Coatings ease out sticky parts
December 4, 2000
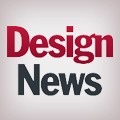
Whether die-casting, squeeze casting, or semi-solid metal casting, the interface between material and die surface impacts product pricing and overall profitability. That's because the interface determines the size, shape, and texture of the part. If any of those three characteristics are off spec, the factory will have to machine, grind, or drill the part, driving up costs.
Many die casters use a surface modification such as a coating to provide lubricity and protection and avoid those problems. But with so many coatings and surface treatments to choose from, how do you decide which way to go?
When Premier Tool and Die Cast Corp. (Berrien Springs, MI) faced decreasing productivity due to constant solder build-up in one of its 600-ton aluminum die-casting machines, Project Engineer Jeff Brennan decided to try some coatings. After a production evaluation of eight different coatings on a 16-cavity die as part of a North American Die Casting Association study, Brennan determined FNC (ferritic nitrocarburizing) from Dynamic Metal Treating Co. (Canton, MI) was the most cost-effective surface treatment for this particular motor-mount insert application.
|
But that's not to say the other coatings didn't reduce soldering. In fact, according to Brennan, any coating is better than no coating at all in his application, with some showing more promise than others in terms of extending die life. But it's no surprise that economics was the deciding factor. "At a cost of $2.50/lb, FNC provides an average die life of approximately 20,000 to 25,000 shots," explains Brennan. "The best coatings [CrC and VC] extended die life to the 30,000-shot range, but that's not enough to justify 10 times the cost or more."
Easy ejection. Premier's problems weren't solely soldering related, however, so Brennan can't attribute the extended life to any single factor. "It was the core redesign and coating combined," he says. In fact, the problem encompassed many issues such as cooling, gating, and load bearing capacity of the ejector pins. "We ended up redesigning the core dramatically to make ejection easier," he explains, "because we had a lot of problems due to process and design related issues."
For example, the cores had to be removed every shift for polishing. Cores broke almost on every run. The die required removal for maintenance every 5,000 shots. Heat checking was a problem in the cavity. Excess flash was a problem at the ejector pins. "All things that take away from the bottom line," notes Brennan. Addressing these issues, the redesign included:
Replacing the ends of the casting and center hole with a 2-inch diameter core to eliminate head breaking
Putting a 1/8-inch bubbler into each core with high-flow cascade
Adding a 1/8-inch copper pin to extract heat from the core body
Increasing the ejector pin surface area by 50%
Moving the pin closer to the core body
|
Only after the redesign did Brennan send the cores off to the Die-Casting Research team at Ohio State University for coating as part of the NADCA-sponsored study. NADCA Coatings and Surface Treatment Task Group members had eight suppliers pick their best coating/surface treatment candidate to help solve Premier's problem.
Coating or surface treatment selection for die casting depends on how well the material protects the die steel from the molten aluminum, which has an affinity for the iron in steel and tends to dissolve it. In Premier's process, the alloy is at 1,200-1,300F and reaches velocities of 1,500 inches/sec inside the cavity.
"It's one of the most corrosive alloys," says Brennan. "And when you plunge it into a die cavity with a hydraulic cylinder at high temperature, pressure, and velocity," he explains, "it adheres to the core as it's trying to break down the iron. The resulting solder build-up makes the parts resist ejection, contributing to part, core, and ejector pin damage."
A suitable protective barrier requires:
Adequate adhesion to the substrate for longer life
Good mechanical properties (hardness, ductility, fatigue strength, shear strength, and ultimate tensile strength)
Corrosion and oxidation resistance
Shock resistance-thermal and impact
High thermal conductivity to dissipate heat from the interface quickly
Dimensional stability
Thermal properties compatible with the substrate to minimize interface stresses
Compatibility between the coating and substrate
Low surface wear
It's important to understand the fundamental difference between the roles a coating and a surface treatment play in modifying the substrate's surface characteristics. Coating deposition places material with desired properties onto a surface. Examples include PVD (physical vapor deposition), CVD (chemical vapor deposition), PCVD (physical chemical vapor deposition), TRD (thermo-reactive deposition), and thermal spray. In contrast, surface treatments actually alter the chemistry and/or microstructure of the surface. Examples include carburizing, nitriding, cold working, and work hardening.
With two cavity cores in each die using the same coating/surface treatment, engineers at Premier provided on-site observation of the number of shots, condition of cores before cleanup, polishing frequency and related downtime. "If problems came up during production," says Brennan, "we stopped the machine, and visually inspected the cores after polishing with emery paper. Then, we decided if a particular core pin was fit to use in production again."
Coating test conclusions. After completing coating performance evaluation during actual production, Brennan deduced some good general information about the tested coatings. Testing revealed that carbides in general performed better than other compounds. FNC, the only carbide surface treatment tested, is applied with a low-temperature nitrocarburizing process. While one of the FNC cores was removed from service after only 14,932 shots, the other FNC core survived 32,269 shots and would still clean up, according to Brennan.
The VC coating applied with TRD in a high-temperature diffusion process performed similarly to the FNC coated cores. One survived 32,269 shots, and the other was pulled from service after 14,932. Both PVD-applied coatings, CrC and BC, are low temperature sputtered coatings. However, performance wasn't the same. "CrC survived over twice as many shots [32,269] as BC, and would still clean up," says Brennan. BC was pulled after 14,932 shots.
For the nitride test category, ion nitriding (IN) is the only coating that falls under surface treatment. However, IN coatings from two suppliers were tested. Core 3, treated with IN1, chipped in the first run and was removed from service after 7,330 shots. At 32,269 shots, core 4, also treated with IN1 may have had a failed coating, according to Brennan. However, IN2's performance was different with core 7 failing after 21,679 shots. And at 32,269 shots, core 8 had serious buildup that may not clean up, according to Brennan.
Premier process conditions Machine size: 600 ton |
In the category of PVD nitrides, CrN was the only one applied by a low-temperature arc evaporation pro- cess. After 7,609 shots, Brennan says, the core may not clean up. CrN2, which is a combination of shot peening and CrN (arc evaporated PVD coating), belongs in the duplex coating category. Core 9 broke at 2,000-3,000 shots and core 10 survived 32,269 shots, but Brennan says it's not likely to clean up.
Looking to the future. "All these coatings are single layer coatings," Brennan says. "As a company we are looking into extending die life even further in the future using multi-layer coatings." Premier maintains involvement with NADCA, and related work at the Colorado School of Mines.
"Preventing the onset of coating failure is the biggest challenge," says Brennan. "When the coating starts to break down, the aluminum goes underneath and tears it up," he says. According to Brennan the more expensive coatings and surface treatments, "may be worth spending $50 on one of these cores, if we could get it to last 100,000 shots."
Technique | Suppliers | Coating/Surface Treatment | Code | Core#s Treated | Coating Thickness | Hardness | Website | Enter # |
---|---|---|---|---|---|---|---|---|
|
|
|
|
|
|
|
|
|
|
|
|
|
|
|
|
| |
|
|
|
|
|
|
|
| |
|
|
|
|
|
|
|
|
|
|
|
|
|
|
|
|
|
|
|
|
|
|
|
|
|
| |
|
|
|
|
|
|
| ||
|
|
|
|
|
|
|
|
|
About the Author(s)
You May Also Like