The Case of the Acrobatic Airplane
December 10, 2007
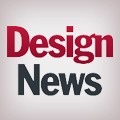
A twin-turboprop powered passenger airplane was shared by several companies. The pilot for one user attempted to lower the gear for a routine landing but found to his dismay one of the two wheels remained retracted. The pilot managed to tippy-toe in on the single lowered wheel with no injuries and only modest damage to the aircraft. It was a nice piece of flying.
The Scene of the Crime
The landing gear retraction mechanism involved an up-lock hook that engaged a pin. The hook had partly fractured and jammed so the wheel could not be lowered. The owners and users of the airplane, of course, sued the manufacturer. I was retained by the plaintiffs to determine why the hook failed.
The Investigation
Chemical analysis showed the hook to be made of a common aluminum copper alloy. Hardness measurements showed the alloy had been heat treated to a fairly high hardness or equivalently, strength. Optical microscopy on a small piece of the hook that had been polished to a mirror finish showed a sandwich construction. The core was the strong aluminum-copper alloy and both surfaces were covered by thin sheets of pure soft aluminum that provided corrosion resistance. The hook material was similar to cookware that has a copper or aluminum core for heat conduction and a stainless-steel exterior for corrosion resistance. All this was fine.
Most failures in moving parts are due to metal fatigue. The high magnification power and the ability to keep an uneven surface in focus make the scanning electron microscope (SEM) the natural tool for studying fatigue. The figure (below) is an SEM photo of a small region on the fracture surface. The cuboidal features are tiny copper aluminide particles a few ten-thousandths of an inch across. These tiny particles were formed during heat treatment to strengthen the alloy. The many dimples on the fracture surface are evidence of a generally ductile fracture, which is, of course, desirable.
The roughly parallel lines just below the particle in the middle are so-called fatigue striations. A crack started at the particle and then progressed a minute amount each time the hook was loaded during retraction. Finally, the crack in the figure and other cracks so weakened the hook that it partially broke, causing the hang-up during landing.
The Smoking Gun
Many airplanes of the same model used the same hook without incident. So why did this particular hook fail? Examination of the failed hook with a simple hand lens gave the answer. The fracture was next to a hole that had been reinforced by a washer spot-welded in place. The spot weld was defective in burning a hole through the bracket. Fatigue cracks started at this weld defect and ultimately caused the accident.
The manufacturer had an extensive failure analysis done on the bracket that at first look seemed to be of high quality. The report showed even clearer fatigue striations than my pictures. Yet, the report explicitly denies any evidence of fatigue failure. I found this denial incredible.
I told my story in Federal Court in Boston sufficiently well that counsel for the manufacturer asked me to work for that company in any further cases. I found it a bit amusing that the request was made in the men's lavatory. Sometime later I told the story to a woman lawyer who took umbrage. Her remark was, "There are entirely too many deals going down in men's rooms." She had a point, but redress may be difficult. Female professionals have fairly well eliminated the men-only clubs and restaurants where business was once discussed in their absence. Men-only lavatories represent a bit trickier problem.
About the Author(s)
You May Also Like