Aerospace-Grade Composites Will Repair Themselves
May 12, 2014
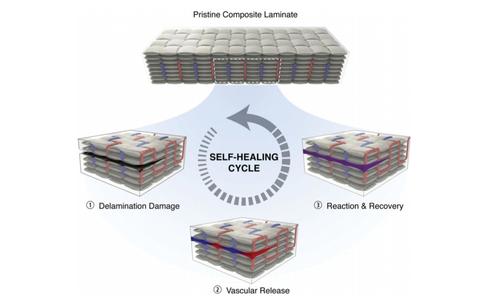
We've talked a lot on the comment boards about the problems of repairing fiber-reinforced composites, especially pricier composites like the ones used in aerospace. Wouldn't it be cool if they could just repair themselves? That may not be such a wild idea. Engineers at the Beckman Institute for Advanced Science and Technology think they've found a way to do that.
A team led by professors Nancy Sottos, Scott White, and Jeff Moore in the Beckman Institute's Autonomous Materials Systems Group at the University of Illinois at Urbana-Champaign have invented a system of three-dimensional capillary microchannels carrying two different reactive fluids throughout fiber-reinforced composite materials such as fiberglass. The two fluids (an epoxy resin and a hardener) are contained in two vascular networks isolated from each other. When the composite is damaged by delamination, sections of the two networks at the damage site break apart, and the liquids mix and polymerize to heal the composite.
As the team points out in an Advanced Materials article describing their work (subscription required), one of the biggest obstacles to greater use of fiber-reinforced composites in automotive and aerospace structures is the difficulty of detecting internal damage that can quickly propagate and cause delamination problems. There's been a lot of progress in self-healing polymers, such as the ones used for a composite's matrix, but that hasn't been translated into self-healing techniques for an entire fiber-reinforced composite structure.
The researchers inserted sacrificial polylactic acid monofilaments infused with the catalyst fluids into the interior layers, or plies, of an aerospace-grade fiber-reinforced textile structure -- a process compatible with composite manufacturing. The resulting preform was turned into a structural laminate using a vacuum assisted resin transfer molding process. Vaporizing the monofilaments created the microchannels. Surprisingly, the team reports, this process does not degrade the composite's inherent fracture properties.
The team tested the vascular network system over multiple delamination fractures and healing cycles, using two architectures: a herringbone-patterned network and an isolated parallel configuration. In the herringbone pattern, the system delivered greater than 100% recovery of the material's resistance to fracture after delamination. The researchers were surprised to discover that, after each cycle of damage and healing, a greater load was required to propagate a crack in this architecture. The isolated parallel configuration fared much worse. The researchers wrote that the herringbone pattern's better performance was probably due to better dispersion of fluid throughout the fracture plane.
This research was supported by the Air Force Office of Scientific Research; the Department of Homeland Security Center of Excellence for Explosives Detection, Mitigation, and Response; and the Army Research Laboratory.
Related posts:
About the Author(s)
You May Also Like