To Find the Optimal Prototyping Method, Start by Asking the Right Questions
Not too long ago, almost all plastic prototypes were either machined, hand fabricated, or cast. Many more options are available today, but if a prototyping method is misapplied, the results may lead to erroneous conclusions. Follow these recommendations to avoid such missteps.
February 7, 2021
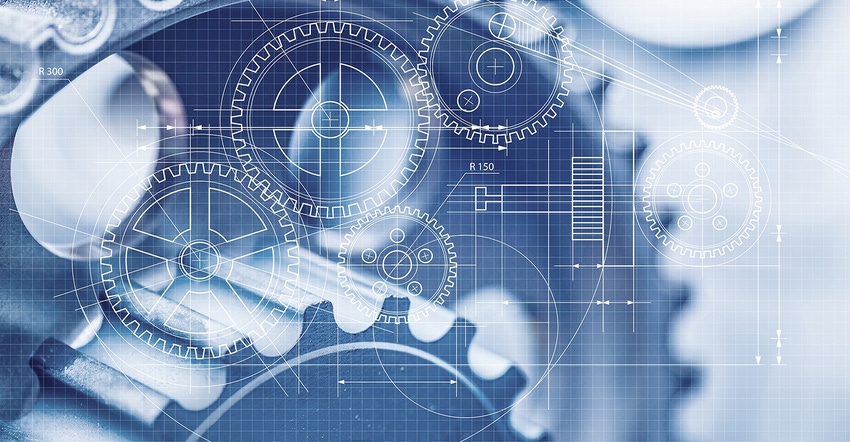
A critical phase during product design and development is verification of your design. Design verification can be attained either by simulation or prototyping. Prototyping is usually the preferred method for design verification for smaller plastic parts because of its cost effectiveness, accuracy, and convenience.
Not too long ago there were only two prototyping options available to designers and engineers — machined/hand-fabricated prototypes or prototype injection molded parts. Today, many more options are available, the most popular of which is 3D rapid prototyping. However, every prototyping method has its advantages as well as limitations. This article will review the various plastic prototyping options based on their advantages and disadvantages to help you decide which method is best suited for your needs.
Below is a list of currently available plastic prototyping methods:
Rapid prototyping — 3D part creation directly from CAD files. The top three technologies are FDM (fused deposition modeling), SLA (stereolithography), and SLS (selective laser sintering)
Handmade/fabricated
CNC machining
Casting — polyurethane, epoxy, or silicone
Injection molding — temporary tooling
Vacuum forming
Composites
Selecting the best option should be based on your requirements. A suggested list of important considerations include:
Purpose of prototype
Aesthetic requirements
Lead time — turnaround time
Plastic manufacturing process
Tolerances
Level of detail
Material properties
Quantity of prototypes required
Size of parts
Cost
Degree of clarity/color
Parameters to be tested or verified
Once upon a time . . .
Not too long ago there were very few options for creating plastic prototypes. Approximately 25 years ago, all plastic prototypes were either machined, hand fabricated, cast, or, to a very limited extent, injection molded using temporary tooling. There were no other options.
Fabricating a plastic prototype was extremely expensive, time consuming, and highly inaccurate. Only a very limited group of shops offered prototype injection molding, which was very expensive coupled with long lead times. This option was rarely utilized. Most plastic prototypes, therefore, were hand fabricated or, in some cases, CNC machined.
We must also remember that designs were being detailed predominantly in traditional 2D, since 3D CAD was still in its infancy. In those days, 3D CAD was mostly wire frame or very primitive solid modeling. Engineering “production-like” prototypes were hand fabricated based on a manual interpretation of 2D drawings. This often resulted in significant deviations from the prints because of the model maker’s interpretations or errors, and the limitations of the tools. Designers patiently waited for weeks and many times months for the prototype, which was always a bottleneck in the design process. It was a nail-biting experience, since one never knew how the design would turn out. In addition, one always questioned the accuracy of the model, never knowing if the model maker fudged the design that would camouflage errors until the parts were molded.
Fast forward to 2021
Today, 3D CAD modeling, computer simulation, and many prototyping options have exponentially accelerated the design process. Projects that at one time required a year to develop can now be completed in a month or two, and sometimes in weeks! 3D CAD models can now be accurately replicated with all the subtle details including draft, radii, embossed logos, and dozens of other critical features without any human interpretation or error. Of course, this paradigm change is a result of 3D CAD, 3D printing, and CNC machining. However, if any of these prototyping options are misapplied, the results may lead to erroneous conclusions. Designers should select a prototyping method best suited to their requirements. I will review these prototyping options based on the 12 previously stated considerations.
Purpose of prototype
Before you decide on a prototyping method, you should first ask yourself: What is the purpose of the prototype? Prototypes are used for many different reasons. For example, you may need a realistic-looking, non-functional model to present to marketing or sales. This model must have the correct surface finish, colors, graphics, and materials to accurately represent the final production design so viewers can evaluate the appearance. In other situations, your prototype will be subjected to harsh chemicals or impact tests. You may need a prototype to evaluate human factors such as the force to snap release a plastic cover or bottle cap. You may want to evaluate the ease of assembly and serviceability. Lastly, you may simply want to quickly evaluate a concept at minimal cost. All these situations will lead you to a different prototyping option.
An appearance model does not necessarily require internal features or individual parts. If the part is small — less than a 10-in. cube — it may be ideally suited for FDM printing in ABS. However, if the part is large like a refrigerator, it may be ideally suited for hand fabrication using REN shape or wood. If the refrigerator-sized product has hinged doors and a finished interior, it may be best suited for a combination of methods including FDM, vacuum forming, and wood. It’s important for you, as a designer, to understand how the prototype will be fabricated since you may be required to provide the modelmaker with the CAD files for each part of the overall model. These parts will be very different from the actual production parts.
Aesthetic requirements
Models should be distinguished from prototypes based on their sole purpose to communicate the appearance and aesthetics of a design concept versus the product’s function. Although models may lack internal details, the complexity and skill required to develop a high-quality aesthetic model is quite challenging. The planning and skill levels for the designer as well as the model maker are equally demanding. Designers are required to design parts specifically for a non-functional model vs. a set of production parts. For example, a non-functional model of a product like the one shown below would require the following parts:
Single, hollow fine build FDM or SLA part for the main body
Red and green tinted acrylic window
Front bezel with holes
Inner front bezel ring
Separate blue decorative oval ring
Elastomeric blue trim around display
Black painted clear acrylic insert for display
Separate blue button
The 3D-printed parts would be best suited for a fine build FDM or SLA. The elastomeric trim could be printed in an elastomer using SLA technology, as FDM would yield too rough a surface. Conversely the medical device could be fabricated using a combination of CNC-machined REN shape, FDM, and hand-fabricated sheet.
Lead time – turn-around time
Lead time and turn-around time for fabricating one or more prototypes is often a critical consideration during the development process. Sometimes the fastest method of prototyping something is simply to pick up a tool and cut a piece of plastic into a shape that represents the part and testing it. Although this is not exactly the most accurate method for making a prototype, it is the cheapest, quickest, and most convenient one. Medium to large parts are often much faster to fabricate versus print, especially if they are designed as large planar surfaces. The second fastest method is in-house 3D FDM printing or CNC machining, depending on your equipment. Today, most companies and design firms have in-house 3D printers, which can print medium- to high-quality parts on demand. Independent prototyping facilities will typically convert 3D CAD files into parts based on the following general turn-around times:
Process | Turn-around time |
Rapid prototyping | two days to one week |
Handmade/Fabricated | one to three weeks |
CNC machining | one to two weeks |
Cast | two weeks to one month |
Injection molding | one week to one month |
Vacuum forming | one to three weeks |
Composites | one to three weeks |
It should be noted that the turn-around times listed in the table are realistic general time ranges. Some vendors may be able to respond much faster or slower depending on workload, complexity of the project, and number of parts.
Plastic manufacturing process
Although injection molding is the most popular plastic molding process, there are many other processes available for manufacturing plastic products. Most 3D rapid prototyping is optimized for injection-molded parts, since the tooling investment and part complexity are the most extreme for this process. Other processes like blow molding, vacuum forming, rotational molding, and extrusion are also specified for processing plastic parts. Each process has its own set of unique design criteria, choice of materials, and type of part geometry.
Blow-molded bottles, for example, are typically manufactured in polyethylene (PE), polyethylene terephthalate (PET), or polypropylene (PP). Prototyping a PE blow-molded bottle in a 1-mm wall utilizing any of the rapid prototyping methods is not available today. However, a blow-molded PE bottle can be prototyped by creating an SLS or FDM blow mold and molding a few samples. There are several vendors offering this type of service. The same is true for other plastic molding processes, where the mold is either 3D printed or CNC machined, and a small quantity of parts are molded in the actual material. Prototyping plastic parts based on the actual material and molding process provides you with the most accurate representation of the final production part. Injection-molded prototype parts in the actual material will be almost identical to the production parts. They can be tested and evaluated based on the performance of the specified resin, molded-in stresses, as well as the part tolerances. Large structural foam molded parts are best suited for CNC fabrication or FDM, with a 70% to 80% part density. Since structural foam molded parts are typically large, you may be required to split them into smaller pieces that are printed and assembled into one larger piece.
Tolerances
Plastic parts are often required to comply with very tight tolerances. Tolerances are especially critical for features such as snap fits, press fits, sliding parts, or optical assemblies. Controlling tolerances and surface finish in prototypes is highly dependent on the material, equipment, prototyping process, part size, and build speed. FDM typically yields parts with tolerances ranging from +/- 0.008 to +/- 0.02 in. SLA tolerances are much tighter than FDM parts, yielding parts with tolerances in the range of +/- 0.004 to +/- 0.007 in. SLS parts are like those of SLA. CNC parts can be machined to within +/- 0.0005 in. for reamed holes and +/- 0.002 in. non-cumulative. This is the most accurate prototyping option.
Cast polyurethane or epoxy tolerances are very imprecise because of the number of variables associated with the process. Tolerance stack-ups accumulate starting with the pattern, silicone mold, resin shrinkage, and, finally, secondary handling operations. Tolerances for cast polyurethanes can range from +/- 0.01 to as much as +/- 0.06 in. depending on all the variables previously cited.
Level of detail
One of the big challenges of any prototyping method is accurate rendition of fine design details. Preserving part features is highly dependent on the same parameters previously mentioned, which are listed below:
Prototyping method
Material
Equipment
Part features
3D printing — ratio between material deposit and feature
A brief review of resolution and accurate replication of design features is provided below for each of the prototyping options.
Rapid prototyping – 3D part creation directly from CAD files (top three technologies)
Fused deposition modeling (FDM). Although some FDM machines claim to achieve details down to 10 to 20 microns, it is impractical for most FDM machines to print at this level. The extruder cannot consistently dispense material at these very fine deposit levels. Most FDM machines are therefore ideal for resolutions no greater than 100 microns. Typical extruder bead diameters are 200 microns or 0.2 mm, which limits details to this resolution.
Stereolithography (SLA). Since the SLA process is based on the solidification of a liquid epoxy medium, the resolution is much finer. SLA parts, at a minimum, are 4X finer than FDM parts. SLA layer heights are typically 25 microns or better. This process is preferred for producing very fine detailed parts.
Selective laser sintering (SLS). Part resolution lies somewhere between FDM and SLA. Typical layer resolution is 75 microns.
Handmade/fabricated
Rendition of details of handmade prototypes are obviously dependent on the craftsman. A highly skilled craftsman can exceed the resolution of most rapid prototyping machines; however, most handmade prototypes are crude and very basic. The reasons are obviously based on efficiency, cost, and skill level. This option is therefore at the bottom of the list for accurate replication of design features.
Example of a handmade prototype. |
CNC machining
CNC machining is at the bottom of the list for reproducing fine design details of an injection molded part. There are two major reasons for this ranking. First, most of the features of an injection-molded part cannot be machined from a single block of plastic. CNC machines are restricted by cutter diameters and depth of reach. For example, a two-inch-deep pair of ribs spaced 0.09 in. apart would be impossible to machine from a single block of plastic because there are no 0.09-in.-diameter cutters that are long enough. CNC prototypes, therefore, are separated into many smaller pieces and bonded together to form the intended final part, or injection parts must be redesigned for the CNC machining process.
CNC machined prototypes. |
Casting — polyurethane, epoxy, or silicone
Cast polyurethane is frequently specified as a cost-effective means of replicating five to 100 parts. The reproduction of part features is as good as the original pattern used to create the silicone rubber mold. One should be alerted to the fact that the quality of cast polyurethane parts is highly dependent on the vendor, staff, and QC procedures they employ. Replication of fine details is highly dependent on the casting technique, quality of the mold, and all the secondary operations that are inherent in the process. Although cast parts can replicate details as fine as a fingerprint, the high labor content inherent in this process typically results in very inconsistent quality.
Injection molding — temporary tooling
Temporary injection mold tooling will provide you with prototypes that are virtually identical to the final production parts. It should be noted that the replication of design details is dependent on the tooling quality and processing conditions. This option is also the most expensive and lengthy in turnaround time.
Vacuum forming and composites
Vacuum formed and composite parts are distinctly different from injection-molded parts based on the process, part geometry, tooling, and materials. Prototypes for either of these two processes are typically large parts — greater than 2 x 2 ft — which are basically a surface with mounting features bonded to the rear side after molding. Parts molded in these processes typically don’t have fine details.
The second part of this two-article series, which has now been published, covers the six remaining considerations.
If you have any questions, please feel free to contact me at 516-482-2181 or via email, [email protected].
About the author
Michael Paloian is President of Integrated Design Systems Inc. (IDS), located in Oyster Bay, New York. He has an undergraduate degree in plastics engineering from UMass Lowell and a master's of industrial design from Rhode Island School of Design. Paloian has an in-depth knowledge of designing parts in numerous processes and materials, including plastics, metals, and composites. Paloian holds more than 40 patents and was past chair of SPE RMD and PD3. He frequently speaks at SPE, SPI, ARM, MD&M, and IDSA conferences. He has also written hundreds of design-related articles for many publications. He can be reached by phone at 516/482-2181 or via e-mail, [email protected].
About the Author(s)
You May Also Like