A Soldering Conundrum
May 28, 2014
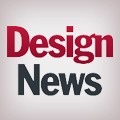
Some years ago, I worked for a defense contractor as a product support engineer. The responsibilities of this position were to assist the manufacturing engineers whenever there was a problem with the product that they could not solve without a design change.
The program was a "build to print" one, meaning that we received a set of very complete drawings and documentation from the customer and were not permitted to deviate from what we were sent in any way without approval. If a design change was needed, I would prepare an engineering change request and send it up the chain to the design agency and ultimately to the customer for approval. Approval of a design change was a lengthy and cumbersome process, taking about a year from start to finish, so that was not the preferred option. It was much easier to modify our internal processes as long as it did not violate any requirement in the documentation package.
One problem that comes to mind was brought to my attention by one of the assembly operators. She was responsible for soldering each end of a very thin flexible aluminum ribbon into a narrow slot in a gold collet (the collet weighed a few milligrams). These ribbons were used to provide power to a module without adding a mechanical constraint. The ribbons were plated with nickel and pre-tinned in the area where they went into the slot so that the solder would wet the joint easily.
The operator had been making this difficult solder joint for a long time and was very good at it. She said a new lot of collets that she recently received didn't solder well at all -- the solder just beaded up and would not flow into the slot and surround the ribbon. The manufacturing engineer had already checked the soldering station calibration, the traceability of all material lots, the C of A for both the tin-lead eutectic solder and the gold alloy, the incoming inspection reports, the nickel plating logs, and the RMA solder flux expiration date. Everything was in order.
The only smoking gun was the new lot of gold collets, but they appeared to be the same as past lots in every way. I asked the operator for a demonstration of the problem and found a few parts from an old lot so we could compare them. Sure enough, the old lot soldered fine but with the new one the solder just beaded up.
I asked Purchasing for permission to contact the supplier, a precious-metal machine shop. This was allowed, as long as I had a purchasing representative on the call (ensuring no shenanigans from those pesky engineers), and I asked the supplier whether they had changed any of their processes. They had to research this, but called back later to say that, yes, they recently purchased a new wire EDM machine and had cut the slots in the new lot with it, rather than using a slitting saw, the old method. They had been able to reduce cost and actually improve the tolerance of the slot with the new machine, and seemed pleased. I said thanks and went off to think about it.
Nothing about the change to wire EDM seemed inherently wrong, but I thought that must be the cause. I was channeling Sherlock Holmes, who said: "… when you have eliminated the impossible, whatever remains, however improbable, must be the truth." I opened up the slots in an old-process and a new-process collet and took them to the SEM lab to get a look at the surface. The difference in the surfaces was striking in the SEM photos. The slitting saw surface had classic linear machine marks, but the EDM surface had a glassy undulating texture with some particulate spatter from the gold melting and re-solidifying during the EDM process.
We compared the effect of these surfaces by testing solder melting and wetting on a hot plate in the lab. While the machined surface was easily wetted by the solder as soon as it melted, the topography of the EDM surface prevented the solder from wetting and it just sat there as a molten bead. On the line, capillary forces would not draw the molten solder into the joint. We reworked the slots in that lot of collets in our shop, maintaining the width of the slot within the drawing tolerance, and they soldered just fine. Since there was a second source and this contract was a competitive one, we were able to maintain a small competitive advantage by keeping this knowledge to ourselves rather than requesting a design change. Instead, we modified future purchase orders, adding a note specifying "NO EDM" to prevent a recurrence.
This entry was submitted by A. David Boccuti, P.E.
Dave Boccuti has been a mechanical design engineer for more than 30 years and has worked in a number of different industries. He is currently developing disposable in-vitro diagnostic medical devices at Daktari Diagnostics in Cambridge, Mass.
Tell us your experience in solving a knotty engineering problem. Send stories to Lauren Muskett for Sherlock Ohms.
Related posts:
About the Author(s)
You May Also Like