3 Steps to Get the Most From Your FEA Modeling
October 14, 2015
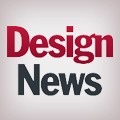
More and more design engineers today are turning to upfront computational methods like finite element analysis (FEA) to get their designs developed and products to market faster. Creating FEA models early in the design cycle not only reduces overall development time, cost, and effort, it can improve product quality and avoid costly rework during later phases. If you want more effective FEA results, consider using some of these simple but proven techniques on your next FEA model.
1.) Properly Prepare the Model
One of the most common mistakes is to directly upload every manufacturing detail into the mesh geometry for analysis. It's not necessary to include non-critical features that have little or no impact on the overall analysis (such as part numbers embedded into the surface or non-functional, decorative features). Take the time to simplify the geometry by removing and suppressing any non-critical features or parts.
Also, clean up the final geometry by getting rid of any knife edges, sliver faces, or any other complex features that have a negligible influence on FEA accuracy. When done correctly, a simplified geometry model can reduce the total duration of the FEA analysis (setup, run-time, post-processing) by 40% or more compared with a geometry model that has not been simplified.
Take great care when defining input data such as material properties, applied loads, and contact definitions and make sure that these specifications are accurate. Incorrect applied load units and inaccurate custom material properties tend to be common sources of modeling error. Also, be aware of all underlying assumptions. For example, if a force applied to a bracket is breaking the part, it makes little sense to use a linear static solver (which will show unrealistic stresses since it does not consider the nonlinear nature of the material deforming beyond its yield limit).
READ MORE ARTICLES ON PRODUCT DEVELOPMENT:
2.) Right-Size the Mesh Density
While a finer mesh with more elements yields more accurate results, it also means higher computational effort, longer solver run times, and greater hardware requirements. Conversely, a coarser mesh runs faster and requires minimal hardware but typically produces more basic results.
To get the best of both worlds, use a combination by first doing a coarse mesh during the initial analysis to ensure the FEA model is working properly. During this stage, a sanity check of the model will be the higher priority (instead of accuracy). Then, after making sure that the model is behaving as expected under the various loads, use a finer mesh only in the regions of concern, such as high stress gradients, sharp corners, etc.
In this way, accurate results at critical locations can be obtained without overly burdening the model with an excessive number of mesh elements. This optimizes computational effort and allows for more solver iterations during the same time period.
3.) Refine the Mesh to Minimize Errors
In many cases, meshing errors are unavoidable. However, these errors can be reduced by creating mesh independence, where the numerical solution is not dependent upon the mesh.
To create mesh independence, Srikrishna Chittur, a simulation product specialist at engineering solutions firm TriMech Solutions, recommends first refining mesh elements globally until the displacements converge. Then, progressively refine the same mesh only in the areas of concern until the local stresses converge. By refining the mesh in this manner, solution errors are usually kept to a very minimal level. To further save time, solution-based adaptive meshing techniques can be employed to automate this process.
The results obtained from FEA analysis will always be directly related to the quality of inputs, simplifications, meshing, and assumptions with the model. Taking the time to properly model and mesh in the early stages of FEA not only provides more accurate results, leading to shorter development cycles and better product performance, it can avoid lots of headaches.
Greg Jung has more than 25 years of experience designing medical equipment and electro-mechanical products for a wide variety of industries. He also served in various project management roles and has led global, cross-functional development teams for a wide variety of programs. During this time, he developed several award-winning and patented product designs. Greg holds bachelor and master of science degrees in mechanical engineering from the Georgia Institute of Technology.
About the Author(s)
You May Also Like