cause parts to yield at stresses below their designated tensile capacity, which may have happened in Tuesday’s incident.
"Fatigue failures are probabilistic events," Tin said. "They may not always occur, but the probablity of them occurring becomes higher after a longer number of loading cycles."
Tuesday’s incident was not the first case of metal fatigue on a CFM56 engine. A similar failure happened in August 2016, when a Southwest Airlines jet traveling from New Orleans to Orlando made an emergency landing after a fan blade separated from a CFM56 engine and ripped a foot-long hole in the plane’s fuselage. The Federal Aviation Administration subsequently proposed ultrasonic inspections of similar fan blades, but the directive hadn’t yet been finalized before Tuesday’s incident.
“Having it occur back to back, about one-and-a-half years apart, means it has to be looked into further,” Tin said. “What’s raising eyebrows here is the fact that there have been two failures.”
In a statement, CFM International wrote that it is deploying about 40 aircraft engine technicians to support Southwest Airlines’ inspection of the CFM56-7B engine. It also said that ultrasonic inspections are being conducted on a “population” of fan blades.
According to Professor Tin of Illinois Institute of Technology, “Fatigue failures are probabilistic events. They may not always occur, but the probability of them occurring becomes higher after a long number of loading cycles.” (Image source: IIT) |
After this week’s incident, investigators cited the possibility that the metal fatigue may have been caused by factors other than aging and cyclic loading. “The NTSB mentioned that it may have been due to some kind of inclusion or defect that was trapped in the material during manufacturing and was never caught,” Tin said. “That can accelerate the rate of fatigue crack growth.”
If the metal fatigue was caused by a manufacturing defect, it wouldn’t be the first such case. In October 2016, an American Airlines flight experienced an “uncontained failure” of a GE-80C2B6 engine during a take-off roll at O’Hare Airport in Chicago, according to the NTSB. The resulting explosion and fire was traced to metal fatigue cracks in the engine’s metal-alloy disk. Metal fatigue accelerated the rate of the crack’s growth, leading to the failure, the NTSB concluded earlier this year.
A piece of the engine housing was found about 70 miles northwest of Philadelphia. (Image source: NTSB) |
Tin said that such incidents serve as teaching moments for design engineers. When designing, he said, engineers need to do proper fatigue analysis up front to ensure that components are able to meet their life requirements. “Usually, there’s scheduled inspection and maintenance, so that before a part fails catastrophically, it’s removed from service and replaced,” he said. “But before that, design engineers always need to remember that what they are doing now may have an impact 10 or 15 years down the line.”
Read More Articles on Materials Technology
Silicon Supplants Carbon to Improve Li-Ion Batteries
Will the Supply of Lithium Meet Battery Demands?
This Flexible Piezoelectric Fabric Turns Kinetic Energy into Electricity
Nickel Is the New Key to Recycling CO2 Emissions
Senior technical editor Chuck Murray has been writing about technology for 34 years. He joined Design News in 1987, and has covered electronics, automation, fluid power, and auto.
About the Author(s)
You May Also Like